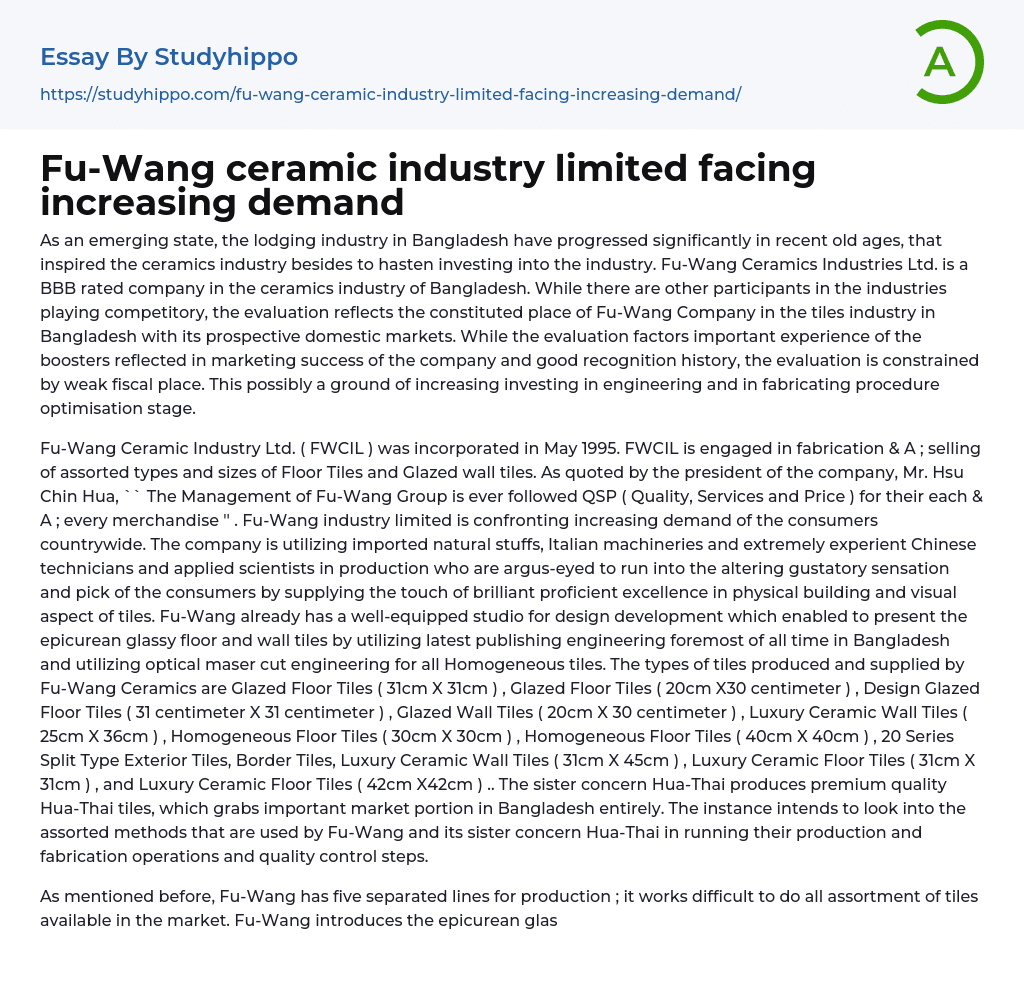
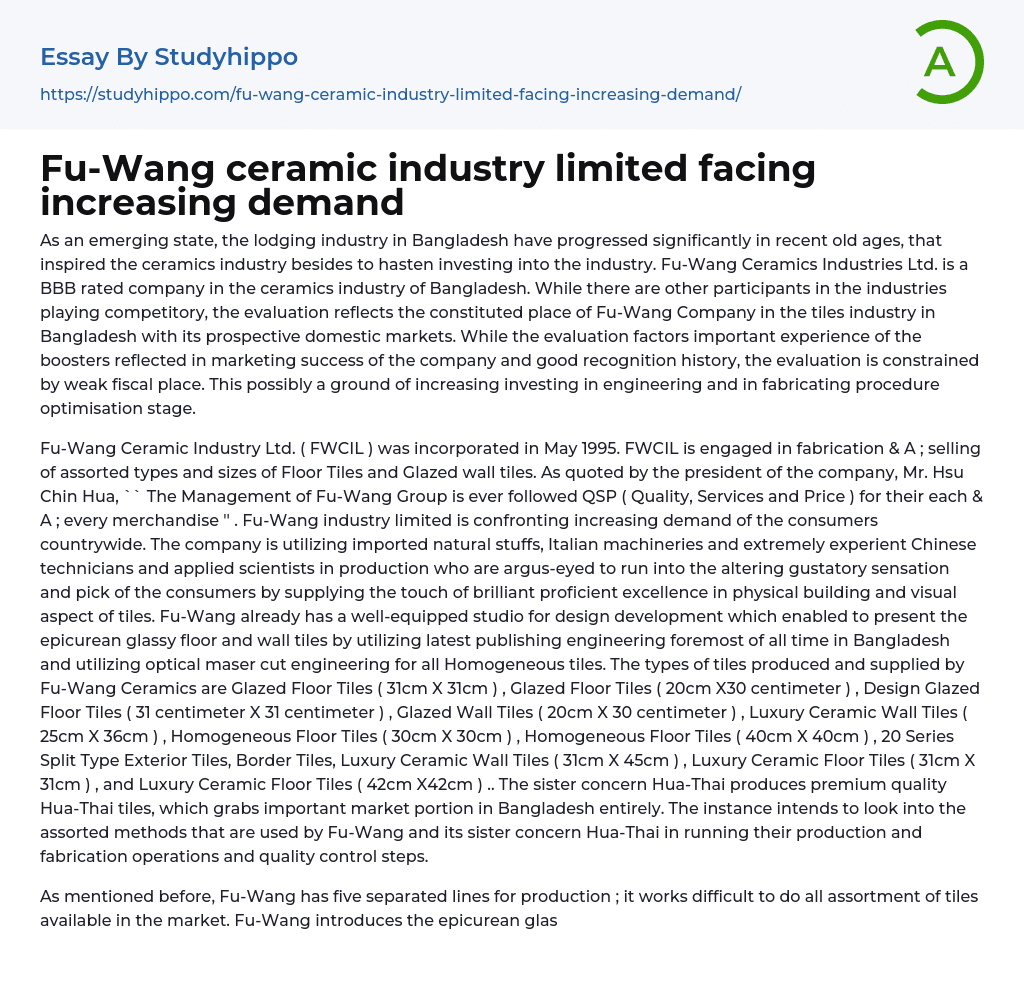
Fu-Wang ceramic industry limited facing increasing demand Essay Example
Responding to the recent progress in the lodging industry in Bangladesh, Fu-Wang Ceramics Industries Ltd. has increased its investment in the sector.
Fu-Wang Ceramic Industry Ltd. (FWCIL) is a ceramics company in Bangladesh with a BBB rating. Despite facing competition, Fu-Wang's rating reflects its strong presence in the country's tiles industry and potential for growth in the domestic market. The evaluation considers the founders' extensive experience, which is evident in their marketing achievements and positive reputation. However, FWCIL's weak financial position limits the evaluation. This could be addressed by investing more in technology and streamlining the manufacturing process. FWCIL was established in May 1995.
FWCIL is involved in the production and sale of various types and sizes of Floor Tiles and Glazed wall tiles. According to Mr. Hsu Chin Hua, the company's president, "The Management
...of Fu-Wang Group always adheres to QSP (Quality, Services and Price) for every product." Fu-Wang industry limited is facing a growing demand from consumers nationwide. The company uses imported raw materials, Italian machinery, and highly skilled Chinese technicians and engineers in production to meet the changing taste and preferences of consumers. The goal is to provide tiles with excellent technical quality and appearance.
Fu-Wang is equipped with a well-equipped design studio enabling the presentation of glassy floor and wall tiles using the latest publishing and laser cut technologies. The types of tiles produced by Fu-Wang Ceramics include glazed floor tiles (31cm X 31cm), glazed floor tiles (20cm X 30cm), design glazed floor tiles (31cm X 31cm), glazed wall tiles (20cm X 30cm), luxury ceramic wall tiles (25cm X 36cm), homogeneous floor tiles (30cm X 30cm), homogeneous floor tiles (40cm X 40cm), 20 serie
split type exterior tiles, border tiles, luxury ceramic wall tiles (31cm X 45cm), luxury ceramic floor tiles (31cm X 31cm), and luxury ceramic floor tiles (42cm X 42cm). The sister concern, Hua-Thai, produces premium quality Hua-Thai tiles and holds a significant market share in Bangladesh. This investigation focuses on the various methods employed by Fu-Wang and Hua-Thai in their production, fabrication, and quality control processes. Fu-Wang operates five separate production lines and strives to offer a wide variety of tiles in the market.Fu-Wang, the leading company in Bangladesh, presents the revolutionary epicurean glassy floor and wall tiles. These tiles showcase cutting-edge printing technology, marking a significant milestone in the country's history, while also incorporating laser cut technology for all Homogenous tiles.
Fu-Wang is revolutionizing the tiles market in Bangladesh by deploying advanced mechanisms and engineerings. It offers the same quality as European tiles at a low-cost monetary value, making it accessible to all valuable Bangladeshi consumers for comfortable, hygienic, and stylish home life. Fu-Wang's excellent quality has earned it the ISO-9002 certification in 1998. This has made Fu-Wang a preferred choice among users in Bangladesh. Currently, Fu-Wang tiles are also exported to India and Pakistan.
The Fu-Wang Management Team is dedicated to elevating Fu-Wang to higher levels of success by ensuring top line revenues through their expertise and capabilities. This unique management team can anticipate business needs by utilizing innovative technology solutions and restructuring the organization for maximum profitability. The corporate management of the Company consists of 7 managers, with the Chief Executive serving as the Managing Director who oversees all planning and control responsibilities.
Other managers and highly skilled and experienced personnel support him. This diverse group
of individuals at Fu-Wang Ltd. is dedicated to providing unmatched service to their clients, developing timely and innovative products and services, and improving the skills of their workforce while focusing on the latest technology. In order to commemorate the process optimization milestone set by Fu-Wang Ceramics, it is important to outline the detailed production process. Taking into account the manufacturing process of Fu-Wang (Wall-tiles), it serves as a benchmark.
Fu-Wang tiles buy the raw materials from Mymensingh. The white clay and red clay are crushed and placed in the ball mills. During this process (W), the crushed clay is mixed with water to create ceramic clay. After the ceramic clay is manufactured, it is stored in the slide (X). The slide can hold 30 tons of clay.
Magnet extractor (Y) is used to extract the magnets from the clay. The clay is then dried and pulverized using a spray drier (Z). This mill has a total of 6 silos, with each silo having the capacity to store 70 tons of clay powder. These silos are utilized for the storage of clay powder for pressing.
There are 6 silos that are connected to two pressing machines (A). A pressing machine is a hydraulic machine that operates on a home base. The home base has the surface design of the tiles and clay pulverization from the silos is poured into it. The machine applies a hydraulic force of 250 tons per unit area to compress the pulverization.
Next, the pulverization is shaped appropriately and transported onto the conveyor belt. The mill features a 3-layer drier (B), which is employed to remove any excess moisture from the surface of the natural tiles.
The startup time for this dryer is 20 minutes and it has a capacity of 645 square feet. Once the natural tiles are dried, they are sent to a conveyor belt and transported to the dusting area. Manual surface dusting (C) is performed by one person who cleans the upper surface of the tiles. The next step (D) involves applying color to the surface of the natural tiles.
Glaze spray (E) is applied to coat the surface of tiles. In the subsequent stage (F), side glaze is reduced. This factory has five roller printing machines (G). These printers imprint the surface design individually in five phases.
After chilling, the manual review begins where the quality accountant inspects each and every tile for texture problems, deformation, spots, edge breaks, and color using their own judgement. The Accumulator reserves the tiles for firing. After glazing, the tile must undergo intense heating to strengthen it. Kiln fires the tiles. Cooler fan is used to cool the discharged tiles. Then, the finished tiles are inspected for any edge breaks.
Tiles are manually packed into battalions, with each battalion containing 10 tiles. The battalions are then taken to the stock list.
Findings of Fu-Wang Wall Tiles production procedure:
A) CT (Cycle clip) = 2.49 Second
B) Output = Total Time Available/Cycle Time = 24*60*60/2.49 = 34699 degrees Celsius
C) Entire Activity Time = 0.43 + 0.34 + 0.58 + 0.69 + 2.35 + 1.16 + 1.74 + 1.16 + 0.87 +
0.58 +
1.16 +
1.
16
+
0.
87 +
2.
49 +
1.
00 +
1.
16 +
0.
58 =
18
.
29 Second vitamin D) Total Idle Time =
2
.
06 +
2
.
15 +
1
.
91 +
1
.
8 +
0
+
14
+ %
degree Fahrenheit ) % Utilization = - %. The precedence diagram of Fu-Wang Wall Tiles fabrication procedure shows a straightforward diagram as signifier the precedence relationship it is clear that each undertaking has to go after the earlier one.
The procedure begins by performing Step W, which is the Ball mill step, and separating it with Step M, which is the packaging measure. We have determined the total time based on one SFT of tiles produced. We are aware that Cycle Time is the longest processing time in the procedure. Currently, Cycle Time is 2.49 seconds, which occurs during Step J (Kiln).
The total activity clip is currently 18.29 seconds and it represents the sum of the entire undertaking clip. The achievable output of this process is 34,699 SFT tiles per day. Idle time in each station is the difference between the demanding position's undertaking time and the cycle time. In this process, the total idle time is 24.01 seconds, resulting in 56.72% idle time.
And use of this procedure is 43.27%.
Proposed production procedure of Fu-Wang Wall Tiles:
Desired Output = 60,000 Required CT = Total Time Available/Desired Output= 24*60*60/60,000= 1.44
Findingss for proposed procedure of Fu-Wang Wall Tiles:
A) CT = 1.24 Sec B) Output = Total Time Available/CT= 24 * 60 * 60/1.24= 69,677 square feet per day C) Entire Activity Time = 0.43 + 0.34 + 0.58 + 0.69 + 1.17 + 1.17 +1.16 + 0.87 + 0.87 + 1.16 + 0.87 + 0.58 + 1.16 + 1.16 + 0.87 + 1.24 + 1.24 + 1.00 + 1.16 + 0.58 = 18.3 Second D) Total Idle Time = 0.81 + 0.9 + 0.66 +
0.55 + 0.07 + 0.07 + 0.08 + 0.37 + 0.37 + 0.08 + 0.37 + 0.66 + 0.08 + 0.08 + 0.37 + 0 + 0 + 0.24 + 0.08 + 0.66 =6
5 Second E) % Idle tile = Total Idle Time / ( CT x No.
of Stations )=6
5 / (1
24 x20 )=26
20 %
F)
%
Utilization =100- 26
20 =73
79 % As of the penchant relationship it is evident that grouping of undertaking is non executable.
Bottleneck of current procedure is step A, C and J.
As a consequence our suggestion of this procedure is to infix one Pressing machine, one manual dust storm and one Kiln as parallel Stationss at measure A, C and step J.
This jutting procedure will supply a Cycle Time of 1.24 sec.
As a result, it will reduce the overall idle time. This anticipated process will provide 26.20% idle time and utilization of 73.79%. Therefore, this proposed process will offer approximately 30% higher utilization than the existing process.
Problem Solving Session 1
Hua Thai (Floor Tiles) Manufacturing Process: The main raw material for the floor tiles is ceramic clay. Fu-Wang tiles imports ceramic clay from Malaysia. Each bag of ceramic clay powder weighs 1.05 ton. Ceramic powder is lifted to silos.
There are three silos in this mill. Silos are used for storing the ceramic clay powder for pressing. Two of the silos are in constant operation while one is kept as a backup. Each silo has a capacity of 42 tons of ceramic powder.
The procedure description goes as follows. Each silo is connected to a hydraulic machine (machine A). This machine is a pressure machine that has a home base beneath it.
Within this home base, the
surface design of the tiles is created. Ceramic powder is extracted from a silo and poured into this home base. A machine applies a hydraulic force of 250 tons per unit area to press the powder, giving it the desired shape. Once formed, the powder is then transported to the conveyor belt.
The mill has one 3-layer drier (B) which is used to remove excess moisture from the surface of the natural tiles. The startup time for this drier is 20 seconds, and its capacity is 645 square feet. After drying, the natural tiles are then transported to the conveyor belt and pass through the dust storm (C), which is used to clean the upper surface of the tiles.
The blower is utilized to remove light dust from the surface. For glazing the tiles, the glaze spray (D) is applied. Additionally, this mill is equipped with two optional roller printing machines (E) that are used when extra printing is required. Prior to firing, an anti-adhesive coating (F) is applied underneath the tiles to prevent them from sticking in the kiln (oven).
Alumina is utilized as an anti-adhesive substance. The accumulator (G) stores the tiles for firing, with a capacity of 360 square feet. In stage (H), the tile undergoes a low-temperature fire known as bisque firing prior to the final firing. The glaze drier eliminates any excess glaze from the natural tiles before firing.
After the glazing process, it is necessary to heat the tile at a high temperature to strengthen it and give it the desired porousness (I). This is done in a specific firing machine designed for firing natural tiles. The tile and glaze are fired together
in a process known as GLOST fire. Both firing processes occur in a tunnel or continuous kiln. This kiln is made up of a chamber where the ware can be easily moved on a conveyor, which is placed on furnace lining BATTS-shelves made of heat-resistant materials- or in containers called SAGGERS. The kiln has an output of 16 square feet per minute.
This is the process where soft natural tiles are changed into harder tiles through different firing beds. A cooler fan ( J ) is used to cool the tiles after they are discharged. After cooling, a manual review is conducted by a quality controller who inspects each tile for texture issues, deformation, spots, edge breaks, and color using their own judgment ( K ). They then categorize the tiles as follows:
- Grade A: No defects.
- Grade B: One or two defects.
- Grade C: More than two defects.
Once the tiles have been inspected, they are kept in a designated area and chilled at room temperature for 8 hours straight ( L ). Then, the cooled tiles are taken for squaring and scaling. Prior to cutting the edges, water is sprayed onto the surface of the tiles ( M ).
To ensure the cutting process is not interrupted, there are two cutting machines. These machines cut the tiles to the desired size, known as the squaring and scaling stage (N). The Water Dryer (O) is used to dry the water that was sprayed earlier. The Heater (P) warms the tiles and prepares them for
packing. During the Final physical review (Q), completed tiles are inspected for any border interruption.
Finally, during the packaging stage (R), the tiles are manually packed into battalions of 10 tiles each, which are then taken to the stock list.
- Question 1: Determine the entire activity clip, entire idle clip, percentage of idle tile, and percentage of use. Provide remarks on your findings.
- Question 2: Determine the entire activity clip, entire idle clip, percentage of idle tile, and percentage of use. Provide remarks on your findings.
- Question 3: Identify the bottleneck in the system and propose methods for its removal. Comment on what machinery can be added to alleviate the constraint.
- Question 4: Analyze the system and suggest process optimization.
Quality CONTROL
Most modern tile makers now utilize statistical process control (SPC) for monitoring various processing parameters. They also collaborate closely with their raw material suppliers to ensure that specifications are met prior to material usage. Statistical process control involves the use of charts to monitor parameters such as particle size, milling time, drying temperature and time, compression pressure, dimensions after pressing, density, firing temperature and time, and more.
These charts help identify jobs with equipment and out-of-spec conditions, and contribute to better outputs before the final merchandise is completed. The final merchandise must meet specific specifications related to physical and chemical properties. To determine these properties, standard tests established by the Bangladesh Standard Testing Institution (BSTI) are conducted. The measured properties include mechanical strength, scratch resistance, chemical resistance, water absorption, dimensional stability, frost resistance, and linear coefficient of thermal expansion. Our study companies, Fu-Wang ceramics (wall tiles) and Hua-Thai Ceramics (floor tiles), are registered with ISO 9002.
During our mill visit, we
observed minimal choice control measures being implemented, with only a few manual reviews taking place. There was a lack of statistical record keeping for the entire batch's end product and the number of Grade A, Grade B, and bit tiles. Quality control inspectors primarily focused on identifying defects such as texture, deformation, topographic point, color, and two-dimensionality. To conduct our analysis, we utilized a data set containing 36 observations regarding the quantity of Grade A, Grade B, and bit tiles from a single line of Hua-thai ceramics.
The rest of the company's lines did not provide any information, so we do not know if they have maintained any kind of record or not.
Quality control Data of Hua-Thai Floor Tiles:
We have considered Grade A as the main product and Grade B as our faulty product as well and have conducted the analysis based on that. Grade A represents no defects, Grade B represents 1-2 defects, and Scrap represents more than 2 defects in the tiles' end product. The batch size is 2180 SFT of homogeneous floor tiles.
Relationship diagram between different Grades of end product:
The following diagrams illustrate the relationships between various types of end products.
Rate A V Bit
The relationship between Rate A and Scrap is negative. As Grade A increases, the amount of scrap decreases. This can also be seen in the linear line drawn.
Problem solving session 2
- Question 1: Using quality control data, analyze and define the relationship between grade A and grade B. Comment on your findings.
- Genetic Engineering essays
- Bus essays
- Internal Combustion Engine essays
- Hybrid essays
- Electric Car essays
- Invention essays
- Mechanics essays
- Innovation essays
- Telephone essays
- Software Engineering essays
- Automobile essays
- Cycling essays
- Civil engineering essays
- Mechanical Engineering essays
- Bentley essays
- Automotive essays
- Real Estate essays
- Construction essays
- E Commerce essays
- Commerce essays
- Polymers essays
- Automotive Industry essays
- Paper Industry essays
- Textile Industry essays
- Pharmaceutical industry essays
- Pharmacy essays
- Grocery stores essays
- Classical Mechanics essays
- Rail Transport essays
- Tata Motors essays
- Vehicle Brands essays
- trucks essays
- Auto Racing essays
- Harley-Davidson essays
- Suzuki essays
- Lexus essays
- Mercedes-Benz essays
- Buying Homes essays
- Futures Contract essays
- Mortgage Loan essays
- Renting essays
- Transaction Cost essays
- Building essays
- Optical Fiber essays
- Freezing essays
- Polymer essays
- Weaving essays
- Bangladesh essays
- China essays
- Hong Kong essays