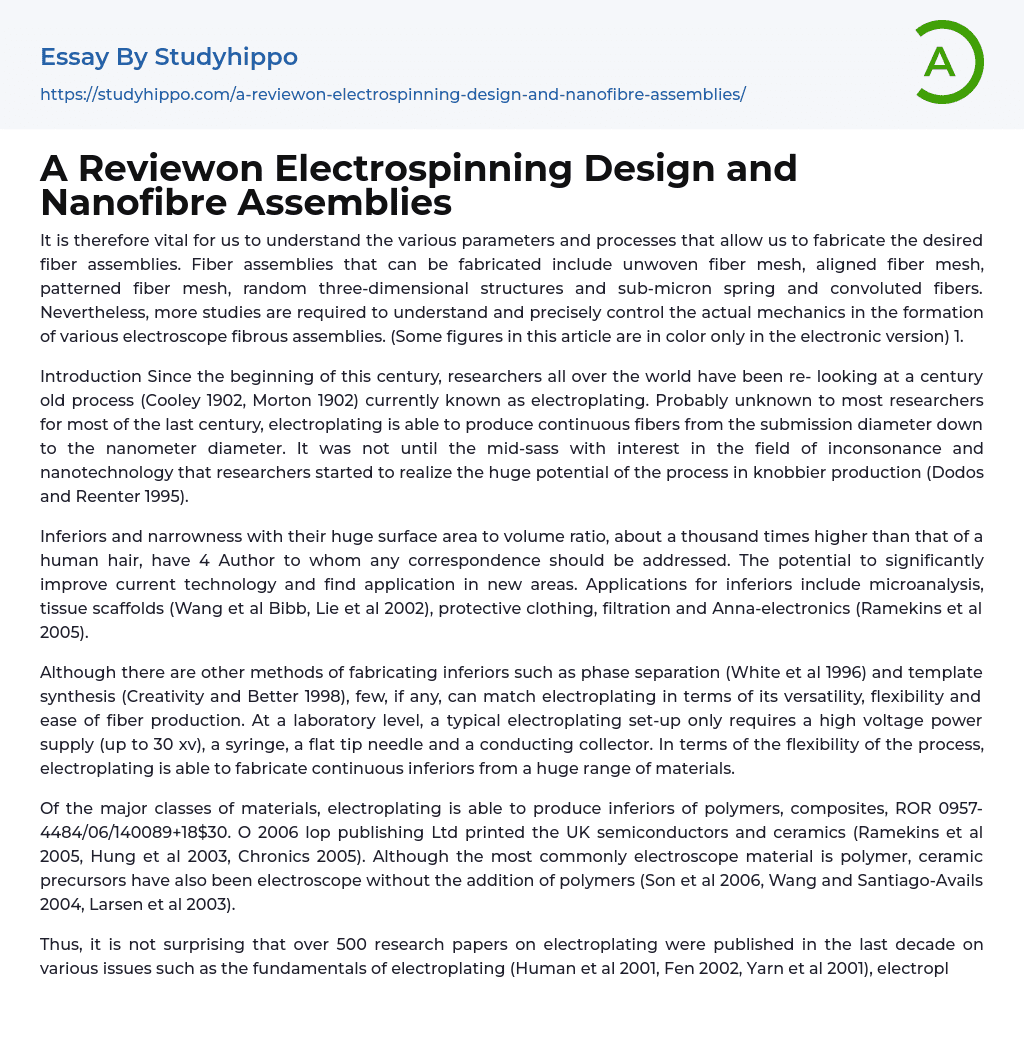
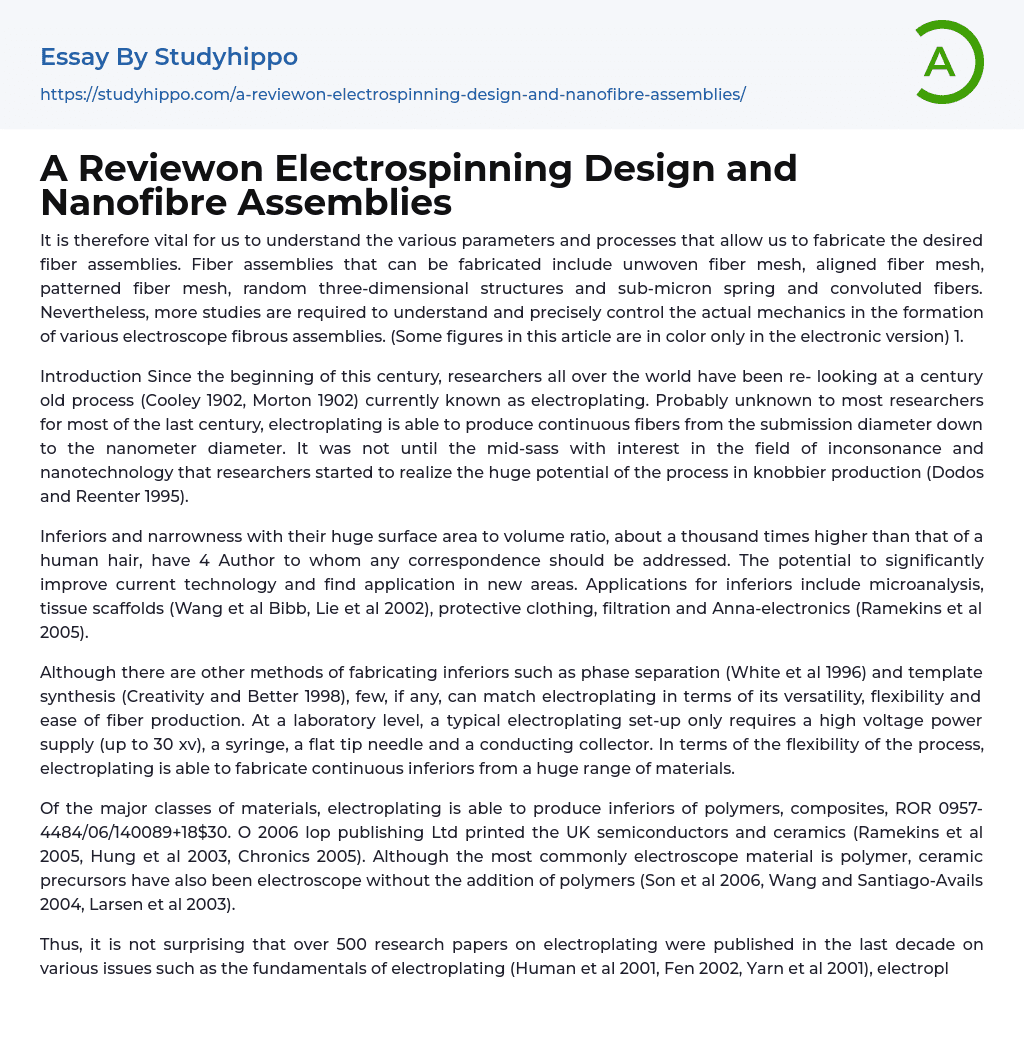
A Reviewon Electrospinning Design and Nanofibre Assemblies Essay Example
In order to fabricate desired fiber assemblies, it is important for us to understand the different parameters and processes involved. These assemblies can include unwoven fiber mesh, aligned fiber mesh, patterned fiber mesh, random three-dimensional structures, sub-micron spring, and convoluted fibers. However, further research is needed to fully comprehend and control the mechanics behind the formation of these electroscope fibrous assemblies. It is worth noting that some figures in this article are only available in color in the electronic version.
Introduction: Researchers worldwide have been revisiting the electroplating process, which originated in the early 1900s (Cooley 1902, Morton 1902). This process can produce continuous fibers ranging from large to nanometer diameters. It was only in the mid-1990s, with the emergence of interest in inconsonance and nanotechnology, that researchers began to recognize the
...immense potential of electroplating in knobber production. Inferiors and narrowness, with their significantly higher surface area to volume ratio compared to a human hair by a thousand times, have the potential to revolutionize current technology and find applications in new areas.
Applications for inferiors, such as microanalysis, tissue scaffolds (Wang et al Bibb, Lie et al 2002), protective clothing, filtration, and Anna-electronics (Ramekins et al 2005), are diverse in nature. While other methods of fabricating inferiors exist, such as phase separation (White et al 1996) and template synthesis (Creativity and Better 1998), electroplating stands out for its versatility, flexibility, and ease of fiber production. In a laboratory setting, a typical electroplating set-up only requires a high voltage power supply (up to 30 xv), a syringe, a flat tip needle, and a conducting collector. Electroplating excels at fabricating continuous inferiors from a wide range
of materials. Electroplating is capable of producing inferiors from polymers, composites, semiconductors, ceramics (Ramekins et al 2005, Hung et al 2003, Chronics 2005). While polymers are the most commonly used electroscope material, ceramic precursors have also been employed without the addition of polymers (Son et al 2006, Wang and Santiago-Avails 2004, Larsen et al 2003).
Over the past decade, more than 500 research papers have been published on electroplating. These papers cover various topics such as the fundamentals of electroplating, electroplating conditions, and characterizing fiber for different applications. Some notable authors and studies include Human et al (2001), Fen (2002), Yarn et al (2001), Krishna et al (2003), Tan et al (2005), Digitize et al (2001 b), Mit-apathy et al (2004), Shawano and Sung (2002), Ideas et al (2004), and Rayon et al (2006). A comprehensive overview of these studies can be found in the book by Ramekins et al (2005).
Recent research on electroscope fibers has focused on exploring different materials, characterizing the fibers, and discovering new applications. The arrangement of fibers plays a crucial role in their performance, with ordered Anna-grooves and assemblies shown to affect cell proliferation and morphology (Xx et al 2004). To fully utilize the potential of electroscope fibers, it is necessary to fabricate diverse fibrous assemblies and ensure the growth or positioning of single fibers across specific electrodes.
In certain applications like filtration membranes, an unwoven mesh may be preferred. The development of yarn made of knobbier could lead to higher performance clothing or woven scaffolds.
The use of physical manipulation to form different assemblies is challenging due to the size of smaller objects. However, electroplating offers an advantage by
allowing the fabrication of various knobbed assemblies in place. This customization enhances the performance of the assemblies, giving electroplating an edge over other large-scale production methods. In this review, we will focus on different electroplating designs and modifications in order to create diverse knobbed assemblies. This information will benefit researchers in various fields, as they will become familiar with the range of knobbed assemblies that can be produced and the corresponding setups required. We will also describe the concepts researchers have used to generate these assemblies, facilitating an understanding of the process and enabling the creation of new designs to meet specific needs. Furthermore, the process of forming knobbed assemblies through electroplating relies on the stretching of a solution, and an understanding of electroplating principles and relevant parameters is crucial in appreciating and comprehending this process.
Electroplating, unlike dry-spinning and melt-spinning, utilizes electrostatic forces to stretch the solution as it solidifies. The drawing of the elution to form the fiber continues as long as enough solution is available for the electroplating Jet. Consequently, the formation of the fiber remains continuous without disrupting the electroplating Jet. In a typical electroplating set-up (Figure 1), a solution is fed through a spinneret. By applying a high voltage to the solution, specifically exceeding 5 xv, the repulsive force within the charged solution exceeds its surface tension, causing a Jet to erupt from the spinneret tip. While the Jet remains stable near the spinneret tip, it eventually undergoes a bending instability stage as the solvent evaporates, leading to further stretching under electrostatic forces in the solution. Various researchers (Yarn and Susann 2004, Kamala et al 2003) have also explored electroplating
devices without using spinnerets. Typically, a grounded target is utilized to collect the resulting fibers, which are deposited in an unwoven mesh form.
The text discusses the parameters that control the diameter of electrospun fibers. These parameters have been studied in various references (Ramekins et al 2005, Thereon et al 2004, Mit-apathy et al 2004, Sousaphone et al 2005, Tan et al 2005). Some commonly studied parameters include solution viscosity, conductivity, applied voltage, spinneret tip-to-collector distance, and humidity.
For instance, reducing the spinneret tip-to-collector distance can result in the collection of a mesh with interconnected fibers (Buck et al 1999), while decreasing the solution concentration will decrease the diameter of the electrospun fibers. Though polymer chain entanglement is important for fiber formation in polymers (Sheens et al 2005), solution viscosity is a more general parameter as ceramic precursors can also be electrospun despite their low molecular weight (Son et al 006, Wang and Santiago-Avails 2004).
There are generally two main methods for achieving different fiber assemblies. One method involves manipulating the electric field to control the flight of the electrospinning jet, while the other method involves using a dynamic collection device. However, using different static collection devices can also result in some form of fiber assemblies. Researchers have made various modifications to the electrospinning set-up to overcome limitations and enhance the performance of electroscope fibrous mesh.
[Topical Review Table 1]List of US patents issued before 1976. Patent issued date: 04 February 1902, 10 May 1938, 19 July 1938, 16 May 1939, 16 May 1939, 06 June 1939, 01 August 1939, 16 January 1940, 29 June 1943, 14 December 1943, 30 May 1944, and 18 October 1966. Inventor: J F
Cooley, W J Morton, K Hegira, A Formals, C L Norton, E K Cladding, F W Manning, and H L Simons. Patent number: 692,631, 705,691, and 1. However, Dalton et al used electroscope polymer melts to deposit fibers directly on cells to form layered tissue constructs for issue engineering. This eliminates any chance of introducing psychotic solvents into the cell culture when the fibers are deposited (Dalton et al 2006). While there have been patents filed for various electroplating set-ups since the sass, it is only in the last decade that academia has been looking into using electroplating to fabricate various nonferrous assemblies. Schematic diagrams of the various electroplating set-ups are shown in table 2. Various principles behind the fabrication of the nonferrous assemblies will be covered in the following sections. Dynamic mechanical device The ability to create ordered structures has many implications in the performance of a fiber assembly.According to Xx et al (2004), cells cultured on aligned knobbier scaffolds have been observed to proliferate in the same direction as the fiber orientation. Multiple studies (Matthews et al 2002, Kamala et al 2003, Submarine et al 2005) have shown that aligned fibers can be obtained by using a rotating collector. Table 2(A) shows a schematic diagram of the set-up. Matthews et al (2002) demonstrated that the speed of rotation of a mandrel affects the alignment of collagen fibers. At speeds below 500 RPM, a random mix of collagen fibers was collected. However, at a speed of 4500 RPM (approximately 1.4 m s-l at the surface of the mandrel), the collagen fibers showed significant alignment along the rotation axis. Mechanical testing revealed that the peak
stress along the principal fiber alignment was 1.5 Amp and the average modulus was 52.3 ± 5.2 Amp, while the peak stress across the principal fiber alignment was 0.7 1 Amp and the modulus was 26.1 ± 4.0 Amp (Matthews et al 2002). Kim et al (2004) studied the effect of linear velocity of the rotating mandrel on the crystalline, mechanical properties, and alignment of electroscope poly(ethylene ethereally) (PET). PET electroscope fibers were found to be more amorphous with increasing mandrel rotation, possibly due to rapid solidification and collection of the fibers.
The increased linear velocity of the mandrel resulted in greater alignment of the PET crystals in the fibers. The Young modulus, yield stress, and tensile stress of the mesh along the PET fiber alignment increased with higher mandrel rotation speed and fiber alignment. However, these properties tend to decrease when the linear velocity exceeds 30 m min-1. At a linear velocity of 45 m min-1, many fibers were dispersed into the air instead of being deposited on the mandrel (Kim et al., slower than the linear velocity of the rotating mandrel.
The reported average velocity of the electroplating Jet ranged from 2 m s-1 (Kowalski et al., 2005; Sunday et al., 2004) to 186 m s-1 (Smith et al., 2005). A separate study by Susann et al. using a rotating disc collector showed that at high enough rotation speed, necking of the electroscope fibers was observed (Susann et al., 2003). This observation may explain the reduced mechanical properties of the PET mesh collected at high speed ROR 3.
To understand the effect of electrostatics on liquid in the electroplating process, it is necessary
to trace back to its first inventor. The observation of water behavior under the influence of electrostatics was made as early as the sass (Gray, 1731-1732). In the late sass, electrodynamics was used to explain the excitation of dielectric liquid under an electric charge (Alarms, 1898).
The early sass saw the invention of electroplating for fiber production by Cooley and Morton (Cooley 1902, Morton 1902). They demonstrated a deep understanding of the process through their inventive designs. Cooley patented a setup that utilized auxiliary electrodes to guide the electroplating jet onto a rotating collector. In the sass, Formals introduced various innovative setups for creating electroscope fiber yarns, including designs that eliminated the need for a spinneret (Formals 1934). Many modern electroplating setups can be traced back to patents from over 50 years ago, involving multiple spinnerets and parallel electrodes for aligned fiber production (Formals AAA, Bibb, ICC, AAA, Bibb).
Table 1 lists the US patents filed prior to 1976. Fiber production levels are a crucial factor for the industry. Compared to the fast industrial fiber spinning process, electroplating is significantly slower. Industrial dry spinning achieves a yarn take-up rate of 200-1500 m min-l (Guppy and Katharine 1997), while electroplated yarn has a take-up speed of 30 m min-l (Kill et al 2005). Consequently, there was limited research and publications on electroplating before 1990 (Bandmaster 1971).
However, research has been conducted on the behavior of thin liquid Jets in an electric field by Selene in 1917 and Taylor in 1964, 1966, and 1969. The preferred method for producing fibers is melt spinning, with efforts being made to create electroscopic fibers using polymer melts by Larboard and Manley AAA
in 1981 b and ICC. However, there is currently less research in this area, likely due to the difficulty in fabricating nanometer diameter fibers. Table 2 provides a schematic diagram of various electroplating set-ups for multiple peppiness and to obtain various fibrous assemblies, assuming the spinneret is given a positive charge unless otherwise stated.
Assembly-aligned fibrous mesh A. A rotating drum is advantageous due to its simple set-up and ability to fabricate a large area of aligned fibers. However, fabricating highly aligned fibrous assemblies can be difficult and there is a risk of fiber breakage if the rotating speed is too high (Matthews et al 2002, Kim et al 2004).
B. Parallel electrodes provide a simple set-up and make it easy to obtain highly aligned fibers. These aligned fibers can also be easily transferred to another substrate. However, it is not possible to create a thicker layer of aligned fibers and there is a limit to the length of the aligned fibers (Lie et al 2003).
C. The advantage of a rotating wire drum collector is its simple set-up and ability to produce highly aligned fibers. However, it is not possible to create a thicker layer of aligned fibers and the fibers may not be aligned throughout the whole assembly (Kate et al 2004).
D. A drum collector with wire wound on it offers a simple set-up and the ability to produce highly aligned fibers. The area of aligned fibers on the wire can be adjusted by varying the wire thickness. However, the downside is that the aligned fibers are concentrated on the wire rather than being spread across the entire drum (Battier et al 2005).E. The rotating
tube collector with knife-edge electrodes allows for highly aligned fibers to be deposited on the tube. The entire tube is covered with aligned fibers and it is possible to achieve a thicker layer of aligned fiber deposition. However, this set-up requires a negative electrode and is only feasible for small diameter tubes.
F. The electroplating jet can be controlled using knife-edge electrodes on a spinneret. This allows for highly aligned fibers to be produced and the direction of fiber alignment on the tube can be controlled. Thicker layers of aligned fiber deposition are possible. However, a negative electrode is required and this method is only suitable for small diameter tubes.
G. The disc collector offers a simple set-up and allows for highly aligned fibers to be fabricated. It is possible to create arrayed fibers by attaching an irritable table on the edge of the disc. However, it is unable to maintain high fiber alignment at the same rotating speed when the deposited fibers are thicker. Additionally, the area of fiber alignment is limited.
H. An array of counter-electrodes provides a simple set-up. However, fiber patterning is not consistent throughout the assembly and the area of the assembly is limited. Thicker fibrous assemblies are not possible.
ROR Table 2. (Continued.) l.Advantage: A rotating drum with a sharp pin inside allows for the fabrication of a large area of arrayed fibers.
Disadvantage: The set-up for this method is complicated and it may not be possible to create a thicker area of arrayed fiber assembly. (Sunday et al. 2004)
Advantage: By placing a blade in line, the set-up for fabricating yarn is simple and the yarn can be easily removed from the collector.
The collected yarn is highly aligned.
Disadvantage: However, the fabricated yarn is of limited length and the deposited fibers have to be dipped in water first before the yarn is formed. (Too and Ramekins 2005)
Advantage: Using a ring collector placed in parallel, twisted yarn can be fabricated with a simple set-up.
Disadvantage: Similar to the previous method, the fabricated yarn is of limited length and one of the rings has to be rotated to twist the fibers that are deposited into yarn. (Dalton et al. 2005)
Advantage: Yarn collection using a water bath coagulation bath allows for a simple set-up and the fabrication of long continuous yarn that has well-aligned fibers.
Disadvantage: However, the yarn collection speed is relatively slow using this method. (Smith et al. 2005, Kill et al. 2005)
Additionally, mixing fibers of different materials of desired ratio may introduce interference between the electroplating jets. (Ding et al. 2004, Kodiak et al. 2005, Thereon et al. 2005, Maturity et al. 2003, Kit-n et al. 2006)
Finally, Figure 2 shows a small diameter electroscope nonferrous conduit as described by Kim et al.
The speed of rotation and orientation of fibers on the mandrel directly affect the material properties of the engineered matrix. The disorientation of fibers on the rotating mandrel may be due to residual charge accumulation, which hinders proper alignment of incoming fibers. To improve fiber alignment, the electroplating Jet's Hattie path can be reduced, along with minimizing residual charge accumulation on the mandrel. Seasick et al found that using an alternating-current (AC) high voltage supply instead of a direct-current (DC) supply for electroplating resulted in a greater degree of fiber alignment for collected polyethylene oxide (POE) on
the rotating mandrel. This suggests that using an AC potential has a dual function: it consists of short segments with alternating polarity, which greatly reduces the chaotic path of the electroplating Jet. As a result, fibers can be wound onto the rotating mandrel more easily and with better alignment. Additionally, since there are both positive and negative charges on the surface of the rotating mandrel, there is a neutralizing effect over the mesh area, minimizing charge accumulation.
- Organic Chemistry essays
- Acid essays
- Calcium essays
- Chemical Bond essays
- Chemical Reaction essays
- Chromatography essays
- Ethanol essays
- Hydrogen essays
- Periodic Table essays
- Titration essays
- Chemical reactions essays
- Osmosis essays
- Carbohydrate essays
- Carbon essays
- Ph essays
- Diffusion essays
- Copper essays
- Salt essays
- Concentration essays
- Sodium essays
- Distillation essays
- Amylase essays
- Magnesium essays
- Acid Rain essays
- Agriculture essays
- Albert einstein essays
- Animals essays
- Archaeology essays
- Bear essays
- Biology essays
- Birds essays
- Butterfly essays
- Cat essays
- Charles Darwin essays
- Chemistry essays
- Dinosaur essays
- Discovery essays
- Dolphin essays
- Elephant essays
- Eli Whitney essays
- Environmental Science essays
- Evolution essays
- Fish essays
- Genetics essays
- Horse essays
- Human Evolution essays
- Isaac Newton essays
- Journal essays
- Linguistics essays
- Lion essays