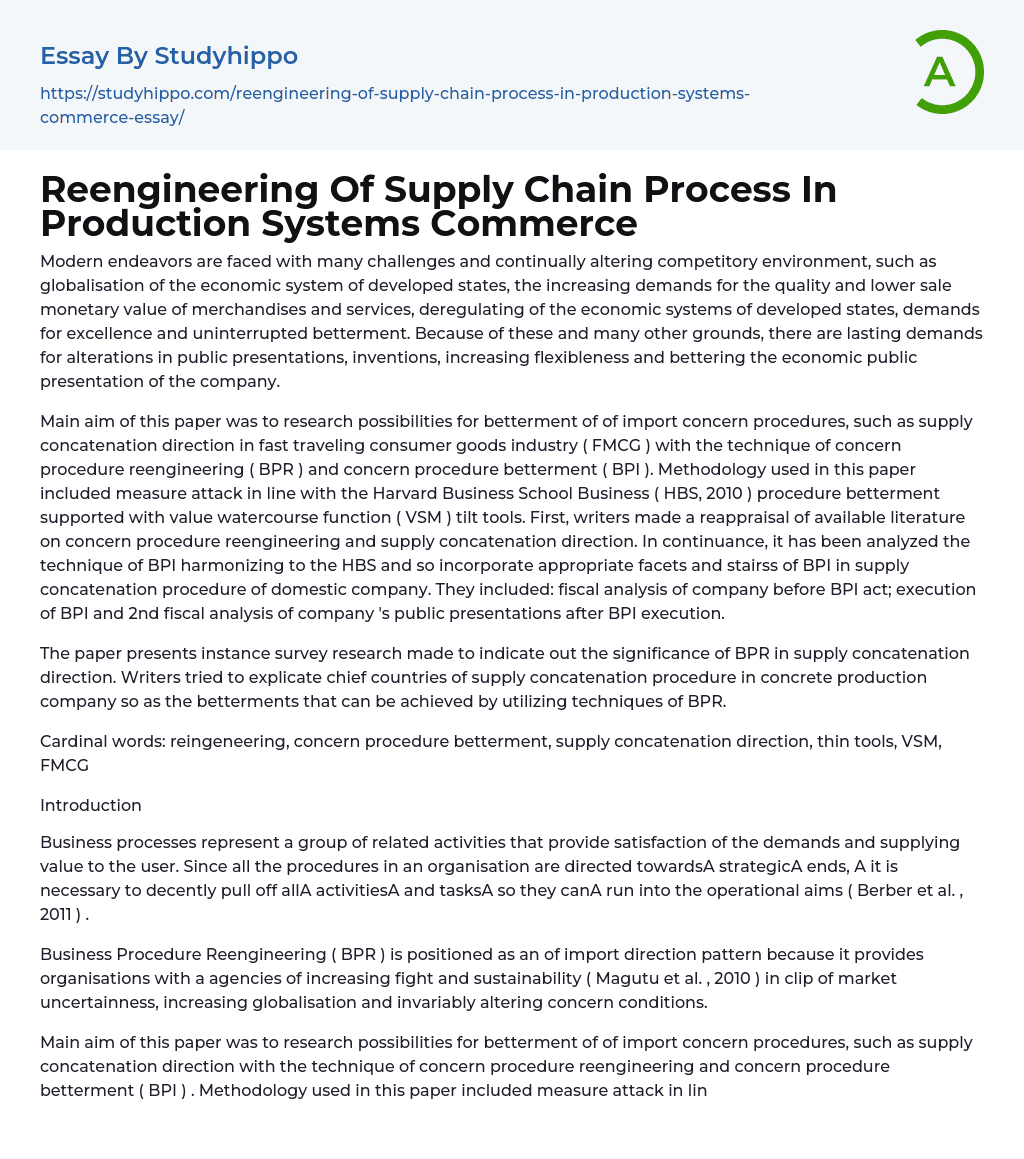
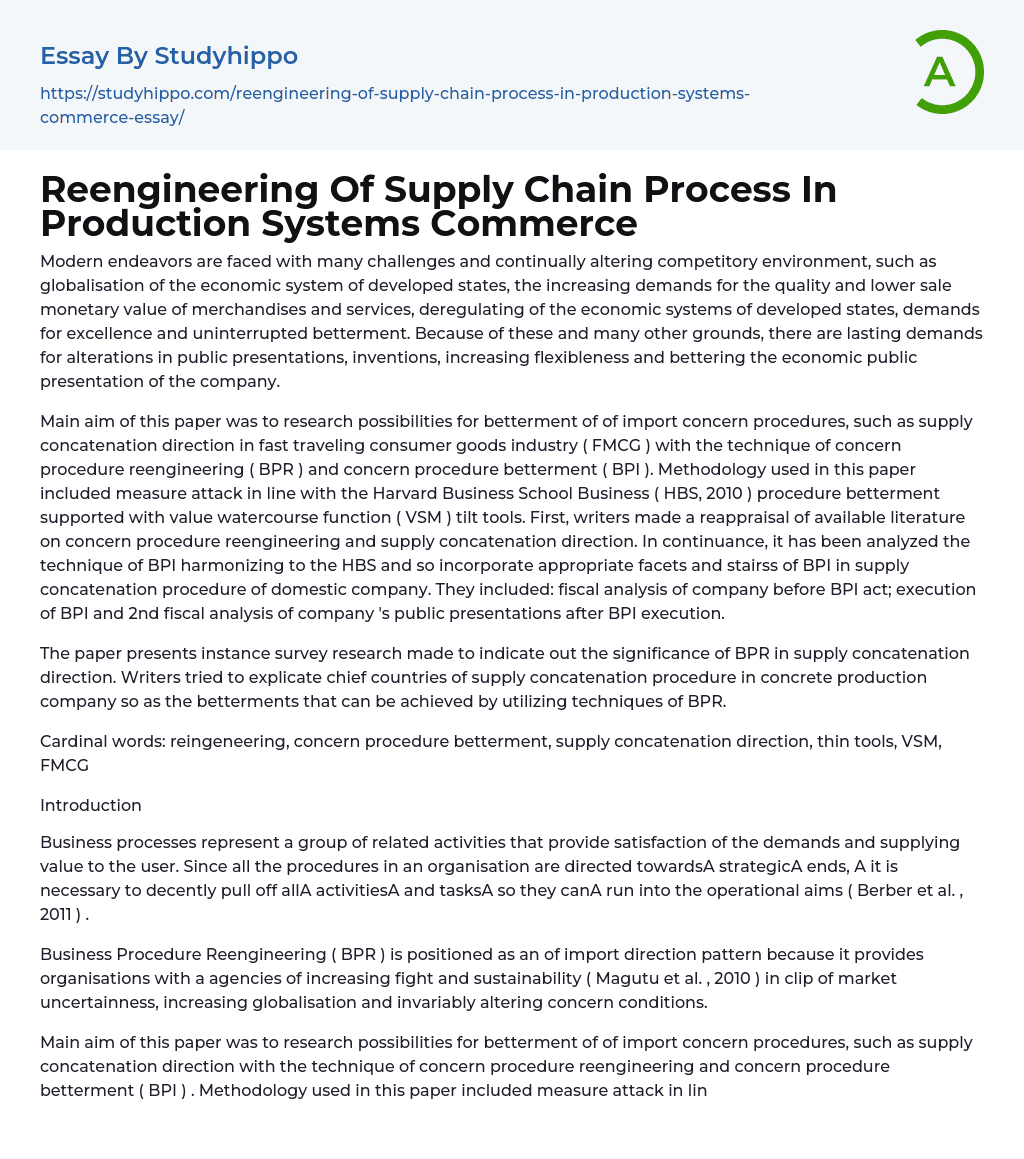
Reengineering Of Supply Chain Process In Production Systems Commerce Essay Example
The modern world poses various challenges and a dynamic competitive environment. These challenges encompass globalization of developed economies, escalating demands for affordable and high-quality products and services, deregulation of developed economies, and the necessity for excellence and continuous improvement. As a result, companies must adapt their performance, innovations, flexibility, and overall economic performance to address these factors. This paper concentrates on investigating ways to enhance crucial business processes in the fast-moving consumer goods industry (FMCG), specifically supply chain management. It explores the utilization of business process reengineering (BPR) and business process improvement (BPI) techniques.
The research in this paper utilized the procedure betterment framework from Harvard Business School Business (HBS, 2010) and value stream mapping (VSM) tilt tools to measure attack. The authors first reviewed existing literature on business process reengineering and supply chain man
...agement. They then analyzed the technique of business process improvement (BPI) based on the HBS method and integrated relevant aspects and steps of BPI into a domestic company's supply chain process. These steps included conducting a financial analysis before implementing BPI, implementing BPI, and conducting a second financial analysis to evaluate the company's performance post-BPI implementation.
The purpose of this paper is to demonstrate the significance of Business Process Reengineering (BPR) in supply chain management. The authors conducted a case study research focusing on a concrete production company to illustrate key areas of the supply chain process and how BPR techniques can lead to improvements. The keywords for this study include reengineering, business process improvement, supply chain management, lean tools, VSM, FMCG.
Introduction
Organizational processes are interconnected activities that fulfill user needs and add value. It is essential to effectively manage all tasks and activitie
aligned with strategic objectives to achieve operational goals (Berber et al., 2011).
Business Procedure Reengineering (BPR) is considered to be a significant management practice as it offers organizations a way to enhance their competitiveness and sustainability (Magutu et al., 2010) during times of market uncertainty, increasing globalization, and constantly changing business conditions. The main objective of this paper was to examine opportunities for improving important business processes, including supply chain management, using the methods of BPR and Business Process Improvement (BPI). The methodology employed in this study utilized a quantitative approach in accordance with the HBS Business Process Improvement framework.
Initially, the authors conducted a literature review on business process reengineering and supply chain management. Next, they examined the method of business process improvement (BPI). Following the theoretical analysis, the authors incorporated relevant BPI steps into the domestic company's supply chain process. These steps consisted of assessing the company's financial situation prior to implementing BPI, carrying out the BPI implementation, and conducting a second financial analysis to evaluate the company's performance post-BPI. Additionally, non-financial performances were also discussed.
The paper presents a survey research that aims to demonstrate the importance of Business Process Reengineering (BPR) in Supply Chain Management (SCM). The authors seek to explain the key areas of the supply chain process in a concrete production company and the improvements that can be achieved through the use of BPR techniques.
A Theoretical Review
Business Process Reengineering
Definitions of business processes are numerous, with most of them originating from the BPR theory of the 1990s. According to
Hammer ; Champy (1993), a business process is a collection of activities that takes one or more types of input and produces an output that is valuable to the customer.
A concern procedure is a structured, mensural set of activities that is influenced by external events or other procedures (Davenport, 1993). According to Davenport, a concern procedure focuses on how work is done within an organisation, compared to the emphasis on what in a merchandise focal point. Essentially, a procedure involves the coordination of work activities over time and space, with a defined start and end point, and identifiable inputs and outputs. It serves as a framework for taking action.
According to Rummler, Brache (1995), a business process is a series of steps designed to produce a product or service. Most processes are cross-functional and have "white space" between the organization's cubes on the chart. Some processes result in products or services required by external clients, known as primary processes. Other processes produce products that are not visible to the client but are necessary for efficient business operations, known as support processes. These processes are effectively managed using the BPM model, which serves as an integrated management philosophy and set of practices. The BPM model focuses on incremental and radical changes in business processes, continuous improvement, customer satisfaction, and employee engagement (Hung, 2006). The foundation of BPM is the reengineering of business processes, which involves rethinking and radically redesigning processes to achieve significant improvements in cost, quality, service, and speed (Hammer & Champy, 1993).
The writers view re-engineering as a completely new concept that involves radical redesign of business processes rather than incremental changes and improvements. Reengineering aims
to improve key areas of business and transform performances such as quality, cost, and speed (Altinkemer et al., 2011). Reengineering is the radical redesign of technological processes with the goal of enhancing economic efficiency. Radical redesign involves starting from scratch instead of altering or modifying existing methods (A A‡ekiA‡ et al., 2011).
The text discusses the common subjects to consider in successful reengineering examples. These include focusing on the entire process, recognizing the need for significant improvements, discarding unnecessary traditions, and utilizing information technology. It emphasizes that reengineering is a process rather than an organization, and companies redesign business processes within departments rather than specific departments themselves.
Reengineering should not be confused with automation, reducing inactive parts of the organization, reducing scope, reorganization, or making marginal changes.
There are four perspectives on reengineering: operational, dynamically-evolving, organizational, and systemic. The operational perspective prioritizes value-added activities and focuses on business process management.
The concept of dynamic-evolutionary position focuses on implementing extremist reengineering activities in order to continuously improve business processes. Organizational position emphasizes that re-engineering should be supported by all employees with a highly advanced vision. From a system perspective, re-engineering aims to create an equal business environment that prioritizes the needs of customers and their demands (Dassisti, 2010). According to this concept, each part of the organization is a unique process that, when successfully executed, leads to higher levels of satisfaction and fulfillment. There are various ways to improve organizational processes (see Berber et al., 2012), but this paper specifically examines the supply chain management process as a significant component of overall business process improvement.
Supply Chain Management
Definitions of Supply Chain Management are numerous. SCM can be understood as "a systems
approach to viewing the supply chain as a whole, and to managing the overall flow of goods inventory from the supplier to the ultimate customer; a strategic orientation toward cooperative efforts to synchronize and integrate intrafirm and interfirm operational and strategic capabilities into a unified whole; and a customer focus to create unique and personalized sources of customer value, leading to customer satisfaction" (Mentzer et al., 2001). Supply chain management is "an integrative philosophy to manage the entire flow of a distribution channel from supplier to the ultimate user" (Cooper & Ellram, 1993).
Supply Chain Management is the planning and control of all procedures that connect partners in a supply chain with the intent of serving the needs of end users (Harrison & Van Hoek, 2005). It includes two or more firms in a supply chain entering into a long-term agreement; the development of trust and commitment to the relationship; the integration of logistics activities involving the sharing of demand and sales data; the potential for a shift in the venue of control of the logistics process (La Londe & Masters, 1994). A comprehensive definition was offered by writer Acimovic, who argues that "supply chain management includes all activities related to procurement of resources, the transformation of these resources, as well as all logistics activities that involve coordination and cooperation of partners in the supply chain, which can be suppliers, intermediaries, logistics providers and customers. In the end, supply chain management integrates and coordinates supply and demand within a firm and between all members of the supply channel; the doctrine of the concept of supply chain management is that it is based on the responsibility that
each business function has, as a major determinant of business functions within the company and between companies, in a cohesive and high-performance business model."Supply chain management involves all operational logistics activities, production, and establishes organizing links through selling, gross revenues, merchandise design, and IT support ( AA‡imoviA‡ , 2006 ).
According to Stock & Lambert (2001), the process of supply chain management consists of several key components. These include the structure of the supply chain, which defines the relationship between the members of the supply system. Additionally, it encompasses the business processes within the supply system, as well as activities that should generate value for the customer who is at the end of the chain. Lastly, the managerial components focus on methodological techniques that integrate processes and networks within the supply chain.
In accordance with the aforementioned definitions, it is important to mention that the central concept of the supply chain is focused on ensuring that it is controlled in order to be fast, reliable, cost-efficient, and flexible enough to meet the needs of their customers (Janvier-James, 2012). The aim of management is to eliminate all forms of "waste" produced by individual entities in the supply chain, including logistics, inventory, procurement, product development, finance, and others. This is done by reducing costs and optimizing processes within the organization, while also applying the same management paradigm and technology outside the internal supply chain (Rejman PetroviA‡ et al., 2012).
From Figure 1, it is evident that Supply Chain Management (SCM) involves complex relationships between companies and providers, as well as the company and clients. Other writers have proposed a business process design model that integrates intelligence. They argue that intelligence
allows humans and human-designed systems to cope with environmental volatility, and they believe that applying these principles to organizational processes can increase the success rate of business operations in an intelligent supply chain (Siurdyban & Moller, 2012).
Methodology
When analyzing the methodology of process reengineering, it is important to consider the ideas put forth by foreign researchers. Zellner (2011) attempted to provide a structured overview of how to improve business processes (BPI) and their contribution to enhancing current practices. Despite much discussion about BPI, there is still a lack of support for its implementation in improving processes.
Most approaches focus on what needs to be done before and after improvement, but the process of improvement itself remains unclear. The authors have analyzed and evaluated numerous entries on business process reengineering (BPR) in their works (see Zellner, 2011; Reijers et al., 2005). There are different opinions on how to implement the reengineering of an organization when determining the stages or steps in the process. Based on a review of the literature, it can be concluded that a gradual, phased approach is always discussed, starting from the determination process for the reengineering implementation to the continuous improvement of the new process.
The framers of reengineering methodological analysis are assumed to be Hammer and Champy ( 1993 ), with numerous other approaches being used today ( Hammer & Champy, 1993 ; Guha et al. , 1993 ; Kettinger et al. , 1997 ; MiladinoviA‡ & AdamoviA‡ , 2010 ; HBS, 2010 ). This paper presents the application of Harvard Business School's ( HBS ) methodological analysis for re-engineering in the procurement process of the food industry. The steps involved in the analysis
are as follows:
- Analysis of financial indicators before BPI (business process improvement);
- Implementation of BPI;
- Financial analysis of company's performances after BPI implementation;
- Discussion on non-financial performances.
A study on the improvement process of supply chain management is conducted in a company in the food industry that produces fast moving consumer goods ( FMCG ). The company, mentioned as SFC in this study, was founded in 1995 in the northern part of Serbia and operates with approximately 1300 employees in a HACCP and ISO certified factory.
In August 2008, the company joined a large transnational company in the non-alcoholic drinks and nutrient industry. According to official financial data, the company was profitable. To gain further insight into the company's financial position and business success, efficiency indicators are calculated. It is important to note that even though the observed company was profitable, it recognized the need for improvements, integration, and standardization of processes (KuA?ar et al., 2009) to determine its position and promote itself in the competitive market. Therefore, an analysis of the business processes has been conducted to identify areas where changes can be made to enhance important business indicators.
After reexamining the concern processes, the company identified the supply concatenation procedure as one of the cardinal procedures that significantly affect the overall concern. According to Harvard Business School (HBS, 2010), the methodology for Business Process Improvement (BPI) consists of six interconnected stages: planning, analysis, redesign, obtaining resources, execution, and continuous procedure improvement. To improve business procedures, the initial
step is planning. This involves selecting an existing procedure to improve, defining the scope of the improvement project, and selecting a team to implement reengineering. The next step in the BPI process is analyzing existing procedures within the organization. This includes understanding the role of the procedure, identifying problems, gathering information from stakeholders, and benchmarking against other organizations' solutions. After analyzing the existing procedure, it is necessary to redesign it. This is done through steps such as anticipating a better process and testing improvement ideas from the team.The text below discusses the steps involved in considering the deductions of the potential design of a procedure, obtaining feedback from stakeholders, and streamlining the redesigned procedures, while also preserving the and their contents.
When redefining a procedure, it is essential to carry out the 4th step: obtaining resources, which is often linked to human resources (HR), information technology (IT), and financial resources. The important aspect during the change process is that the new procedure frequently necessitates a change in the resources utilized. Changes in power, performance, workload, responsibilities, and even the number of employees are among the most common alterations associated with human resources. Additionally, the introduction of new technology is almost always a part of reengineering, particularly in the domestic business environment.
The implementation of IT in various work processes is a necessity. When properly implemented, it can reduce manual labor costs, speed up information flow, and improve the accuracy of information. The fifth phase of BPI involves implementing a new procedure within the organization, which is the most challenging step in process improvement. What is crucial in this phase is identifying any potential barriers to implementation
and streamlining the work process.
Here, the key figures are the top director, company leader, and procedure proprietors who must remain dedicated to the idea of a new and improved procedure, regardless of how complex or impossible it may seem to others. If the redesigned procedure is accepted during implementation, we can proceed to the next step, which involves continuous improvement. Specifically, the new procedure must consistently deliver the expected results. This involves assessing the performance of business processes (such as quality, turnaround time, customer satisfaction, cost, etc.), identifying potential issues, and updating performance measures and targets as necessary.
Business Procedure Improvement in the Company
Analysis of bing procedure included function of procedure, placing jobs, questioning stakeholders in order to set up facts and valid information about the procedure, and benchmarking in footings of detecting how other organisations solved determined or similar jobs. Map of procedure occurs as a consequence of the function procedure (Van Ackere et al., 1993). It is a graphical representation of the procedure with the show order of undertakings utilizing different versions of the description of the procedure eg DTP-flow diagrams, AS2, IDEF, etc. (Giaglis, 2001). Writers have applied in this instance Sigma Flow VSM - tilt and six sigma tools for mapping procedure (see BoA?iA?koviA‡ et al.)
, 2012 ; PavletiA‡ et al., 2007 ; SokoviA‡ et al., 2005 ). Maping "represents one of the get downing foundations in information assemblage and system analysis that, following to the vision of the top direction and staff preparation, represents the foundation for successful reengineering procedure" (RadoA?eviA‡ et al.
According to the complexity of the function with VSM-thin methodology, a simplified representation of the process given endeavor is
provided. Sales' planning, a sub process of SCM, circulates information about the sales program for a period of time. Based on the annual budget, directors in the sales and marketing department plan to create annual, semi-annual, quarterly, and monthly sales programs.
This paragraph provides an overview of the initial information related to the gross revenues program and production program. The production program includes planning for capacities, both in terms of manpower and machinery, in order to execute the programs outlined in the sub procedure for gross revenues planning. The production program takes into account various constraints, such as maximum production per month, weekly breakdown of machines, machine speed, and others. Production planners create their plans based on the gross revenues program, which include weekly and daily production schedules as well as work capacity. This level of planning is referred to as operational planning. Within this sub procedure, information is generated regarding the quantity of products to be produced in each group within the product mix.
The merchandise is sent to the main warehouse, which is managed by a team of people responsible for planning supply shops. In addition, the production plan is shared with suppliers to inform them of the required purchases of raw materials. The company has two options: directly contacting suppliers based on delivery measures and rates, or planning resource allocation based on the sales program (MRP and MRPII) and transferring it to the procurement sector. In this case, a provider will be selected to work with, considering the number of secondary priority providers and determining the trade price, transportation, and ordered volume based on product features and quantity discounts, among other factors.The company's display
on the basis of documents and interviews with the SCM director reveals that the third bombing procedure is the company's supply program for distribution centers. The purpose of this sub procedure is to create favorable conditions for the efficient and uninterrupted transfer of products to distribution centers, ensuring they are delivered when and where they are needed.
The need for distribution as an economic activity is caused by discrepancies between production and consumption in terms of place, time, quantity, and product variety. This is stated by Pranulis et al. (2008). The distribution center's sector manager is responsible for overseeing the daily transportation of finished products based on the production plan and information provided by planners regarding delivery to customers. Park et al. discuss these aspects in their paper.
, 2007 ) suggest an algorithm that uses conveyance agents. This algorithm involves several entities - the agents that gather and share information. These agents are categorized based on their role in distribution, manufacturing, and procurement. The multiagent system also includes a possible integrated SCM planning agent used for coordinating production and distribution planning. Personalizing products to meet individual needs involves efficient and prompt supply of various goods and services at a reasonable price ( GligoriA‡ et al. , 2011 ).
The frequent mismatch between market information and sales programs is revealed here as an exacerbating circumstance for the production, inventory, and delivery plans. Upon analyzing the current procedures in the Supply Chain Management (SCM), it was found that there are certain issues stemming from a lack of awareness about certain activities in the process. To address this, a redesign of the process was carried out, including the creation of
the following elements: an introduction (derived from the sales planning process) and a new process focused on demand planning. Additionally, it was decided to hire at least two workers, one for the Serbian market (which constitutes approximately 70% of the company's total market) and one for the export markets.
Closely linking the demand program with the sale programs allows for accurate and precise information on the market's merchandise needs. This leads to better utilization of capacity, reduced stock levels, balanced supply and sales, and ultimately increased customer and consumer satisfaction. Additionally, there will be a reduction in the amount of lost products due to non-compliance with sales, production, and delivery. Improved relationships with both clients and suppliers are also expected. Integrating the company's largest buyers into the information system can enhance sales efficiency by enabling them to send requests for replenishment of only those products that are truly depleted. Distribution centers would then automatically respond to these requests by contacting delivery planners, who will in turn inform supply planners about the specific products, quantities, and timing needed. The integration of suppliers into the SCM information system is also crucial.
The information about resources consumed in a timely manner is accessible to providers who have their own capacity and exercise delivery to the company when materials are actually needed. Two-way communication ensures that the company not only receives requests for materials, but also receives information and inquiries from the seller regarding the availability of materials and whether more or less is needed. This is crucial since certain materials are not produced locally and need to be sourced from Latin American countries, which takes several weeks for acquisition
and several days for transportation. Source: Suggestions from authors for new process. Figure 3 demonstrates the altered relationship between the company and providers, company and clients, and the development of a strategic cooperative and collaborative approach.
The text discusses the importance of separating demand planning from the gross revenues program in order to create accurate production programs. The demand and supply program, which includes trade selling activities and new merchandise development and launch, forms the basis for the production program. This allows for specific demands for the merchandise to be determined on a monthly, fortnightly or even hebdomadal program, improving efficiency in terms of capacity use. Additionally, ERP software integrates internal procedures such as gross revenues, production, and stuff handling, creating a large circle on the map that includes suppliers, clients, and the company. This integration supports various tools that combine information on all participants in the chain. By accessing information about suppliers' production and delivery schedules in real-time, buyers can plan their own inventory levels and production programs. Sharing information about the current state of orders among chain members enhances service quality, speeds up payment cycles, and improves productivity (Kelle & Akbulut, 2005).
The velocity of bringing, guaranteed supply and a possibility to purchase merchandises, convenience for purchasers and other things may better the relationship between purchasers and Sellerss and heighten consumer satisfaction ( Banyte et al. , 2011 ).
Discussion
After executing the SCM procedure betterment it is necessary to indicate out all the qualitative and quantitative alterations that have been implemented. Specifically, in the paper has already been mentioned that that there are several positive effects of alterations in concern procedures. For illustration, in this specific
instance survey, these effects are summarized and presented in table 2. By and large, a decrease in stock list costs in footings of the stock list in figure of yearss, but besides the cost of storage infinite.
The issue of stock list direction is a crucial area where a business can gain a competitive advantage. When it comes to stocks, it is important to note that the company faced challenges in managing inventory levels. These challenges were primarily caused by inaccurate information on market demands, excessive amounts of liquid assets, high costs of storage space, and unnecessary inventory. However, the implementation of a new process known as Supply Chain Management (SCM) has helped reduce inventory holding costs and release the company's liquid assets. Special attention should be given to the sourcing of raw materials, which are obtained from companies based in Latin American countries.
The reduction of stock list and transit costs is a crucial aspect in reengineering, as it is aimed at achieving the mission and goals of cost reduction. Another improvement brought about by reengineering is the decrease in time and changes in production lines, resulting from better planning. The production planning process used to be hindered by inaccurate market demand information, leading to frequent adjustments in production line setups. However, thanks to more realistic market demand information, the preparation of production lines and workforce is now based on a more effective plan.
Due to this, there has been a decrease observed in the number of capacity accommodations and time allocated for the preparation of produ
- Chief Executive Officer essays
- Convenience Store essays
- Firm essays
- Training And Development essays
- Unilever essays
- Variable Cost essays
- Virgin Group essays
- Bargaining essays
- Entity essays
- Pest analysis essays
- Â John Locke essays
- 9/11 essays
- A Good Teacher essays
- A Healthy Diet essays
- A Modest Proposal essays
- A&P essays
- Academic Achievement essays
- Achievement essays
- Achieving goals essays
- Admission essays
- Advantages And Disadvantages Of Internet essays
- Alcoholic drinks essays
- Ammonia essays
- Analytical essays
- Ancient Olympic Games essays
- APA essays
- Arabian Peninsula essays
- Argument essays
- Argumentative essays
- Art essays
- Atlantic Ocean essays
- Auto-ethnography essays
- Autobiography essays
- Ballad essays
- Batman essays
- Binge Eating essays
- Black Power Movement essays
- Blogger essays
- Body Mass Index essays
- Book I Want a Wife essays
- Boycott essays
- Breastfeeding essays
- Bulimia Nervosa essays
- Business essays
- Business Process essays
- Canterbury essays
- Carbonate essays
- Catalina de Erauso essays
- Cause and Effect essays
- Cesar Chavez essays