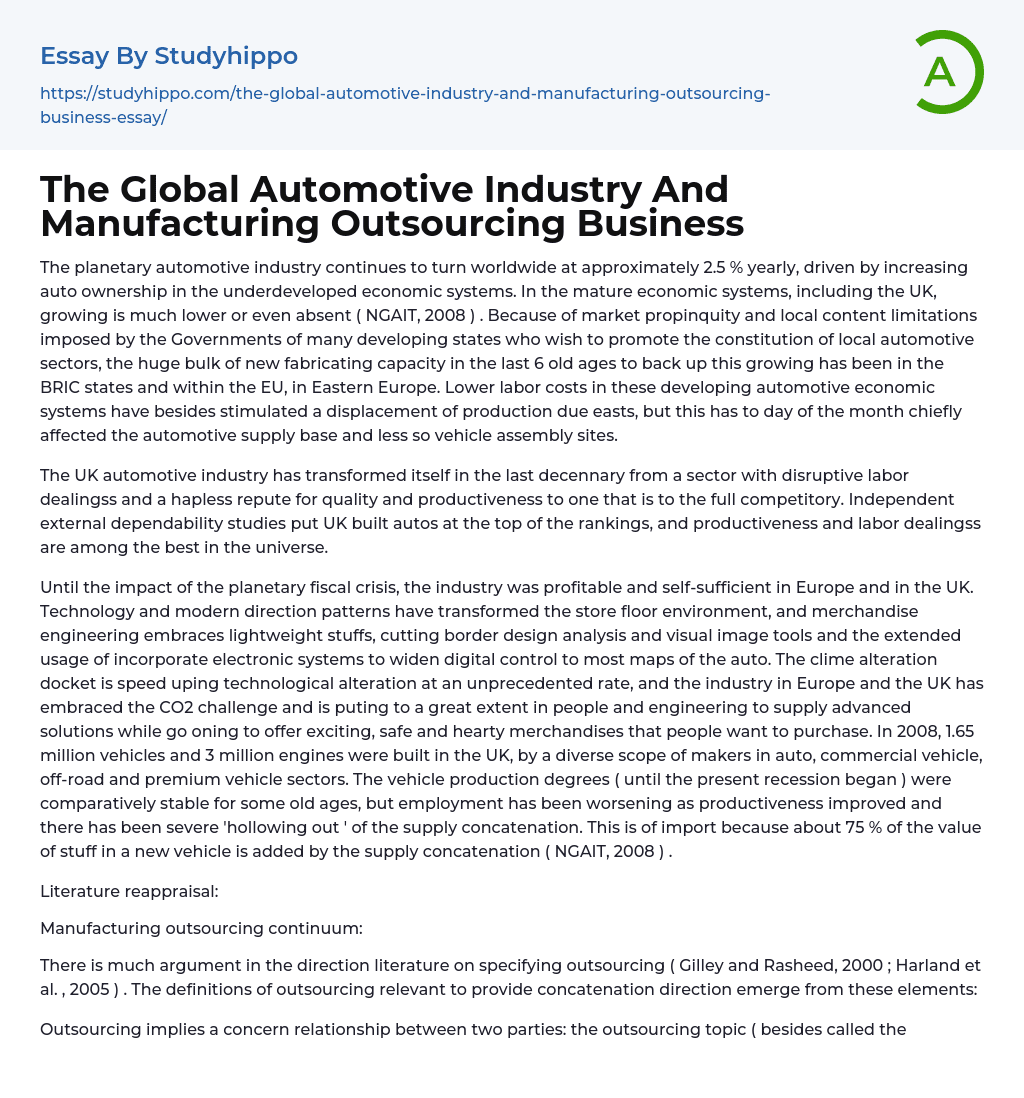
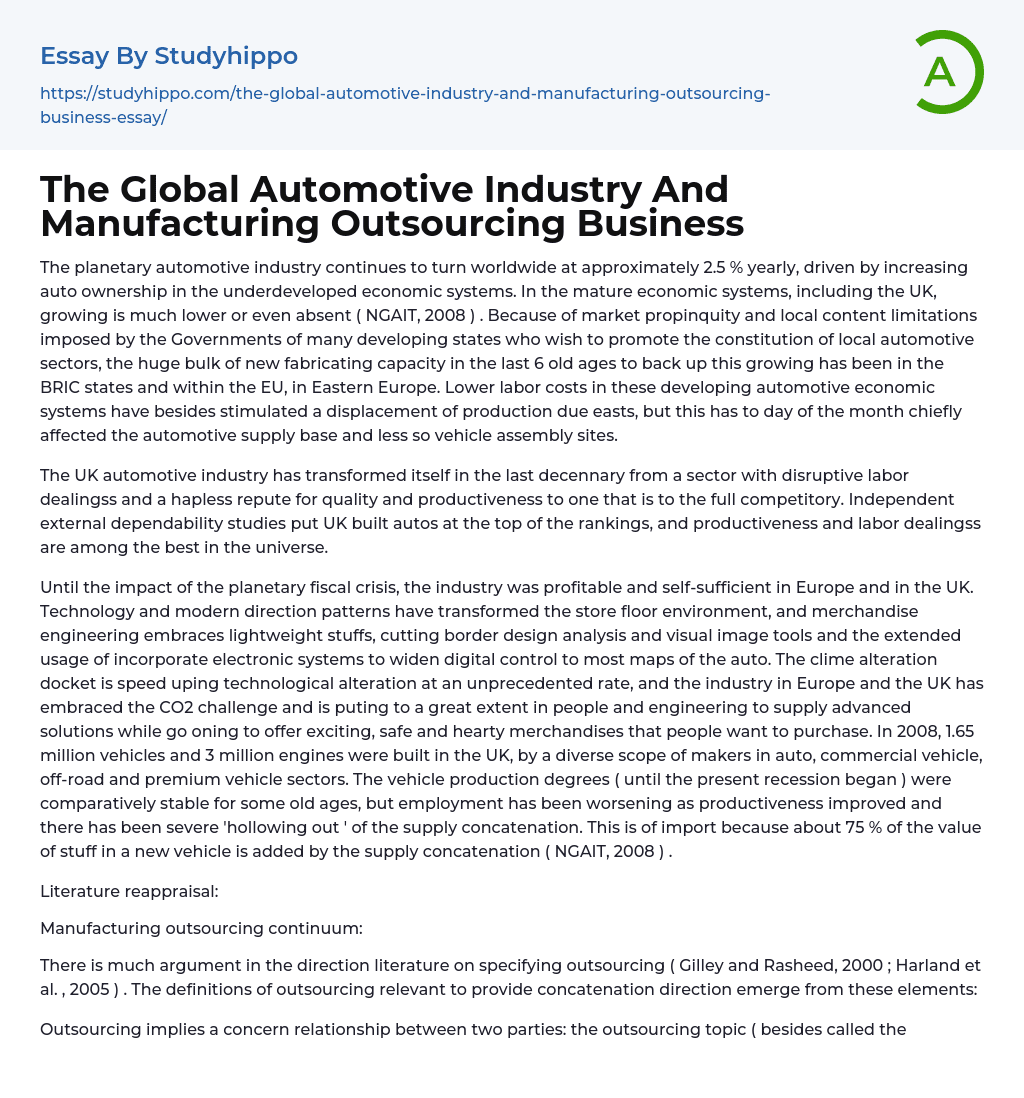
The Global Automotive Industry And Manufacturing Outsourcing Business Essay Example
The global automotive industry is experiencing growth at a rate of approximately 2.5% per year. This growth is driven primarily by increasing car ownership in underdeveloped economies. However, mature economies such as the UK are seeing lower or no growth due to market proximity and local content restrictions imposed by developing countries' governments. These restrictions aim to promote their own automotive sectors.
As a result, most new manufacturing capacity over the past six years has been located in the BRIC countries and Eastern Europe within the European Union. The lower labor costs in these developing automotive economies have also caused production to shift towards the east, mainly impacting the automotive supply base rather than vehicle assembly sites.
Despite these shifts, there have been significant improvements in the UK's automotive industry in recent years. It has transformed from a sector with labor disputes and a poor reputat
...ion for quality and productivity into one that is highly competitive. Cars built in the UK consistently rank as top performers according to external reliability studies, and productivity and labor relations are among the best globally.
Both Europe and the UK's automotive industries were profitable and self-reliant before the global financial crisis occurred. The utilization of technology and modern trends has transformed store floor environments, implementing lightweight materials, cutting-edge design analysis, and visual image tools in merchandise engineering.
Integrated electronic systems are increasingly being used in the automotive industry to expand digital control in vehicles. The urgency surrounding climate change is driving rapid technological advancements in Europe and the UK, leading to heavy investments by the automobile sector to reduce CO2 emissions while still offering desirable, safe, and reliable products. In 2008, different sector
within the UK manufactured a total of 1.65 million vehicles and 3 million engines, including automobiles, commercial vehicles, off-road vehicles, and premium vehicles. However, there has been a decline in employment due to increased productivity and reductions in the supply chain. This decline is significant as approximately 75% of the material value in a new vehicle comes from the supply chain (NGAIT, 2008).
Literature review:
Manufacturing outsourcing continuum:
Ongoing management literature debates exist on how to define outsourcing (Gilley and Rasheed, 2000; Harland et al., 2005). The concept involves two main elements: the decision-making party (also known as the principal or client) who determines whether to outsource or not, and an external outsourcing company.Outsourcing refers to the delegation of various business processes and their outcomes, including manufacturing, sales, R, maintenance, accounting, IT, and logistics. It is a strategic choice that goes beyond simple purchasing decisions to avoid internalizing certain activities. There are two scenarios in which outsourcing occurs: when the client outsources objects initially sourced internally or when the client chooses to outsource objects that could have been done internally. These outsourced objects are specific to each individual client and are executed based on the provided program, specification, form, or design. Acquiring standardized components without customization does not qualify as outsourcing. The client has flexibility in deciding whether to outsource an entire process or only parts of it. Manufacturing outsourcing specifically involves delegating tasks related to specific parts/components or the final product itself. In the 1990s, there was a significant increase in companies engaging in outsourcing activities (Kimura, 2002; Van Mieghem, 1999; Webster et al., 1997; Gilley et al., 2004; Harland et al., 2005).The
rise in outsourcing services, such as auditing, maintenance, repairs, transportation, janitorial work, and legal services, can be attributed to advancements in information technology that have reduced transaction costs (Abraham and Taylor, 1996). This has led to substantial growth in business-related services over the past decade (Fixler and Siegel, 1999). Additionally, manufacturing companies have also outsourced internal production along with these services. For example, major auto makers often rely on external providers for parts assembly within the automotive industry. These international outsourcing practices are closely tied to globalization (Feenstra and Hanson ,1996).
The academic literature extensively discusses various aspects of outsourcing. Coase's influential paper from 1937 and subsequent works by Grossman and Hart (1986), Bolton and Whinston (1993), and Grossman and Helpman (2002) explore a company's decision-making process regarding whether to produce in-house or outsource. These studies primarily focus on transaction costs and incomplete contracts that determine either vertical integration or specialization.
Lyons (1995) applies this theory to examine the significance of transaction costs in firms' outsourcing decisions. The literature has increasingly focused on how trade influences outsourcing.Trade models, such as those by Deardorff (2001), Jones and Kierzkowski (2001), and Kohler (2001), analyze the effects of trade in "discrete products" on specialization patterns among countries and its implications for factor prices. Recent studies by Feenstra and Hanson (1996, 1999) and Gorg et al.(2001) investigate the impact of international outsourcing on comparative rewards and labor demand using industry level data for the US and UK respectively. These studies align with traditional HOS trade theory, finding that international outsourcing, which entails relocating low-skill intensive production to countries with abundant low-skill labor, boosts demand and wages for high-skilled workers in both
nations. Egger and Egger (2001) explore how outsourcing affects productivity of low-skilled labor in the EU using industry level data. They discover that although short-term outsourcing initially decreases productivity for low-skilled labor, it ultimately has a positive long-term effect.
Various studies have investigated the motives and benefits of manufacturing outsourcing. Abraham and Taylor (1996) found that outsourcing offers cost savings, uncertainty transfer, and access to specialized skills and inputs. Kakabadse and Kakabadse (2000) identified economic advantages, improved quality through skilled providers, and innovation as reasons for outsourcing.Bendor-Samuel (1998) proposed that outsourcing offers advantages in terms of cost savings, process expertise, capital access, and advanced technology. This combination enables outsourced tasks to be performed more efficiently than internal departments. Additionally, outsourcing allows companies to be flexible in adopting new technologies or fashion goods/components of complex systems (Carlson, 1989; Harrison, 1994). By outsourcing engineering services externally, companies can save money on replicating these services internally. Moreover, forming a network of providers grants companies the ability to adjust production capabilities based on changing demand for increased flexibility compared to vertically integrated organizations (Carlson 1989; Harrison 1994).
Outsourcing in manufacturing has the potential to expedite product and process design and development by leveraging multiple top-tier providers concurrently (Quinn and Hilmer, 1994). However, critics express concerns about the drawbacks of outsourcing. They argue that it can result in a loss of management control, reduced flexibility, and increased costs. To remain competitive while outsourcing, effective supplier management is crucial in order to prevent the transfer of critical functions or excessive dependence on suppliers for daily business operations.
Furthermore, outsourcing introduces new risks such as skill loss, inadequate skill development, diminished cross-functional capabilities ,and decreased
supplier control (Domberger ,1998; ).Quinn and Hilmer (1994) discuss the potential loss of flexibility that can arise from long-term outsourcing contracts. These contracts may be inflexible and unsuitable for the changing business environment, which can include technological advancements, shifts in competition, and changes in regulations. Despite the initial expectation of cost reduction, evidence suggests that outsourcing does not always lead to decreased costs and can even result in increased expenses. A survey by the PA Consulting Group found that only 5% of organizations achieved significant economic benefits from outsourcing, while 39% reported mediocre benefits. Additionally, outsourcing also has social and organizational costs as it requires redefining boundaries within an organization and making structural adjustments. While some of these costs can be mitigated through staff retraining and reassignment within the organization, there are still significant expenses associated with transporting employees to the provider organization and providing redundancy payouts.
Moreover, outsourcing can result in conflicts between employers and employees, leading to decreased morale, trust, and productivity. The management of global supply chains is particularly challenging due to the distances involved. This not only leads to increased transportation expenses but also complicates decision-making processes because of longer lead times in the supply chain, which in turn results in trade-offs regarding inventory costs. Different local cultures, languages, and practices when dealing with international suppliers or providers reduce the effectiveness of various business processes such as demand prediction and material planning. Developing countries face challenges related to transportation infrastructure, telecommunications infrastructure, worker skills, supplier availability and quality, equipment, and technology that are not commonly encountered by developed countries. These difficulties limit the competitive advantage of a global supply chain.
When companies decide
to outsource activities, they typically compare the market price for outsourced tasks with internal marginal costs. The impact of outsourcing on company performance remains uncertain. Some studies have discovered that companies underestimate the costs associated with outsourcing and may even bring back previously outsourced tasks due to issues with quality or inadequate investments. Limited research has been conducted on the efficiency effects of outsourcing on companies;The impact of outsourcing on product market performance should be taken into account. Even if a company's efficiency remains unchanged after outsourcing internal production, using higher quality intermediate inputs can enhance the final product's quality and result in increased sales and greater profit margins. The limited availability of relevant micro data might explain the lack of empirical studies on the relationship between outsourcing and firm performance. Theoretical considerations suggest that efficient firms allocate their resources within the value chain based on activities where they have a comparative advantage (Shank and Govindarajan, 1992). These firms typically outsource activities that do not offer such advantages to external providers. When deciding to outsource, companies evaluate the productivity of their in-house service functions and choose to outsource if others can provide comparable services at lower costs. Essentially, by outsourcing activities related to product/service production, firms adopt a business strategy centered around "core competences" - a set of skills and knowledge that help them maintain their competitive advantage when serving customers (Porter, 1985; Sharpe, 1997). Consequently, cost savings are expected compared to internal production or service functions. This is particularly true if outside providers benefit from specialized knowledge and/or economies of scale (Heshmati, 2002).Recent research conducted by Grossman and Helpman in 2002 has revealed that
when making a decision between continuing internal production or outsourcing, factors beyond production cost differences must be taken into consideration. According to transaction cost economics, the advantages of outsourcing only apply when the costs associated with asset specificity, incomplete contracts, and search efforts are lower than the advantage gained from production costs (Williamson, 1971). Additionally, the attractiveness of outsourcing for a manufacturer may depend on the availability of potential suppliers that can provide necessary inputs. Furthermore, several case studies have demonstrated that managers often overestimate the benefits while underestimating the transaction costs involved in outsourcing (Benson, 1999; Gornig and Ring, 2000; Young and Macneil, 2000).
A comprehensive perspective on the outsourcing process is provided by Wasner (1999) through a combination of literature review and two independent case studies in the Swedish aircraft industry (Saab AB) and electronics industry (Ericsson Radio Systems AB and Swedform Metall AB). The first case study discusses the outsourcing of aircraft sub-systems followed by subsequent insourcing of related software activities. Meanwhile, the second case study explores outsourced wireless base station production. However, according to Wasner's findings interdependencies at an operational level make transferring an internally controlled activity to external management equally challenging.The effects of outsourcing have a notable impact on various aspects such as physical, temporal, and organizational perspectives. When control is handed over to an external provider, there is inherent complexity in terms of physicality. Furthermore, assessing how circumstances may change over time presents temporal challenges. Moreover, the organization faces challenges in converting strategic decisions into operational actions and transferring functions from one entity to another.
- Finance essays
- International Business essays
- Macroeconomics essays
- Barriers To Entry essays
- Microeconomics essays
- Pricing essays
- Profit essays
- Consumerism essays
- Export essays
- Free Trade essays
- International Trade essays
- Compensation essays
- Monopoly essays
- Trade essays
- Industry essays
- Warehouse essays
- Economic Development essays
- Economic Growth essays
- Inflation essays
- Taxation essays
- Central Bank essays
- Monetary Policy essays
- Economy essays
- Gross Domestic Product essays
- Recession essays
- Capitalism essays
- Economic System essays
- Materialism essays
- World economy essays
- American Dream essays
- resources essays
- Max Weber essays
- Employment essays
- Minimum Wage essays
- Unemployment essays
- Human Development essays
- Income Inequality essays
- Economic Inequality essays
- Money essays
- Financial Accounting essays
- Market Segmentation essays
- Supply And Demand essays
- Purchasing essays
- Forecasting essays
- Legacy essays
- Bank essays
- Corporate Finance essays
- Financial News essays
- Financial Ratios essays
- Financial Services essays