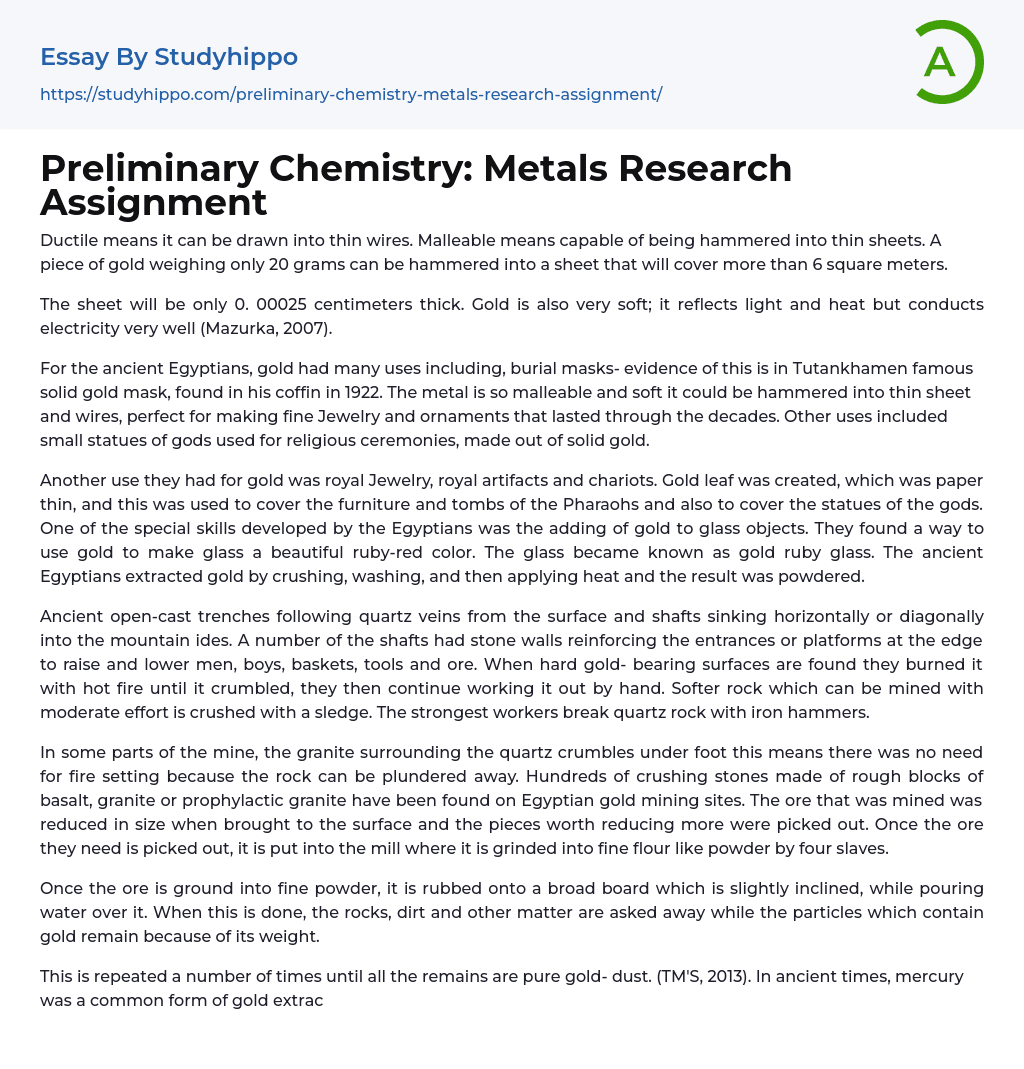
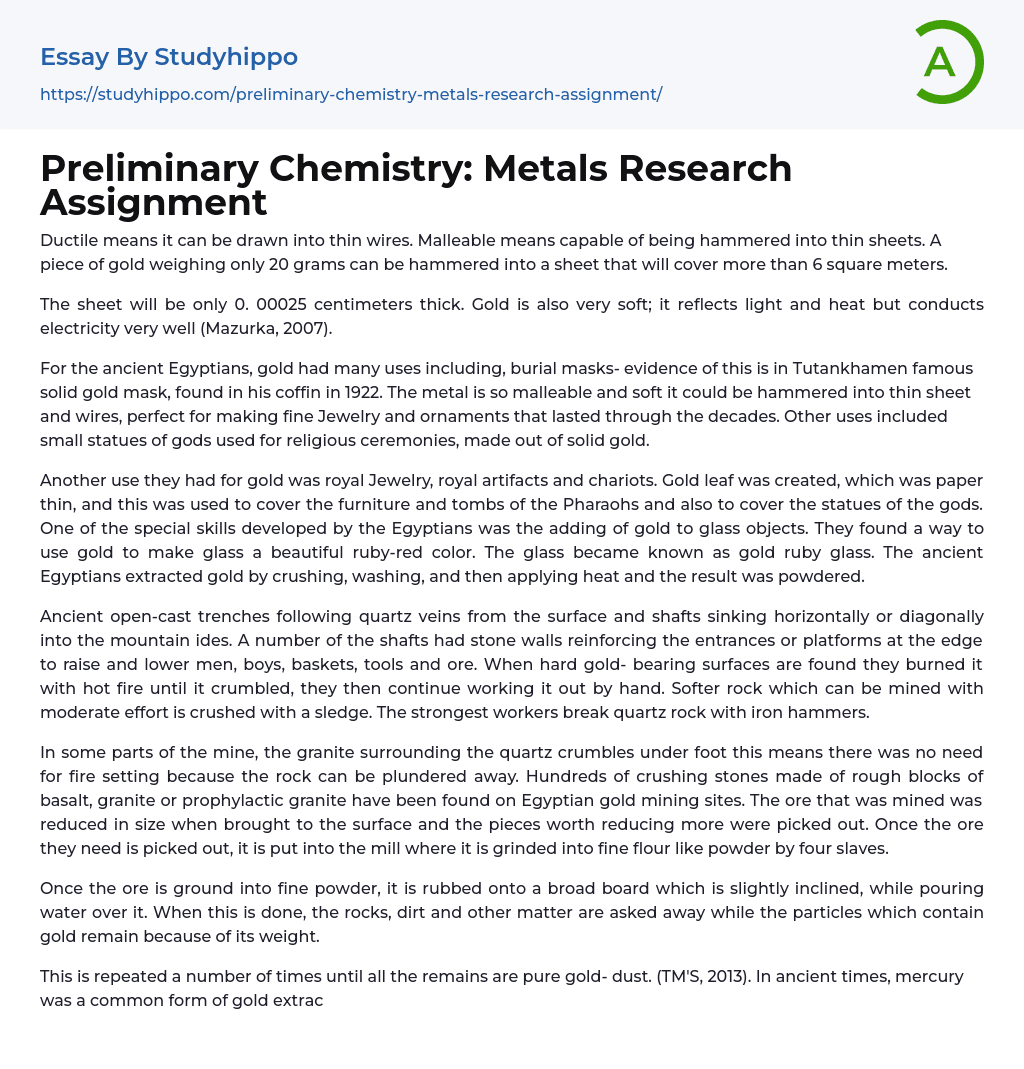
Preliminary Chemistry: Metals Research Assignment Essay Example
Ductile and malleable are terms used to describe different properties of materials. Ductile means that a material can be easily formed into thin wires, while malleable means that it can be easily hammered into thin sheets. For example, a 20-gram piece of gold can be hammered into a sheet that will cover more than 6 square meters with a thickness of just 0.
Gold is a metal that is only 0.00025 centimeters thick and is very soft. It has the ability to reflect light and heat, while also being an excellent conductor of electricity (Mazurka, 2007). The ancient Egyptians utilized gold for various purposes, such as creating burial masks. An example of this can be seen in King Tutankhamen's well-known solid gold mask, which was discovered in his coffin in 1922. Due to its malleability and softness, gold could be easily hammered into thin sheets
...and wires, making it ideal for crafting durable jewelry and ornaments that could withstand the test of time. Additionally, solid gold was employed in the creation of small statues of gods used during religious ceremonies.
Among their various uses, the Egyptians utilized gold for royal Jewelry, royal artifacts, and chariots. They skillfully created gold leaf, an incredibly thin material, to adorn the furniture and tombs of the Pharaohs and statues of the gods. Additionally, they developed the technique of incorporating gold into glass objects, creating stunning ruby-red colored glass known as gold ruby glass.
The Egyptians in ancient times used various methods to extract gold. They crushed it, washed it, and applied heat, which turned it into powder. They dug open-cast trenches along quartz veins on the surface, and they also dug shaft
horizontally or diagonally into the mountain sides. Many of these shafts had stone walls to strengthen the entrances or platforms that were used to transport men, boys, baskets, tools, and ore up and down. When they encountered hard gold-bearing surfaces, they would heat them with fire until they crumbled, and then they would manually continue working on it.
Softer rock that can be easily extracted is crushed using a sledgehammer, while the hardest workers break quartz rock using iron hammers. In certain areas of the mine, the granite surrounding the quartz crumbles underfoot, eliminating the need for fire setting and allowing for the easy extraction of the rock. Numerous crushing stones made of rough blocks of basalt, granite, or prophylactic granite have been discovered at Egyptian gold mining sites. The extracted ore is first reduced in size upon reaching the surface, with the pieces deemed most valuable being selected for further reduction. Once the desired ore is chosen, it is placed into a mill where four slaves grind it into a fine powder resembling flour.
After the ore is ground into a fine powder, it is applied to a slightly inclined broad board and water is poured over it. The rocks, dirt, and other materials are washed away, leaving behind the heavier gold particles. This process is repeated multiple times until only pure gold dust remains. In ancient times, mercury was commonly used for gold extraction until later in the first millennia. (TM'S, 2013).
Mercury, a metal, was discovered in ancient Egyptian ore. Finely crushed gold ore was mixed with liquid mercury, resulting in a coating of mercury on the gold. The coated gold was then burned to
vaporize the mercury and leave behind pure gold (Brooks, 2011). The crystal structure of metallic gold is face centered cubic, which enhances its ductility by facilitating the movement of dislocations within the lattice.
When gold nuggets were not easily found in streams or deposits, the ancient Egyptians invested significant effort into mining their gold. Gold, being a non-reactive metal that does not readily bond with other elements, requires less energy for extraction compared to reactive metals. Nevertheless, the Egyptians still consumed a considerable amount of energy in extracting the ore due to their primitive techniques. Despite this energy expenditure, the Egyptians managed to accumulate more gold than any other civilization of their time. This indicates that their gold mining endeavors were both energetically demanding and highly successful. Gold possesses a cubical crystalline structure with a density of 19.32 grams per cubic centimeter. It forms metallic bonds, where the outer electrons of metal atoms are delocalized and free to move. The metallic bond is the attractive force between these free electrons and the metal ions.
Metallic bonds in gold are strong, resulting in a regular structure and high melting and boiling points (BBC, 2013). The strength of gold's structure also means that it requires significant energy to break down into its pure form, as discovered by the Egyptians. However, gold does not easily react with other elements and is often found in its pure form, requiring minimal energy for refinement.
Aluminum Growth of aluminum production
The metal Aluminum was first discovered and its existence established in 1808 by Sir Humphrey Dad, but he was unable to actually make any. 10 years later, a French scientist discovered hard, red clay containing
over 50% aluminum oxide. It was named bauxite, aluminum's most common ore (Dawson, 2002). After its discovery, extensive research was conducted to find an efficient method to extract the metal from its ore and create a production process that would allow for commercial viability (Unknown, 2008). In 1825, a small lump of aluminum metal was produced for the first time. Then, in 1827, another scientist isolated aluminum as a powder using potassium and anhydrous aluminum chloride. It wasn't until 1854 that the first method for commercial production was invented.
During the Paris exhibition in 1855, a bar of aluminum was showcased when it was more expensive than gold. However, within the following decade, the value of aluminum plummeted by over 90% as new extraction methods were discovered. The production of aluminum reached 8 thousand tons in 1900 and increased to a staggering 31 million tons by 1964. It is worth mentioning that aluminum is derived from bauxite - an example thereof. Notably, aluminum ranks third among the most prevalent elements found in the Earth's crust and is the most abundant metal.
Aluminum is not naturally found in its elemental state but only in combined forms due to its high attraction to bond with oxygen, such as oxides or silicates. The most prevalent form is bauxite, which is a hard, red clay consisting of over 50% aluminum oxide. It belongs to the post-transition metals group on the periodic table, represented by the symbol AH and atomic number 13. Its color is silvery white, and it does not dissolve in water under normal conditions.
According to Wisped (2013), aluminum is naturally found in a reactive state, which is evident from
its position on the periodic table of elements. Positioned within the transition metals group, aluminum shares characteristics with other metals in this group, such as being softer and less effective in conducting electricity. It also has a lower boiling and melting point compared to transition metals. Consequently, aluminum is never found in its pure elemental state due to its reactivity with the environment. This positioning of aluminum with other reactive metals in the post-transition group is reflected on the periodic table of elements.
Aluminum, the second most malleable metal and highly ductile, has low hardness due to its low density. It has a melting point of 660°C and a boiling point of 2519°C, demonstrating high electrical conductivity. Nevertheless, pure aluminum lacks significant strength.
The ductility and malleability of aluminum is attributed to its structure, which contains dislocations. Incorporating additional metals enhances the crystal structure and makes it harder for atoms to move around, prioritizing strength. However, to maintain its low density and light weight, other elements are mixed in to support the dislocations, reducing malleability but increasing strength. Consequently, certain aluminum alloys can exhibit a comparable level of strength as steel. The addition of different elements produces different effects, although nearly all alloys are stronger than pure aluminum alone. Copper is added to enhance strength, hardness, and enable heat treatment.
Manganese is often added to aluminum in order to improve its strength and resistance against corrosion. The presence of silicon lowers the melting point and improves stability, while alloys with zinc are known for increased strength and hardness. What distinguishes these alloys is their ability to retain the lightweight nature of aluminum while acquiring additional properties that aluminum
lacks. Because of these distinctive qualities, aluminum and its alloys are widely used in modern society.
Aluminum is commonly utilized in packaging, such as drink cans, foil wrappings, bottle tops, and foil containers. Its malleability, corrosion resistance, impermeability, and capacity to preserve food aroma and taste make it an ideal packaging material. Additionally, aluminum finds extensive use in the transportation industry. Vehicles constructed from aluminum are lighter and require less energy for movement compared to those made from iron or steel. This includes airplanes, trains, boats, and cars. Moreover, aluminum is employed for power lines due to its lightweight nature and efficient electricity conduction capabilities over long distances without heavy-duty supports.
Aluminum possesses ductility, allowing it to be drawn into power line wires. Its resistance to corrosion results in low maintenance for aluminum buildings. The lightweight nature of aluminum makes it suitable for various uses like cladding, windows, skylights, gutters, door frames, and roofing. Additionally, aluminum finds applications in saucepans, kitchen utensils, golf clubs, tennis rackets, furniture, fridges and toasters (Dawson, 2002). When magnesium atoms are incorporated into the system due to their larger size compared to aluminum atoms (Macmillan., 2010), the presence of an edge dislocation generates a pressure field characterized by hydrostatic tension. However, this dilatation field and overall energy decrease. It is worth noting that pure aluminum lacks strength.
Aluminum is frequently mixed with other metals to boost its strength while still retaining its low density and light weight. These alloys contain additional metals that hinder dislocations, leading to decreased ductility but increased strength. In this way, specific aluminum alloys can match the strength of steel while also maintaining the inherent lightweight characteristic of aluminum.
Different elements are employed to achieve various effects, although nearly all alloys surpass pure aluminum in terms of strength.
Adding copper to aluminum enhances its strength, hardness, and heat treatability. Additionally, it makes it heat treatable. On the other hand, including magnesium in aluminum results in increased tensile strength, resistance to salt water corrosion, and ease of welding. Manganese is commonly incorporated to boost strength and corrosion resistance. Meanwhile, adding silicon decreases the melting point and enhances stability, while alloys with zinc offer improved strength and hardness. These alloy properties greatly enhance the utilization of aluminum.
Most uses for aluminum are in alloyed form, as it is not strong enough when in its pure state. Alloyed aluminum is commonly utilized in cars, airplanes, trains, and buildings. The extraction of aluminum involves the Hall Hereunto Process. Additionally, the industrial-scale Brayer process is used to extract the metal. Firstly, aluminum is mined from the earth due to its abundant presence. Since aluminum is reactive, it is always found combined with other elements in compounds and never isolated. To purify the bauxite, the Brayer process is employed.
This process occurs in two main steps. Initially, the aluminum ore is combined with sodium hydroxide, whereby the oxides of aluminum and silicon will dissolve, while other impurities will not. These impurities can subsequently be eliminated through filtration. Carbon carbonic acid is utilized to neutralize the solution and induce the precipitation of aluminum oxide, while the silicon impurities remain in the solution. Following filtration and dehydration, purified aluminum oxide can be obtained. Once purified aluminum oxide has been produced, aluminum can be extracted from it using the Hall-Hereunto method. The aluminum oxide is mixed
with creosote, a blend of sodium fluoride and aluminum fluoride, and then heated to 980°C to melt the solids.
The temperature required to melt aluminum oxide is much lower, resulting in energy savings. The molten mixture is then electrolyzed with a large current to reduce aluminum ions and form metal. Extracting pure aluminum metal is a time-consuming process that requires a tremendous amount of energy. The most energy-intensive part of the aluminum extraction process is the electrolysis step to reduce ions and form metal. The mixture of aluminum oxide and creosote has a melting point of 950 degrees Celsius, which requires a significant amount of energy on a large scale. (Williams, Unknown). The cost of producing aluminum includes electric power, which accounts for 20% to 40% depending on the smelter's location.
Aluminum production in the U. S. consumes approximately 5% of the total electricity generated (Wisped, 2013). The difficulty in extracting aluminum from aluminum oxide and the high energy requirement result from the strong covalent bonding present. Since aluminum oxide exhibits covalent bonding, its elements are strongly connected and difficult to separate, explaining the time and energy-intensive extraction process for aluminum metal.
The main source of copper ore is porphyry copper deposits, which are abundant. These deposits consist of a mixture of igneous rocks like feldspar, copper, and quartz, and have a characteristic purple-red appearance.
Porphyry copper deposits form when a column of rising magma cools slowly deep into the crust. This process results in the formation of large crystal grains measuring 2 mm or more in diameter. During the final stage, the magma cools rapidly at shallower depths or as it erupts from a volcano, creating small
grains that are usually too small to be seen with the naked eye. These deposits contain multiple cavities made up of diorite to quartz. They can also be found mixed in with rocks composed of fragmented minerals and other rocks. Sulfide normalization often occurs between or within these fragments. Additionally, the deposits typically have an outer layer consisting of calcium aluminum iron (peptide). The most common type of ore found in these deposits are sulfide ores, where the copper is chemically bonded with sulfur.
Oxide ores, carbonate ores, or mixed ores make up the other types of ores based on the chemicals present. The prediction of yield is a crucial step in mining and extracting copper from commercial ore deposits. This is due to the extensive nature of copper mining, where the amount of copper extracted must outweigh the cost of the mining process. Mining activities involve expensive techniques such as drilling, explosive blasting, power shovels, and smelting, which also require significant time investments. As excavating pits for copper can extend to be very long, sometimes even a mile or longer, it is essential to predict the amount of copper that can be obtained so that efforts are not wasted. Predicting yield helps in reducing the number of excavating pits required and minimizes energy consumption. Meanwhile, the most commonly found copper ore is chlorinated, accounting for approximately 50% of copper production.
To obtain pure metal, a specific process is required for extracting the ore. Initially, the mined ore is crushed into small pieces and then ground in a ball mill - a cylindrical container containing metal balls that rotate to pulverize the ore into a fine powder.
Next, the sulfide ore is mixed with reactants (alcohol and hydroxide) in a water-filled aeration tank. As a result, the copper sulfide becomes hydrophobic externally. The tank is aerated with air, causing the copper sulfide to repel the water and adhere to the air bubbles.
The process known as froth flotation involves the rising of air to the water's surface, carrying copper sulfide, which is then separated from the other components of the ore and typically discarded as tailings. This concentrates and purifies copper, resulting in a higher percentage of copper metal in the product, which is approximately 30% copper. Subsequently, the copper sulfide is subjected to smelting.
The material is combined with silica and limestone and heated to a temperature of 12000C. This process separates the copper from other elements that are bonded to it. The leftover waste substance is known as slag and can be either discarded or further processed to extract more copper. The resulting molten copper is referred to as copper matte, which consists of approximately 70% copper in the form of copper sulfide and iron sulfide. To eliminate the sulfur from the matte, oxygen is introduced into the liquid mixture, combining with CUSS to create cue and SASS. The final product contains nearly 98% copper and is commonly referred to as a blister due to the cracks on its surface caused by the release of sulfur dioxide.
- Steel essays
- Acid essays
- Calcium essays
- Carbohydrate essays
- Carbon essays
- Chemical Bond essays
- Chemical Reaction essays
- Chemical reactions essays
- Chromatography essays
- Concentration essays
- Copper essays
- Diffusion essays
- Ethanol essays
- Hydrogen essays
- Organic Chemistry essays
- Osmosis essays
- Periodic Table essays
- Ph essays
- Salt essays
- Sodium essays
- Titration essays
- Bank essays
- Banking essays
- Corporate Finance essays
- Credit Card essays
- Currency essays
- Debt essays
- Donation essays
- Enron Scandal essays
- Equity essays
- Financial Accounting essays
- Financial Crisis essays
- Financial News essays
- Financial Ratios essays
- Financial Services essays
- Forecasting essays
- Foreign Exchange Market essays
- Free Market essays
- Gold essays
- Investment essays
- Legacy essays
- Loan essays
- Market Segmentation essays
- Money essays
- Personal finance essays
- Purchasing essays
- Retirement essays
- Shareholder essays
- Stock Market essays
- Supply And Demand essays