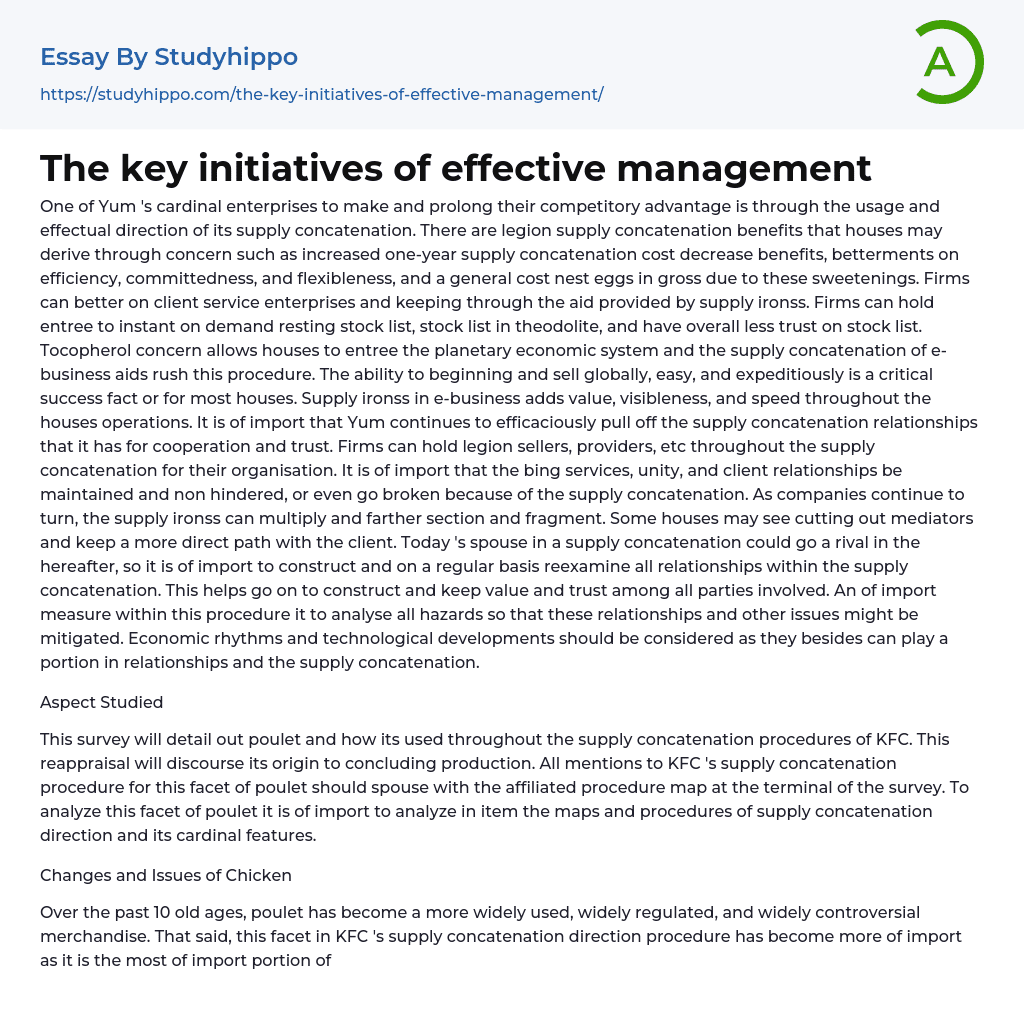
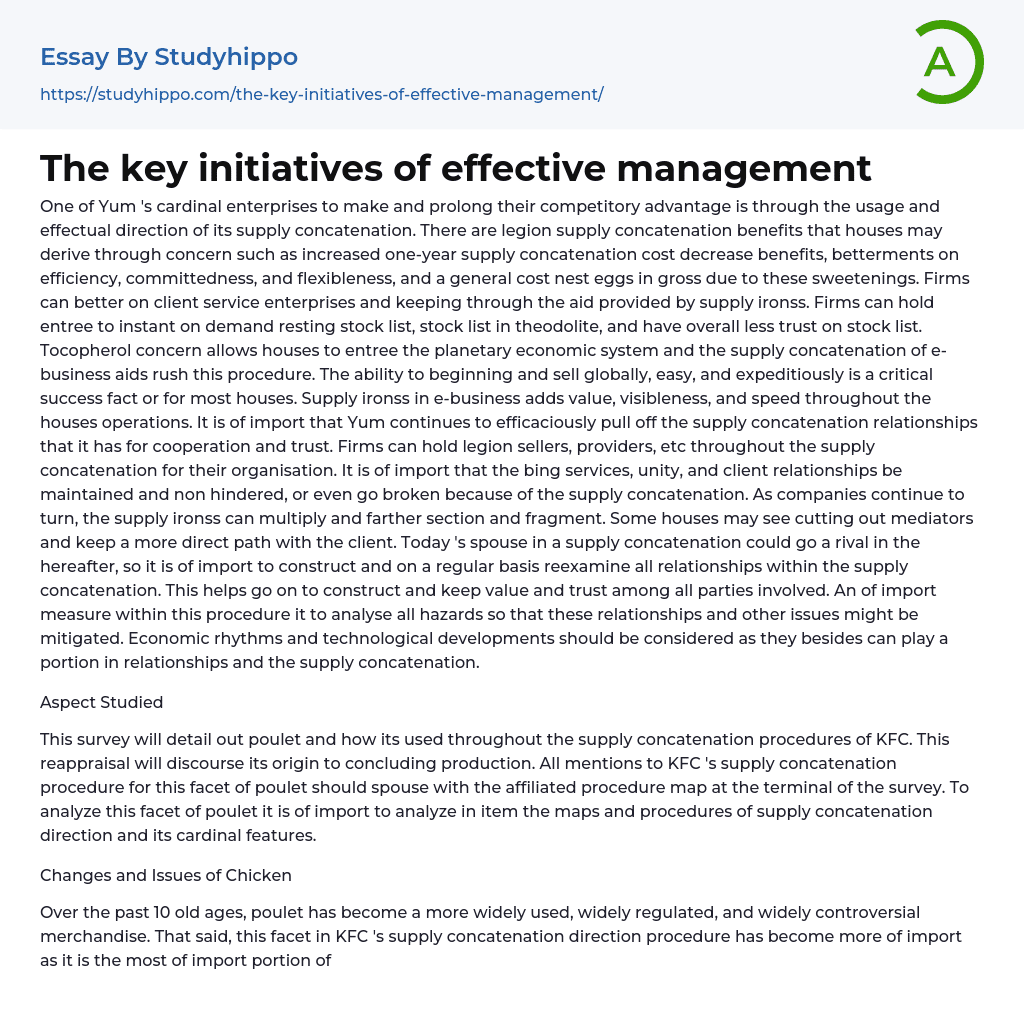
The key initiatives of effective management Essay Example
Yum relies on efficient supply chain management as its main strategy to gain and maintain a competitive advantage. The use of supply chains offers various advantages such as cost reduction, increased efficiency, greater commitment and flexibility, and overall revenue savings. Leveraging supply chains enables businesses to improve customer service and maintenance activities.
E-commerce enables firms to conveniently access real-time inventory, including inventory in transit, and decrease their reliance on inventory. This is made possible by accessing the global economy and the supply chain. Efficiently sourcing and selling on a global scale is crucial for numerous businesses, as e-commerce supply chains enhance value, visibility, and operational speed.
It is crucial for Yum to maintain effective management of its supply chain relationships based on cooperation and trust. Organizations may have multiple vendors, suppliers, and others involved in
...their supply chain. It is important that the existing services, integrity, and customer relationships are preserved and not compromised or disrupted by the supply chain. As companies grow, the supply chains can expand, resulting in increased segmentation and fragmentation.
Some houses may choose to eliminate intermediaries and establish a more direct connection with their clients. Today, a business's partner in a supply chain could become a competitor in the future, so it is crucial to build and regularly review all relationships within the supply chain. This helps in creating and maintaining value and trust among all parties involved. An important step in this process is to analyze all risks, which can help in mitigating these relationships and other issues. Economic cycles and technological advancements should also be taken into consideration, as they can impact relationships and the supply chain.
Aspect Studied
This study will focu
on chicken and its usage throughout the supply chain processes of KFC.
This article will discuss the origins and final production of KFC's chicken. Any references to KFC's supply chain process for this aspect of chicken should be in line with the affiliated process map at the end of the study. To examine this aspect of chicken, it is crucial to closely analyze the functions and procedures of supply chain management and its key characteristics.
Changes and Issues of Chicken
Over the past decade, chicken has seen increased usage, tighter regulation, and significant controversy. Consequently, this aspect of KFC's supply chain management process has become more important as it represents the core of their business.
Chicken is the second most consumed meat product globally. Hence, it is crucial to analyze supply chain providers and manufacturers, as well as just-in-time (JIT) and delivery processes to meet the demand for this product. The affordable price of chicken leads to a surge in demand. Moreover, external factors like beef production and escalating costs of beef and other meats also contribute to the heightened demand for chicken, leading to a decrease in supply. Additionally, regulatory requirements for chicken production and handling should be taken into account.
In the past 10 years, technology advancements have allowed for the enhancement of bird production through the use of steroids and hormones. However, this has sparked controversy as it raises health concerns and prompts demands for free-range or organic birds. In managing the supply for its stores, KFC must address these concerns, as they directly impact the supply and demand of chicken. Additionally, KFC must also analyze the consumption of chicken.
The poulet is not only used for
meat production, but also for the growth of other chickens, feed, and fertilizer. KFC needs to assess its suppliers within its supply chain to ensure that they follow YUM's code of ethics. This guarantees that partners are producing and exporting chickens in an acceptable manner, preventing negative publicity or similar issues.
Supply Chain Detailed
Supply chain management (SCM) is the combination of art and science involved in improving how a company obtains the raw materials necessary for a product or service and delivering it to customers. SCM is crucial in business. The term SCM refers to the interconnectedness of organizations as seen from a particular company's perspective.
Many companies have achieved significant success through unique methods of organizing their supply chains. Planning supply chain operations is a crucial activity for the success of any organization. Delays in operational plans can have an impact on the strategic plans for the organization. If there are delays in sourcing or securing supplies of raw materials, work-in-progress, components, finished goods, and merchandise for resale, this can result in lower than expected revenues and affect overall profitability within a certain timeframe (Hines, 2004). Two measures of supply chain efficiency are inventory turnover and weeks of supply.
The successful operation of a company relies on efficient processes for functional products and responsive processes for advanced products. This requires integrating supply chain strategy with product features. When making decisions about sourcing, production, and distribution, companies must consider the costs associated with materials, transportation, production, warehousing, and distribution. The goal is to create a comprehensive network that minimizes expenses. The five key components of supply chain management are:
Planning, Sourcing, Making, Delivering, and Returning.
This section focuses on the
strategic aspect of supply chain management. It requires developing a strategy to effectively manage all resources involved in meeting customer demand for a product or service. Creating a set of metrics during the planning phase is essential for overseeing the supply chain. This ensures efficiency, cost-effectiveness, and delivering high-quality products and value to customers.
Sourcing
The sourcing process involves selecting providers who can provide the necessary goods and services. It also includes establishing pricing, delivery, and payment procedures with these providers. Additionally, it is important to create metrics for monitoring and improving relationships with providers. Finally, procedures should be developed for managing inventory received from providers, such as receiving shipments, verifying them, transferring them to manufacturing facilities, and authorizing payments to suppliers.
Making
The making process refers to the manufacturing stage. This includes scheduling activities required for production, testing, packaging, and preparing for delivery. It is a highly metric-intensive phase of the supply chain, where quality levels, production output, and worker productivity are measured.
Delivery
This is the part that experts commonly refer to as "logistics." It involves coordinating order reception from clients, establishing a network of warehouses, selecting carriers to deliver goods to clients, and implementing an invoicing system for payments.
Returns
Creating a system for receiving faulty and excess merchandise from clients and providing support for customers who encounter issues with delivered products. Among these five fundamental components, "sourcing" is the most crucial one, as it connects all the other elements. The goal of sourcing is to identify and select a Supplier whose costs, qualities, technologies, timeliness, reliability, and service best
align with the company's needs. Strategic Sourcing is a systematic process that guides a Supply Manager's plan to manage and develop the supply base in accordance with the company's strategic objectives.
The application of current best patterns is used to fully integrate providers into the long-term business process. The approach known as Just-in-time is an inventory strategy implemented to optimize the return on investment by reducing in-process inventory and associated carrying costs. To achieve JIT, the process relies on signals from other parts of the process. By following a series of signals, JIT can result in significant improvements in a manufacturing organization's return on investment, quality, and efficiency. Some argue that "Just on Time" would be a more fitting name, as it emphasizes the importance of production timing to meet demand exactly when needed.
A crucial aspect of JIT and inventory reduction is quickly communicating the consumption of old stock that prompts the ordering of new stock. This helps to save warehouse space and costs. However, when stock levels are determined by historical demand and there is a sudden increase in demand beyond the historical average, the company will use up inventory faster than usual and experience customer service issues. JIT specifically targets inventory as one of the seven wastes (overproduction, waiting time, transportation, inventory, processing, motion, and product defects), and therefore its implementation involves the philosophical aim of reducing input buffer inventory to zero. Zero buffer inventory means that production is vulnerable to external shocks.
Exogenic shocks can reduce input supply, which has a strong impact on production. This can lead to negative consequences such as slow or halted production. Safety stock is a buffer stock
held below the cycle stock level to prevent stock-outs. It serves as a protection against uncertainties in supply and demand, and is defined as extra inventory units carried to avoid potential stock outs.
When an organization cannot accurately predict demand and/or lead time for a product, safety stock is implemented. For instance, if a manufacturing company frequently experiences stock shortages, they would need to keep additional inventory on hand to meet demand while producing more inventory. Safety stock can serve as an indicator for a new company to assess the accuracy of their forecasts in the initial years, especially when used strategically alongside a materials demand planning worksheet. By utilizing an MRP worksheet, one can determine the production quantity required to reduce reliance on safety stock.
Reducing safety stock is a common strategy to maintain low costs, especially for companies with limited financial resources or operating with thin manufacturing.
Lead Time and Inventory Control
Lead time refers to the duration between the initiation and completion of a production process. For example, when ordering a new car from a manufacturer, the lead time can range from 2 weeks to 6 months. In the industry, reducing lead time is crucial for lean manufacturing.
To achieve inventory control, it is important to keep proper records and have a system that activates these records for informed decision-making.
The excessive prioritization of record keeping should be avoided. Instead, the emphasis should be on the actions taken using the records, rather than the records alone. Furthermore, a designated individual should be granted authorization to oversee inventories for a certain number of items. This person will operate within the guidelines established by top management regarding which inventories to
maintain. However, there is considerable flexibility within these guidelines, and by strategically requisitioning, this individual can significantly decrease inventory levels. Reducing inventory levels results in cost savings. Ultimately, achieving profitability is the primary goal in business.
By ensuring that stock lists are balanced, he not only reduces the quantities carried but also puts the company in a more flexible position. The ability to change is important in modern industry. The inventory control group has the responsibility to ensure that the company is always ready to meet the ever-changing sales landscape.
Sourcing to Delivery
In a global company producing over one hundred million branded items every day, the Supply Chain plays a significant role in determining success.
A calling in Supply Chain provides a wide range of opportunities and a lot of responsibility. Our Supply Chain manages all phases of the process known as 'plan, source, make and deliver' - from sourcing raw materials to ensuring that products are delivered on time to keep supermarket shelves and cabinets well stocked. Here are some of the roles you could have at each stage:
Manufacturing
Manufacturing takes place in either own or third-party factories and has two sub-processes: processing and packaging. The challenge here is to ensure products and packaging are made as efficiently as possible and helps factories adapt to changing consumer demands. The manufacturer will be responsible for designing, building, and maintaining high-speed production lines.
Processing
If we closely observe the processing practices at KFC, the most important aspect is to maintain the food hygienic. The majority of the process consists of cooking chicken and fish which is done continuously. Large fryers are used for cooking chicken and fish on a large scale, and
after frying, they are placed in preheated glass ovens.
Inventory Management
The management of inventory is important for a company as it allows them to keep track of natural materials, work in progress, or finished products. Inventories serve various purposes such as mitigating supply and demand uncertainties, taking advantage of economies of scale in manufacturing or acquiring products in large quantities. Moreover, inventories are crucial for building reserves for seasonal demands or promotional sales. The challenges of inventory management include the costs of maintenance, shortages, and demand distributions for specific products at detailed stock levels.
Sourcing
Sourcing is the initial part of the Supply Chain and involves the acquisition of both raw materials and packaging materials.
Astute sourcing of items and goods has the potential to significantly reduce costs. In this role, you will be responsible for managing the relationship between our suppliers and our business, which includes contributing to the introduction of new product innovations. Sourcing enhances the value we receive from suppliers. Vendor development refers to any activity undertaken by a purchasing organization to improve a supplier's performance and capabilities in meeting the purchasing organization's supply needs.
Outsourcing
Outsourcing involves transferring the management and daily operations of an entire business function to an external service provider. The client organization and the provider enter into a contractual agreement that outlines the services being transferred.
The provider obtains the means of production from the client, which may include the transportation of people, assets, and resources. The client commits to using the services of the provider for the duration of the contract. Commonly outsourced business sectors include information
technology, human resources, facilities management, real estate management, and accounting. KFC selects providers globally for its dry goods and other items, but for about 70 to 80 percent of its products, particularly chicken, it relies on local farmers. For beverages, it partners with Pepsi, while local companies and its own vehicle fleet provide logistical support. KFC also establishes suppliers within the country and aims to strengthen and enhance their capabilities.
The main purpose of outsourcing is to increase profits and create a comprehensive web design that reduces costs. Managing this process within the supply chain enables YUM brands, particularly KFC, to maintain a strong competitive advantage. YUM brands enforces a specific code of conduct for suppliers, which includes compliance with all relevant laws, codes, and regulations. These encompass local, state, and federal laws regarding wages, benefits, workers' compensation, working hours, equal opportunity, worker safety, and product safety.
Yum besides expects that Suppliers will conform their patterns to the published criterions for their industry. '' They further province, `` KFC has had an carnal public assistance policy for a figure of old ages. In 2000, KFC adopted specific, comprehensive public assistance public presentation criterions for processing poulets and audits its providers against those criterions. As shown below, KFC 's processing guidelines and audits are designed to pull off and supervise each measure of the procedure to find whether the birds supplied to KFC are handled humanely and any agony is minimized. KFC audits its providers for conformity, and non-compliance could ensue in expiration of the provider 's contract.
KFC 's policies for its suppliers cover all chicken that is intended to be sold to KFC. '' (
KFC, 2010 ) .
KFC and Supply Chain Risks
There are a number of external factors that pose risks to KFC's supply chain management practices. These risks can affect every step of the supply chain as chicken moves throughout it. Farmers and other primary suppliers may have a batch of chickens that is not up to standard, leading to insufficient supply for stores. Additionally, suppliers of oil, breading, spices, and other raw materials may experience production losses, resulting in stores being unable to fully produce their products.
Local employees may face a potential loss of work, although this poses no significant threat to the supply chains. However, it is important to take this into consideration. Transportation procedures could be hindered due to faulty equipment or adverse weather conditions. Government regulations could also impact the growth, production, and shipment of chicken to KFC facilities.
Conclusion
This study has examined the role of chicken and its movement within the KFC supply chain. As the process map illustrates, KFC must analyze various aspects of the supply chain, ranging from external suppliers to internal factors such as distribution and final production.
Supply and demand have a significant impact on KFC's supply chain management processes, and numerous external factors and risks directly affect this. According to the study, KFC is utilizing numerous local suppliers and upholding a strict code of ethics and supply policy. It also has a comprehensive animal welfare policy and ensures thorough analysis and planning across all aspects of its supply chain. This management approach is resulting in improved profits, customer and stakeholder satisfaction, and subsequently increasing the company's bottom line.
- Chief Executive Officer essays
- Convenience Store essays
- Firm essays
- Training And Development essays
- Unilever essays
- Variable Cost essays
- Virgin Group essays
- Bargaining essays
- Entity essays
- Pest analysis essays
- John Locke essays
- 9/11 essays
- A Good Teacher essays
- A Healthy Diet essays
- A Modest Proposal essays
- A&P essays
- Academic Achievement essays
- Achievement essays
- Achieving goals essays
- Admission essays
- Advantages And Disadvantages Of Internet essays
- Alcoholic drinks essays
- Ammonia essays
- Analytical essays
- Ancient Olympic Games essays
- APA essays
- Arabian Peninsula essays
- Argument essays
- Argumentative essays
- Art essays
- Atlantic Ocean essays
- Auto-ethnography essays
- Autobiography essays
- Ballad essays
- Batman essays
- Binge Eating essays
- Black Power Movement essays
- Blogger essays
- Body Mass Index essays
- Book I Want a Wife essays
- Boycott essays
- Breastfeeding essays
- Bulimia Nervosa essays
- Business essays
- Business Process essays
- Canterbury essays
- Carbonate essays
- Catalina de Erauso essays
- Cause and Effect essays
- Cesar Chavez essays