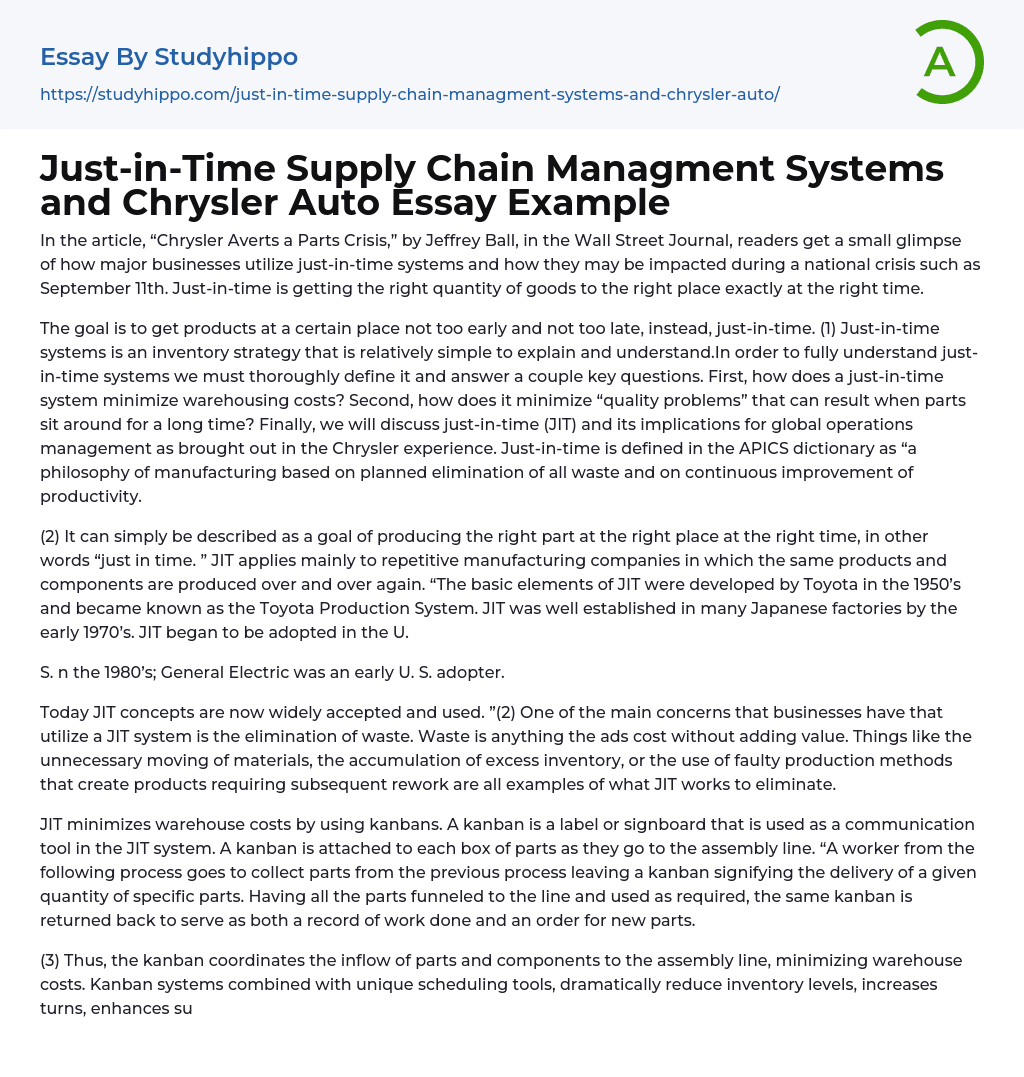
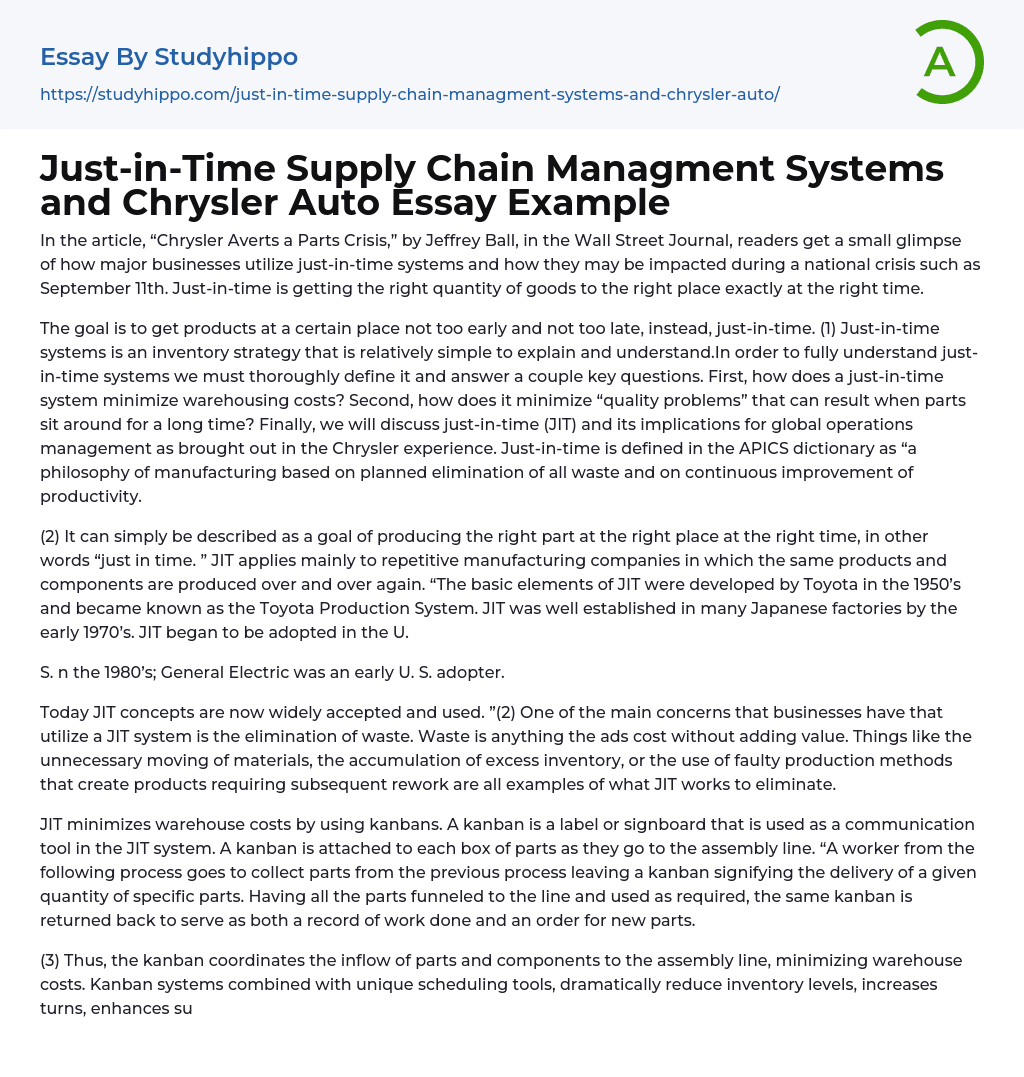
Just-in-Time Supply Chain Managment Systems and Chrysler Auto Essay Example
Jeffrey Ball's Wall Street Journal article "Chrysler Averts a Parts Crisis" offers insight into how large businesses utilize just-in-time systems and their vulnerability during national crises such as September 11th. The just-in-time system involves delivering the appropriate quantity of goods to the correct location precisely on time.
The aim is to obtain products at a specific location at the optimal time, known as just-in-time. (1) Just-in-time systems refer to an inventory strategy that is relatively easy to comprehend. To gain a full comprehension of just-in-time systems, we must first provide a comprehensive definition and address various essential inquiries. First, how does a just-in-time system reduce warehousing expenses? Second, how does it minimize "quality issues" that may arise when parts are left unused for an extended period of time? Ultimately, we will explore just-in-time (JIT) and its effects on glo
...bal operations management, as seen in the Chrysler case. According to the APICS dictionary, just-in-time is characterized as "a manufacturing philosophy that prioritizes minimizing waste and continually improving efficiency."
(2) "Just in time" or JIT is a manufacturing goal that aims to produce the correct components or products at the appropriate location and time. JIT is typically utilized by repetitive manufacturing companies that frequently produce the same goods and parts. The Toyota Production System developed the fundamental elements of JIT in the 1950s, and it was extensively employed in Japanese factories by the early 1970s. Furthermore, JIT started to spread to the U.S.
General Electric was among the first companies in the United States to adopt S. n technology in the 1980s.
The use of JIT concepts is now widespread and popular, and businesses employing such systems are mainly concerned with
eliminating waste. Waste refers to any cost without adding value, such as unnecessary material movement, excessive inventory accumulation, or faulty production methods requiring rework. JIT's goal is to eliminate these types of waste.
Using kanbans in the JIT system effectively reduces warehouse costs. A kanban acts as a communication tool and is attached to every box of parts sent to the assembly line. When a worker needs parts from the previous process, they retrieve them and leave behind a kanban indicating the quantity of specific parts delivered. This ensures that all parts are used as needed and directed to the line. The same kanban is then returned, serving as a record of work done and an order for new parts.
(3) The kanban system works by coordinating the inflow of parts and components to the assembly line, which in turn helps to minimize warehouse costs. By combining kanban systems with unique scheduling tools, inventory levels can be dramatically reduced, turns can be increased, supplier/customer relationships can be enhanced, and the accuracy of manufacturing schedules can be improved. JIT also helps to minimize warehousing costs by producing small amounts of items every day. This strategy, referred to as producing small lots, can be achieved through uniform plant loading in which all items requiring production are produced in one day in small batches or lots. Contrastingly, in a traditional production plan, a company might produce one product on one day and then produce a different product on the next day.
The presence of adaptable resources and a streamlined facility layout are crucial elements for implementing a JIT system. These factors can also contribute to decreased warehousing expenses. A company
that possesses versatile equipment and cross-trained workers capable of performing multiple tasks can enhance production speed and efficiency. Additionally, an efficient facility layout, where workstations are in close proximity, minimizes unnecessary transport and movement, promoting smoother material flow. The JIT approach helps to prevent quality issues that may arise from prolonged storage of parts.
The philosophy of JIT emphasizes waste reduction and continuous improvement. A company that adopts JIT believes in the approach of constantly refining their processes rather than settling for mediocrity. JIT achieves better quality control by implementing pull systems, quick setups, and smaller productions runs, while also utilizing versatile resources and effective facility designs.
An effective way to prevent parts from going bad and save costs is to avoid having them lying around unused. Just-in-time (JIT) systems rely on transportation networks, including trucks, boats, and planes, to deliver time-sensitive parts to factories employing JIT. A case study titled "Chrysler Averts a Parts Crisis" revealed how vulnerable a JIT operation can be to transportation disruptions. During the aftermath of the September 11th attacks, airplanes were grounded and trucks faced significant delays at U.S. ports, causing difficulties for JIT operations.
The September 11th attacks caused disruptions to border crossings, which had a negative impact on just-in-time systems used by auto plants and assembly lines. These systems rely on small, frequent deliveries of parts to minimize warehousing costs and quality problems. However, the disruptions caused delays in the transportation of necessary parts, resulting in shutdowns at auto plants like Chrysler and Ford. Despite the setbacks, the use of just-in-time systems remains an effective way to eliminate waste and improve business operations.
Just-in-time (JIT) employs several strategies to eliminate
waste, including the implementation of pull and production programs, kanbans, quick setups, small lots or batches, uniform plant loading, flexible resources, and efficient facility layouts. These measures can help reduce warehousing costs and quality issues. For effective production, it is crucial that production facilities receive multiple small deliveries of required materials throughout the day. However, if a national security issue like September 11th occurs again, companies may have to rely on backup plans as Chrysler did. Reference: Reid and Sanders, “Just-In-Time Systems”, Operations Management, Chapter 7, 2002.
The Industrial Engineering article by Richard Schonberger titled "Just-In-Time Production Systems: Replacing Complexity with Simplicity in Manufacturing Management" from October 1984, pages 52-63, and the Business e-Coach website's "Just-in-Time (JIT) Production" section, found at http://www.1000ventures.com/business_guide/im_jit_main, are both related to JIT production.
The Wall Street Journal reported that Jeffrey Ball's article "Chrysler Averts a Parts Crisis" discusses how Chrysler avoided a potential crisis with its parts supply. The article was published in New York on September 24, 2001 and can be found on page B1.
- Chief Executive Officer essays
- Convenience Store essays
- Firm essays
- Training And Development essays
- Unilever essays
- Variable Cost essays
- Virgin Group essays
- Bargaining essays
- Entity essays
- Pest analysis essays
- John Locke essays
- 9/11 essays
- A Good Teacher essays
- A Healthy Diet essays
- A Modest Proposal essays
- A&P essays
- Academic Achievement essays
- Achievement essays
- Achieving goals essays
- Admission essays
- Advantages And Disadvantages Of Internet essays
- Alcoholic drinks essays
- Ammonia essays
- Analytical essays
- Ancient Olympic Games essays
- APA essays
- Arabian Peninsula essays
- Argument essays
- Argumentative essays
- Art essays
- Atlantic Ocean essays
- Auto-ethnography essays
- Autobiography essays
- Ballad essays
- Batman essays
- Binge Eating essays
- Black Power Movement essays
- Blogger essays
- Body Mass Index essays
- Book I Want a Wife essays
- Boycott essays
- Breastfeeding essays
- Bulimia Nervosa essays
- Business essays
- Business Process essays
- Canterbury essays
- Carbonate essays
- Catalina de Erauso essays
- Cause and Effect essays
- Cesar Chavez essays