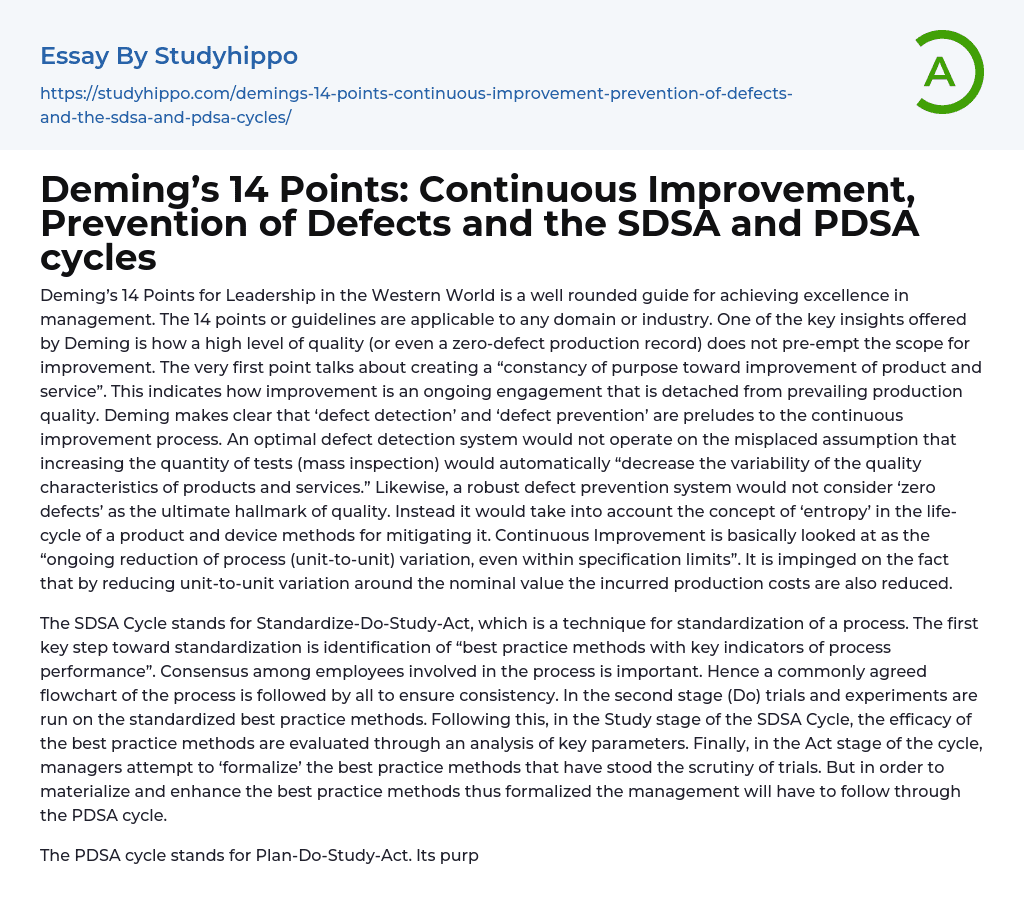
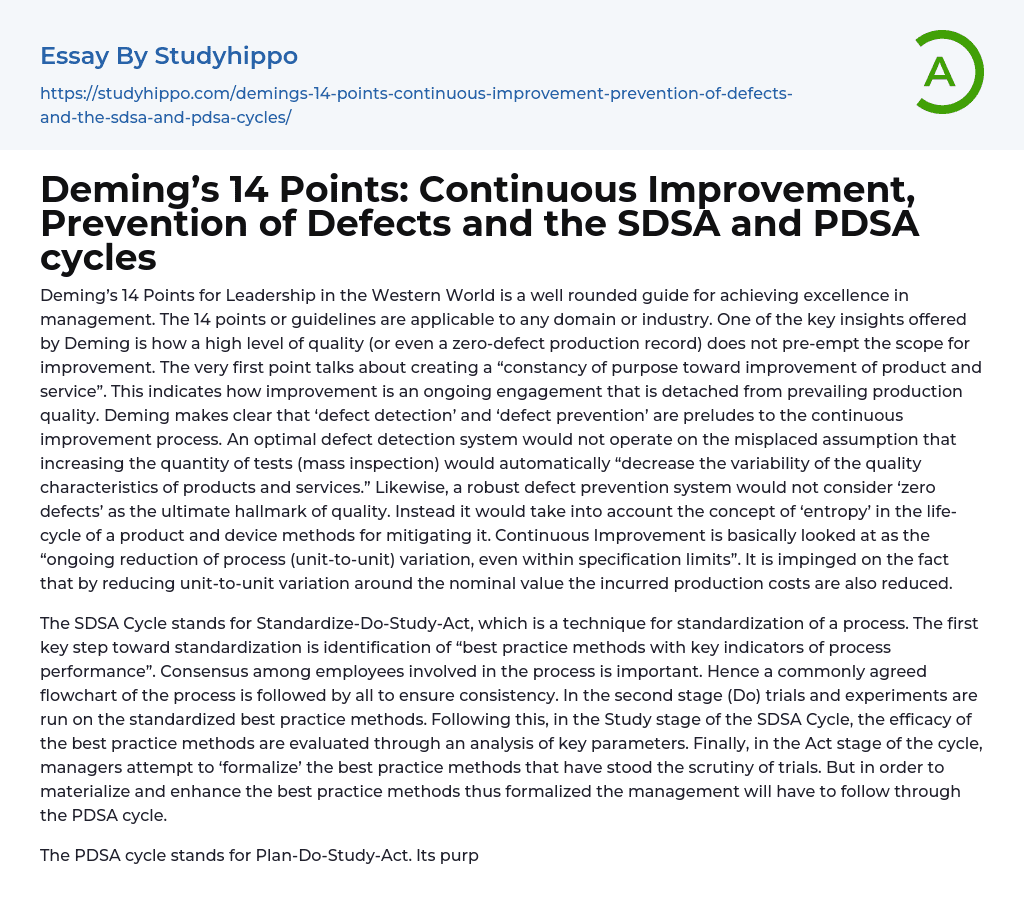
Deming’s 14 Points for Achieving Excellence in Management
Demingâs 14 Points for Leadership in the Western World is a well rounded guide for achieving excellence in management. The 14 points or guidelines are applicable to any domain or industry. One of the key insights offered by Deming is how a high level of quality (or even a zero-defect production record) does not pre-empt the scope for improvement. The very first point talks about creating a âconstancy of purpose toward improvement of product and serviceâ. This indicates how improvement is an ongoing engagement that is detached from prevailing production quality. Deming makes clear that âdefect detectionâ and âdefect preventionâ are preludes to the continuous improvement process. An optimal defect detection system would not operate on the misplaced assumption that increasing the quantity of tests (mass inspection) would automatically âdecrease the variability of the quality chara
...cteristics of products and services.â Likewise, a robust defect prevention system would not consider âzero defectsâ as the ultimate hallmark of quality. Instead it would take into account the concept of âentropyâ in the life-cycle of a product and device methods for mitigating it. Continuous Improvement is basically looked at as the âongoing reduction of process (unit-to-unit) variation, even within specification limitsâ. It is impinged on the fact that by reducing unit-to-unit variation around the nominal value the incurred production costs are also reduced.
The SDSA Cycle stands for Standardize-Do-Study-Act, which is a technique for standardization of a process. The first key step toward standardization is identification of âbest practice methods with key indicators of process performanceâ. Consensus among employees involved in the process is important. Hence a commonl
agreed flowchart of the process is followed by all to ensure consistency. In the second stage (Do) trials and experiments are run on the standardized best practice methods. Following this, in the Study stage of the SDSA Cycle, the efficacy of the best practice methods are evaluated through an analysis of key parameters. Finally, in the Act stage of the cycle, managers attempt to âformalizeâ the best practice methods that have stood the scrutiny of trials. But in order to materialize and enhance the best practice methods thus formalized the management will have to follow through the PDSA cycle.
The PDSA cycle stands for Plan-Do-Study-Act. Its purpose is to aid the management in âimproving and innovating performanceâ. In the planning stage, the formalized best practice methods developed using the SDSA cycle are reviewed. An attempt is made to ameliorate the methods formalized during the SDSA cycle. Often it results in making small adjustments to the flowchart from the SDSA cycle. Thus process improvement plans are laid out by the team. The three possible methods are: 1. Statistical analysis of key indicator data; 2. Benchmarking the process against another organizationâs process; 3. Utilizing a list of tried and proven improvement concepts. The next step in PDSA is Do, whereby the outcomes of the plan are measured. In the subsequent stage (Study) the measurements thus obtained are studied from key indicators. Finally, in the Act stage, requisite corrective actions are taken.
Reference:
Edwards, Demingâs Theory of Management, Chapter 2, Part One, Foundations of Quality Management, pp. 38-50.
Demingâs 14 Points for Leadership in the Western World is a
well rounded guide for achieving excellence in management. The 14 points or guidelines are applicable to any domain or industry. One of the key insights offered by Deming is how a high level of quality (or even a zero-defect production record) does not pre-empt the scope for improvement. The very first point talks about creating a âconstancy of purpose toward improvement of product and serviceâ. This indicates how improvement is an ongoing engagement that is detached from prevailing production quality. Deming makes clear that âdefect detectionâ and âdefect preventionâ are preludes to the continuous improvement process. An optimal defect detection system would not operate on the misplaced assumption that increasing the quantity of tests (mass inspection) would automatically âdecrease the variability of the quality characteristics of products and services.â Likewise, a robust defect prevention .
- Research Methods essays
- Experiment essays
- Hypothesis essays
- Observation essays
- Qualitative Research essays
- Theory essays
- Explorer essays
- Accident essays
- Awareness essays
- Benefits of Volunteering essays
- Challenges essays
- Childhood Memories essays
- Decision essays
- Driving essays
- Event essays
- Excellence essays
- Expectations essays
- Failure essays
- Farewell essays
- Flight essays
- Gift essays
- Growing Up essays
- Ignorance essays
- Improve essays
- Incident essays
- Knowledge essays
- Luck essays
- Memories essays
- Mistake essays
- Obstacles essays
- Overcoming Challenges essays
- Party essays
- Peace Corps essays
- Personal Experience essays
- Problems essays
- Sacrifices essays
- Struggle essays
- Success essays
- Trust essays
- Vacation essays
- Visit essays
- Volunteering essays
- Agriculture essays
- Albert einstein essays
- Animals essays
- Archaeology essays
- Bear essays
- Biology essays
- Birds essays
- Butterfly essays