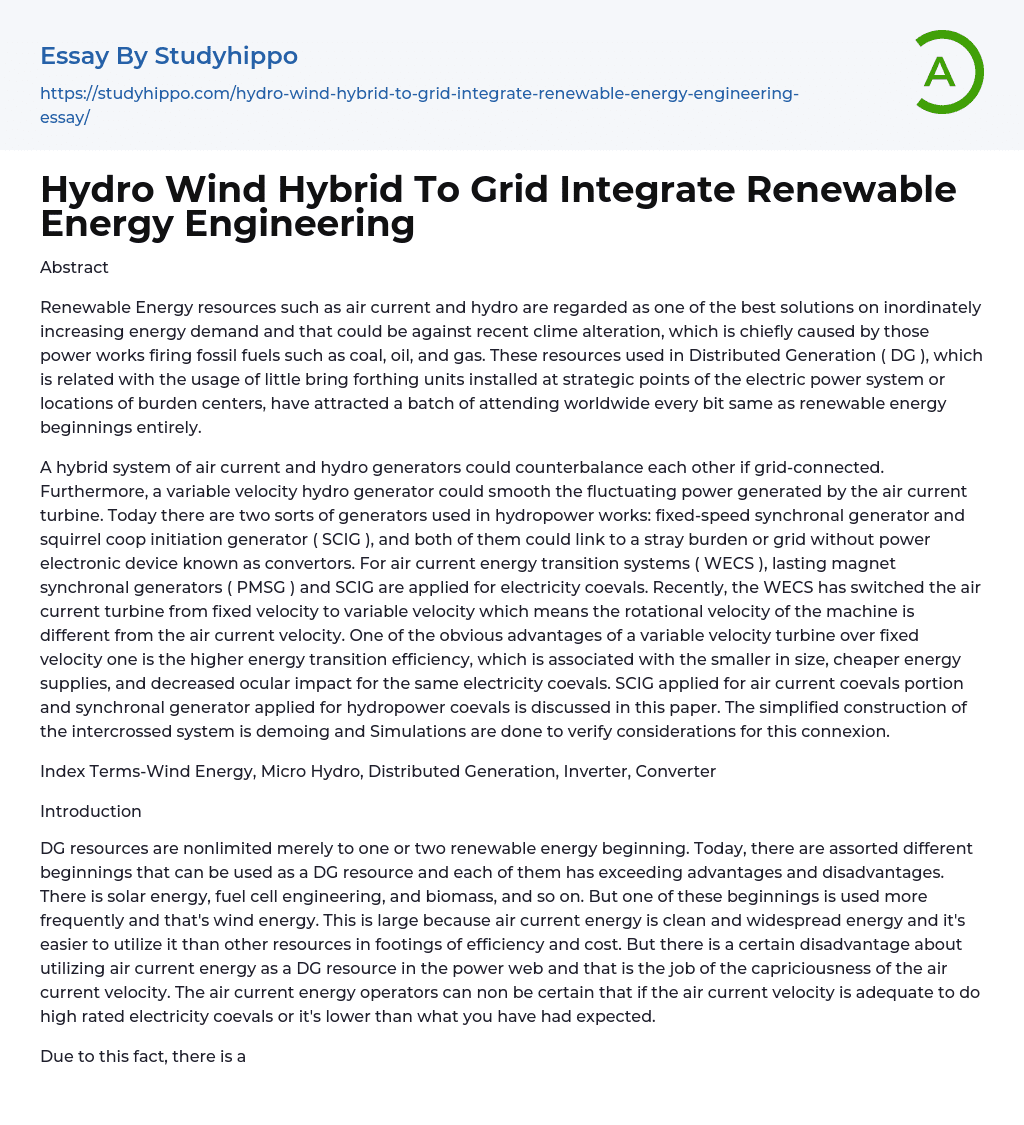
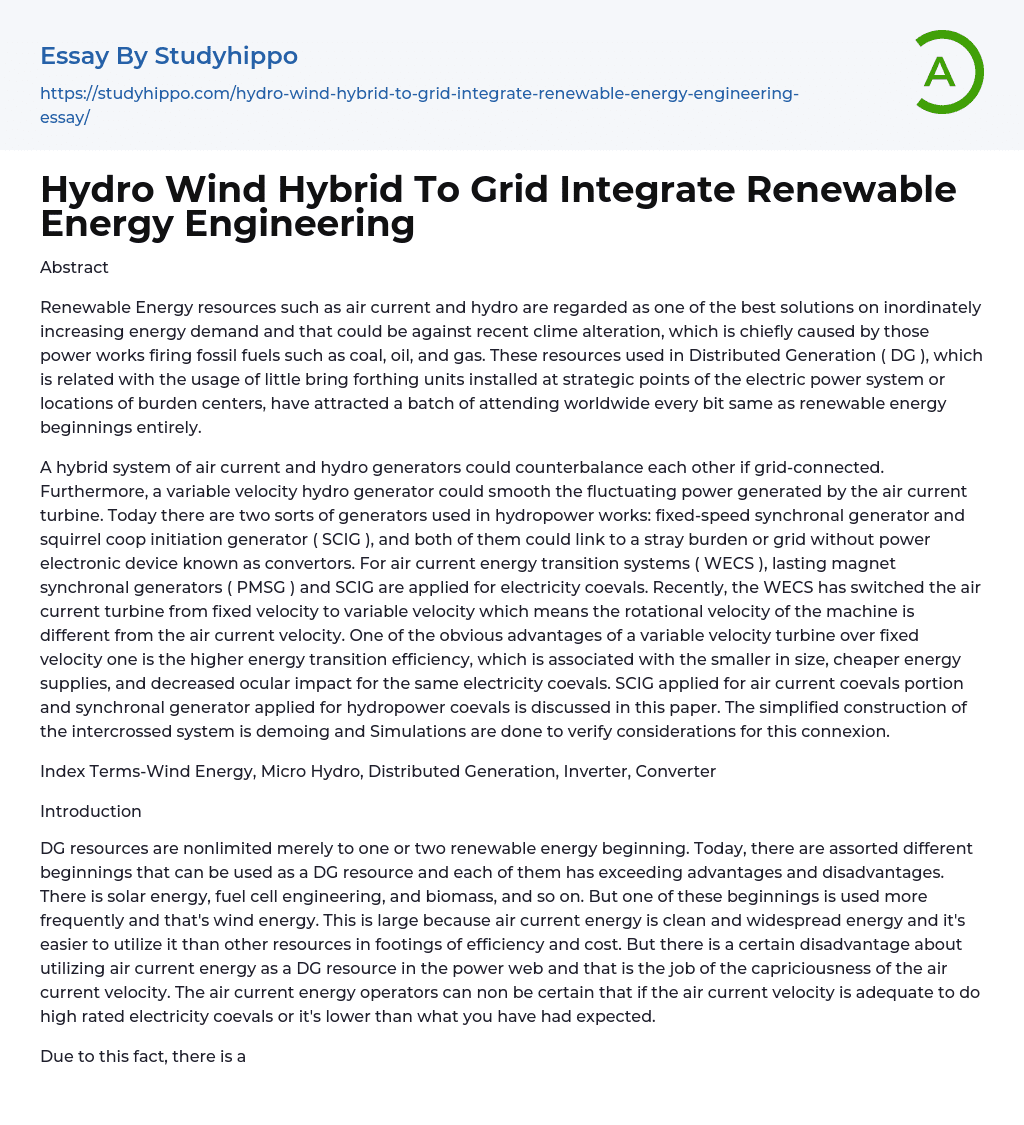
Hydro Wind Hybrid To Grid Integrate Renewable Energy Engineering Essay Example
Abstract
Renewable Energy resources, including wind and hydro power, offer a viable solution for addressing the growing energy demands and combatting climate change. The key advantage of these sources lies in their independence from fossil fuels such as coal, oil, and gas, which are major contributors to climate change.
Distributed Generation (DG) resources, which involve the use of small generating units installed strategically within the electric power system or at load centers, have gained global attention along with renewable energy sources. If connected to the grid, a hybrid system combining wind and hydro generators can compensate for each other. Additionally, a variable speed hydro generator can stabilize the fluctuating power generated by the wind turbine. There are currently two types of generators used in hydropower plants: fixed-speed synchronous generators and squirrel cage induction generators (SCIG). Bot
...h can connect to an isolated load or grid without the need for power electronic devices such as converters. For wind energy conversion systems (WECS), permanent magnet synchronous generators (PMSG) and SCIG are used for electricity generation. Recently, WECS have transitioned from fixed speed to variable speed turbines, where the machine's rotational speed differs from the wind speed.
The advantages of a variable velocity turbine compared to a fixed velocity one include increased energy efficiency, lower cost, and reduced visual impact while still generating the same amount of electricity. This article focuses on the utilization of a squirrel cage induction generator (SCIG) for wind energy generation and a synchronous generator for hydropower generation. It presents a simplified design for integrating these two systems and conducts simulations to verify their compatibility. The keywords associated with this topic are "Wind Energy,"
"Micro Hydro," "Distributed Generation," "Inverter," and "Converter." It is important to acknowledge that distributed generation (DG) resources encompass more than just one or two renewable energy sources, as there are various sources with distinct pros and cons that can be utilized as DG resources.
Wind energy is the most commonly used among various renewable energy sources such as solar energy, fuel cell engineering, and biomass. Its popularity stems from being clean, abundant, and more efficient and cost-effective to harness compared to other resources. However, a drawback of using wind energy in the power network is the unpredictable variation in wind velocity.
The operators of air current energy are uncertain whether the wind velocity is sufficient for generating high-rated electricity or if it is lower than expected. This uncertainty creates a critical need for compensating power and voltage in networks connected to wind Distributed Generation (DG). Often, wind and hydro turbines are connected through a hybrid network to balance each other. In hydro systems, a Variable Speed Drive (VSD) generator is used to smooth the fluctuations generated by a wind turbine. Currently, there are two types of generators used in micro hydropower plants: fixed-speed synchronous generator and squirrel cage induction generator (SCIG). Both types can be connected to either a standalone load or a grid without the need for converters.
For wind energy transition systems (WECS), both permanent magnet synchronous generators (PMSG) and squirrel cage induction generators (SCIG) are used for electricity generation. Recently, the WECS has switched from using a fixed velocity wind turbine to a variable velocity one, where the rotational velocity of the machine differs from the wind velocity. One clear advantage of using a variable
velocity turbine is the increased energy transition efficiency, which leads to smaller size, lower costs, and reduced visual impact while generating the same amount of electricity. This paper discusses the use of SCIG for wind generation and synchronous generators for hydropower generation.
Wind Energy
Generally, wind energy is derived from the potential energy of the Sun. Variations in land temperature across different regions result in the movement of air currents.
Wind energy has four main advantages. Firstly, it is a clean form of energy that does not pollute the environment or society. Secondly, wind sources have a vast potential energy. The global available wind energy is about 2*107 MW, which is ten times greater than hydro energy.
Thirdly, there is an abundance of air current energy and no cost for generation. However, wind energy is not constant and comes from all directions. It fluctuates throughout seasons and varies between countries, as well as within a single day. These factors could be seen as disadvantages of wind power.
In general, there are two ways to demonstrate the effectiveness of wind turbines in a dimensionless form: fixed wind velocity using power coefficient Cp and tip velocity ratio ?, and fixed rotor angular velocity using advancement ratio J and rotor velocity power coefficient Kp. This paper focuses on the first method for simplification purposes.
For a wind turbine with performance coefficient Cp, air density ?, turbine swept area A, and wind velocity Vwind, the output power is determined by the equation. To maximize the output power, the wind turbine should be operated at maximum power coefficient Cp, which is influenced by tip speed ratio ? and blade pitch angle ?.
The highest Cp value is achieved when ? is 0. The relationship between power coefficient Cp and tip velocity ratio ? when ? approaches 0 is important.
The transition of wind energy involves two stages in the system.
The first step in the process involves converting air current energy into mechanical energy, which is then transformed into electrical energy using generators on the turbine. This conversion process must consider factors such as performance, efficiency, and power quality. Additionally, the second step can impact the functionality and construction of the device used in the initial step.
Squirrel cage induction generators have been increasingly utilized in both air current energy systems and micro-hydro energy systems for several decades. However, when these generators are operational, capacitors like analog capacitance, SVC (Static Var Compensator), STATCOM (Static Synchronous Compensator), or synchronous capacitor need to supply reactive power on the generation side. These characteristics may be considered a drawback.
To address this issue, this article proposes connecting a synchronous capacitor and a shunting capacitance to SCIG (Squirrel Cage Induction Generator) to maintain voltage levels.
For an independent country, DC generators and AC generators such as permanent magnet synchronous generators and induction generators can be used in wind power conversion systems to generate electricity. In a grid-connected system, synchronous generators, squirrel cage induction generators, and double fed induction generators can be employed in the wind power generation system. In this case, a squirrel cage induction generator (SCIG) is selected and examined. The SCIG is a conventional generator used for wind energy generation. When a SCIG is operating, it requires reactive power to be supplied to the generator and to maintain the voltage level.
When an induction machine
functions as a generator, the rotational speed of the rotor slightly surpasses the synchronous speed. SCIG is well-suited for wind power generation, as its rotor possesses higher strength, rigidity, and stability. As the technology advances, SCIG is extensively utilized in large wind farms and accounts for a significant percentage of wind power generation. Nevertheless, it is not able to efficiently harness wind energy, resulting in lower conversion efficiency compared to synchronous generators. Nonetheless, the performance of the induction generator continues to improve.
The literature discusses a high-performance air current turbine connected to a public-service corporation grid, which utilizes an initiation generator. The initiation machine, also known as an "asynchronous machine", is praised for its simplicity and ease of fabrication, use, and maintenance compared to other generators. It is also considered more reliable and cost-effective. However, it lacks in terms of start and velocity controlling when compared to synchronous machines and has a lower power factor that may result in reactive power problems. Nevertheless, the induction machine continues to be widely used as a motor worldwide.
The initiation machine, like any other AC machine, consists of a stator and a rotor separated by a small gap. This gap is crucial for enhancing the performance of the initiation machine. In the case of medium or small sized initiation machines, the gap typically ranges from 0.2-2.0mm. Reducing the gap improves the power factor, but it can make the installation difficult, lead to unreliable operation, and cause additional wear and tear. Therefore, the minimum requirements for the machine should be taken into consideration to minimize the excitation current.
The electrical capacity device, such as STATCOM, SVC, or a Synchronous capacitor, will provide
excitement current when the initiation generator is connected to a burden.
Grid Connection Power Electronic equipment
The development of DG engineering has solved the jobs by linking DC-AC-DC convertors. Due to the difference between the rotor velocity and the magnet field rotary motion velocity according to the burden, the output frequency is different from the nominal frequency. An AC-DC-AC converter is necessary on the air current energy system to reform the frequency so that it can be connected to the grid as required.
The AC-DC-AC converters are explained in the next section. To maintain the voltage level, a reactive power source is needed to supply the necessary reactive power. This can be achieved through various sources such as generators, synchronous capacitors, static capacitors, static Var compensators, and Satcom. While static capacitors only absorb capacitive reactive power, other sources can absorb both inductive and capacitive reactive power. An asynchronous capacitor functions like a synchronous motor without a load connection and serves as a reactive power source by providing inductive reactive power during over-excitation.
When operating with under-excitation conditions, the synchronous capacitor absorbs inductive reactive power as a reactive burden. The maximum under-excitation capacity is only 50% - 65% of the over-excitation capacity due to practical and stability requirements. A synchronous capacitor with an automatic excitement system can adjust the reactive power absorption or output based on the voltage level at the installation point to regulate the voltage. Under a system breakdown situation, if there is reinforced excitement equipment, the synchronous capacitor can maintain the voltage as usual and enhance system stability. However, a synchronous capacitor is a complex rotating machine that requires operation and maintenance. The actual power loss can
be significant, reaching 1.5-5% of the full load condition.
The cost of each 1KVA increases as the synchronal capacitor becomes smaller, which is why it is only used for larger capacity needs. Additionally, the response time for velocity is lengthy and it is challenging to adjust reactive control dynamically. As a result, SVC is used instead of synchronal capacitors. A Static capacitor can provide reactive power Qc directly proportional to the square of voltage V.
The equation can be expressed as follows in equation (2.5): In this equation, Xc = 1/wc, which represents the reactance of the inactive compensator. When the voltage at the nodal point decreases, the reactive power to the system also decreases. When the system experiences fault conditions or a voltage drop due to other reasons, the voltage level continues to decrease. The reactive power control provided by the inactive capacitor is not very effective. The inactive Var compensator (SVC) is composed of an inactive capacitor and a capacitance connected in parallel. The SVC can either consume capacitive or inductive current from the network [14].
The capacitor has the ability to absorb reactive power, while the inactive capacitor can produce reactive power. When combined, these two can smoothly alter the reactive power. The inactive Var compensator can quickly and smoothly adjust reactive power to meet the demand for dynamic reactive power compensation when the voltage changes. It is easier to operate and maintain than synchronous capacitors, and also has lower power losses, faster response, and strong adaptability to inrush current. TCR and TSC can also compensate for the imbalance in a three-phase system caused by varying loads.
Satcom is an advanced compensator for reactive power. It
utilizes a combination of 6 GTO (Gate Turn-Off) and 6 rectifying tubes to generate an electromotive force. The GTO enables control over the DC electromotive force within the capacitance, allowing its conversion into AC electromotive force to match the three-phase electromotive force in the power system. The AC component of the inverter is connected to the power system through a transformer or reactor in parallel. Satcom can adjust its operation by controlling the output electromotive force of the inverter, making it suitable for situations with inductive burden, capacitive burden, or no burden. To modify both magnitude and frequency of the electromotive force, an AC-DC-AC converting system employs a three-phase rectifier and a three-phase inverter.
Power electronic devices, such as rectifiers and inverters, are used in renewable energy systems to convert power into suitable forms for connection to the grid. The grid ensures a constant voltage and frequency. AC-DC-AC converters consist of a three-stage rectifier, a three-stage inverter, and an LC filter. In this setup, an uncontrolled rectifier generates a steady voltage output. The DC voltage is then smoothed by the LC filter in the DC link, while voltage control is integrated into the inverter. The grid-side inverter maintains the DC bus voltage between the two converters. Switch mode inverters have been applied in various power system projects like uninterruptible power supplies, communication ring generators, aerospace power systems, and variable-speed AC machine drives to convert DC voltage to AC voltage.
The switch-mode is extensively utilized in numerous applications due to its favorable performance in both steady-state and dynamic periods. The switch-mode inverters have three main characteristics. First, in a Voltage Source Inverter (VSI), the dc side functions as
an electromotive force source that may sometimes bypass through a large capacitance, whose resistance is inconsequential. Conversely, in a Current Source Inverter (CSI), the dc side is connected to a large inductance in series, acting as a current source with negligible resistance. Second, in a VSI, the output voltage on the ac side takes the form of a square waveform due to the clamping of the voltage source.
The output of the current waveform in the current wave is varied based on different tones. However, in a CSI, the output current on the AC side is a square waveform because the thyristor only alters the current direction. Finally, when the load is inductive, reactive power needs to be supplied. The capacitance or inductance on the DC side is used for reactive buffering effect. The three-phase bridge-type inverter is the most commonly used three-phase inverter. This type of inverter can be considered as a three-phase half-bridge inverter.
The three-phase bridge-type inverter operates similarly to the single-phase bridge-type inverter, where each device is turned on for 180° as needed. At each stage, two subdivisions switch alternately, with each stage having a different firing angle separated by 120°. This results in three subdivisions working simultaneously. To convert the current into AC with a frequency of 50Hz, a PWM-controlled three-stage inverter is used as a grid-side converter. By controlling the opening and closing of IGBT/diodes through PWM, the voltage waveform is obtained after passing through an LC filter.
For a grid-connected inverter, the controlled pulse signal for the inverter can be generated using an end product accountant, a PWM Generator, and a Unit Delay to regulate the stability of the AC
output voltage. The physical structure of the output accountant is illustrated by the Matlab package.
Hydro Energy
Hydro energy is considered a form of renewable energy due to the endless potential energy of water. Unlike fossil fuel and nuclear power plants, hydro energy does not involve a second conversion from heat to electricity. There are numerous advantages of hydro energy over power plants that use fossil fuels and nuclear fuels. Firstly, hydro energy can be obtained continuously due to its cyclic nature. In contrast, the fuels used in coal-fired power plants and nuclear power plants are non-renewable.
The utilization of hydro energy can effectively reduce the consumption of fossil fuels, thus extending the limited availability of oil and coal while promoting environmental sustainability. Furthermore, hydro energy has diverse applications. Apart from electricity generation, hydro power plants can also perform tasks such as flood prevention and control, irrigation, transportation, water supply, and fishing. Additionally, the water flowing upstream can provide water supply and energy to downstream hydropower plants.
Thirdly, hydro power works are more cost-effective and efficient compared to fossil fuel power plants. The use of hydro energy eliminates the need for transportation and development costs, as well as the need for fuels. Additionally, the equipment used in hydro turbines and associated machinery is smaller in size, requiring less maintenance and operation personnel, leading to reduced capital and operational costs. Fourthly, hydro energy exhibits significantly higher efficiency than fossil fuels. Generally, hydro electricity generation has an efficiency rate of 85%, with only a small percentage of losses.
Hydro energy is considered the most cost-effective form of electricity generation. It has several advantages over other renewable energy technologies. Firstly, it does not
release harmful gases, dust, or other pollutants, resulting in cleaner air and a healthier environment. Additionally, there is less wasted water, no chemical pollution or heat waste, and no risk of nuclear radiation. These factors contribute to the overall well-being of humans and the ecosystem. Furthermore, hydropower can be stored in reservoirs, unlike electricity. Excess water from rainfall can be stored in the reservoirs for future use in electricity generation when the water supply is lower than the demand. This provides a backup power source and increases efficiency in utilizing available resources.
This could set the balance between supply and demand and also improve the flexibility and economy of electricity generation.
Grid Connection of Hydro turbine
Generally, hydro energy, based on the potential energy in falling water, can provide a constant value of energy to the hydraulic turbine regardless of changes in external factors such as temperature. The prime mover of the hydraulic turbine can be utilized to drive either a synchronous machine or a permanent magnetic synchronous machine.
In the hydro energy system, a synchronal machine is chosen as a generator. It functions with the rotor and magnet revolving at the same speed. The relationship between the rotor velocity N, frequency degree Fahrenheit, and pole pair number P is shown in an equation. Compared to generators used in fuel-fired plants, the rotor speed of a synchronal generator connected to a hydro turbine cannot be much higher. Therefore, the pole pair number must be set higher. In this case, it is set to 20. According to the 50Hz system, the rotor speed is 150 rotations per minute. The grid connection can be regarded as multiple synchronal generators working together,
which offers numerous advantages in supplying energy to the load.
Originally, the parallel operation map could improve the power quality of usage. Currently, the grid has enough capacity to handle disturbances and turbulence in the power system due to reasons like errors, loss of generator units, or issues in transmission lines. A single generator's capacity is much smaller than that of the entire grid. However, when generators are connected to the grid in parallel, the voltage and frequency remain constant.
If a synchronous machine is connected to the grid, there is no risk of the entire system's voltage and frequency varying, which can be expressed by the mathematical equation: In the UK, the frequency is 50Hz. The grid, with a constant frequency and voltage, can be seen as an infinite grid for a single generator. Additionally, the electric power can balance each other out and reduce the need for backup storage capacity. Furthermore, unnecessary generators can be disconnected from the grid based on regulations regarding changing load in different seasons or even within a single day, resulting in cost reduction. Moreover, power plants can improve their interests in response to increasing demand. Lastly, the reliability of the power supply will be enhanced.
One individual generator operation map and a large capacity demand do not have a significant impact on the grid due to its large capacity. When a synchronous machine is connected to the grid, there will no longer be an occurrence of inrush current in the circuit after a short period of time. To achieve this, the grid-connected generator must meet four conditions, which are explained below:
- The frequency of the generator must match the frequency of the
grid.
The synchronous machine can be divided into two types: non-salient pole generator and salient pole generator. The air gap of the non-salient pole generator remains constant, while that of the salient pole generator does not.
For a high-velocity synchronous generator, with a rotary motion velocity of more than 3000r/min, a non-salient pole generator is used to generate electricity. However, the rotary motion velocity cannot reach such high speeds, so outstanding pole generators are used. In the case of hydro turbines, outstanding pole generators are used in the transition system because hydro turbines have a low-speed prime mover. The purpose of linking the generator to the grid is to supply power to it. Generally, after the generator is linked to the grid for a short period of time, it can still be considered the same without any load connection.
The input mechanical power of the generator is equal to its no-load loss, resulting in no transformation of power to electromagnetic power. If the input mechanical power exceeds the no-load loss, the remaining power is converted to electromechanical power, allowing the generator to supply active power to the grid. The active power output from the generator is determined by the input mechanical power, which can be adjusted to change the active power output. By adjusting the input mechanical power, the active power of the generator connected in parallel to the grid can be modified. Simultaneously, the voltage angle will automatically change, causing variations
in electromagnetic power and output power, ultimately establishing a new balance between the generator and the grid.
Figure 4.3 demonstrates the steady-state features. The procedure for providing direct current through the excitement twists during operation of the synchronal machine is shown below. The excitement current is typically supplied by a small District of Columbia generator known as an exciter.
The excitement system plays a crucial role in maintaining the electromotive force levels of the generator and grid in accordance with the load. It has several functions, including providing excitation current to the generator to regulate the terminal electromotive force and adjusting the excitement current to stabilize the power system during voltage drops or short circuits. Additionally, it can reduce exciting current to limit the terminal electromotive force when losing some tones and minimize the damage caused by a short circuit. Furthermore, it can regulate reactive power and distribute it when multiple generators are connected to the grid. The excitement system should have a fast and reliable reaction speed, simple equipment structure, ease of maintenance and repair, among other qualities.
Simulation Consequences
The following diagram illustrates a 25kV grid-connected hybrid system that combines wind and hydro energy. It includes a synchronous generator connected to a hydraulic turbine and a SCIG connected to a wind turbine. Additionally, an air current generation system based on a SCIG is equipped with a synchronous capacitor and a shunt capacitance to provide active power. An LC filter is also utilized between the AC-DC-AC converters to eliminate DC ripples.
The main function of a Voltage regulator is to provide a steady AC voltage as an output signal, which is connected with a PWM generator
and Unit delay to produce the control pulse. A three-phase induction and capacitance act as an AC filter to isolate and filter out the harmonics. A step-up transformer increases the voltage from 500V to 25kV to power the grid. Below are the simulation results.
The main simulation circuit can be seen on the following page. It is important to note that the grid has a large capacity and the electromotive force and frequency remain fixed regardless of the size of the varied burden or the disturbance due to factors such as mistake occurring or losing a generator unit. For hybrid systems with DG technology, grid connection can support the burden accurately and economically by allowing excess energy to be sold back to the grid.
A 25KV 50Hz power system is created to demonstrate the grid. A fixed time interval of Ts = 2*10-6s is chosen for measurements, and a convergent-minded thinker uses the ode45 (Dormand-Prince) method to replicate the theoretical model.
Decision
This paper discusses and simulates the performance of a wind and hydro hybrid system connected to the grid using Matlab. The MatLab simulation employs synchronous machines and induction machines to represent the wind and hydro energy generation system. The rectifier and inverter components are separately modeled within Matlab. In this hybrid system combining wind and hydro, the low capacity turbines and generators are utilized for micro generation connected to the grid.
The simulation results demonstrate the feasibility of constructing contemporary generation facilities. However, this may be restricted by the harsh environment and high cost. Thankfully, as wind and hydro hybrid technologies advance, the price is expected to decrease. Individuals will be able to afford micro generation facilities for
their homes. There will be a variety of equipment options available to enhance energy efficiency. Due to the incorporation of large components from the sim power system and Simulink in Matlab, errors can occur when even a single setting is modified.
When the system loses grid support, the synchronous generator acts as if it lacks an anchoring system. The ratio of the three-phase transformer does not match the simulation result, and different performances are observed with the same settings but different types of three-phase transformers (such as a 12-terminal element and a two-twist component). Future work can be conducted to refine the model for this project. Due to the complex settings, the model runs smoothly under continuous conditions. Currently, only a simplified model is constructed. To obtain more accurate results, a larger or more advanced computer is required.
The utilization of renewable resources in the generation system is increasing due to the depletion of fossil fuels and growing awareness of their impact on the climate. Hybrid systems will play a crucial role in managing the energy transition in the near future.
- Atom essays
- Big Bang Theory essays
- Density essays
- Electricity essays
- Energy essays
- Force essays
- Heat essays
- Light essays
- Motion essays
- Nuclear Power essays
- Physiology essays
- Sound essays
- Speed essays
- Temperature essays
- Thermodynamics essays
- Automobile essays
- Bus essays
- Civil engineering essays
- Cycling essays
- Electric Car essays
- Genetic Engineering essays
- Hybrid essays
- Innovation essays
- Internal Combustion Engine essays
- Invention essays
- Mechanical Engineering essays
- Mechanics essays
- Software Engineering essays
- Telephone essays
- Air Pollution essays
- Carbon Dioxide essays
- Climate essays
- Deforestation essays
- Ecology essays
- Endangered Species essays
- Environmental Issues essays
- Environmental Protection essays
- flood essays
- Greenhouse Gas essays
- Hurricane essays
- Nature essays
- Pollution essays
- Renewable Energy essays
- Sustainability essays
- Tornado essays
- Traffic essays
- Tsunami essays
- Water Pollution essays