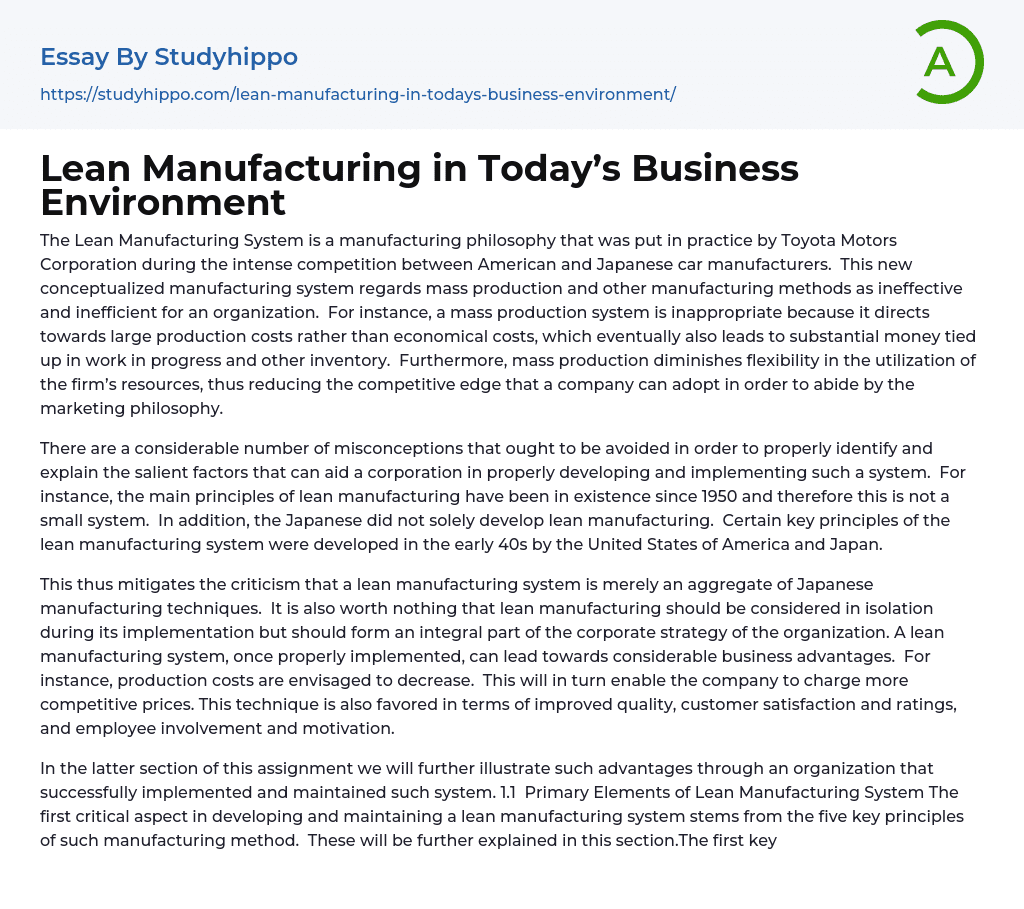
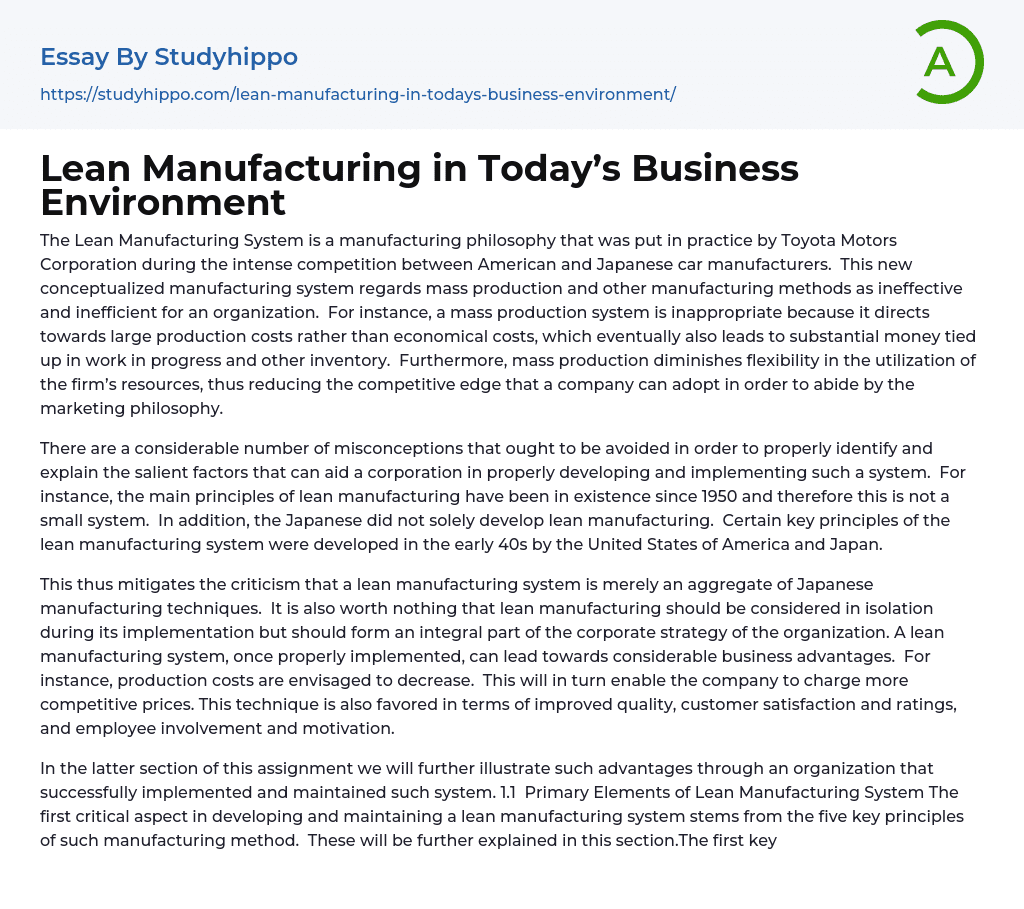
Lean Manufacturing in Today’s Business Environment Essay Example
The Lean Manufacturing System was implemented by Toyota Motors Corporation as a response to the intense competition between American and Japanese car manufacturers. This manufacturing philosophy considers mass production and other methods as ineffective and inefficient. An example of this inefficiency is that mass production leads to high production costs rather than economical costs, resulting in significant money tied up in work in progress and inventory. Additionally, mass production limits the flexibility of a company's resources, reducing its competitive advantage in the market.
There are numerous misconceptions that need to be avoided when identifying and explaining the factors that aid in the development and implementation of a corporation's system. The main principles of lean manufacturing have been around since 1950, so it is not a small system. It is also important to note that lean manufacturing was not solely developed by
...the Japanese. The United States and Japan developed certain key principles in the early 40s, meaning it is not just a combination of Japanese techniques. Additionally, lean manufacturing should not be implemented in isolation but should be integrated into the corporate strategy. Implementing a lean manufacturing system can bring significant business advantages such as decreased production costs, enabling the company to offer more competitive prices. This technique also improves quality, customer satisfaction and ratings, and employee involvement and motivation.
This section of the assignment will showcase the benefits of implementing and maintaining a lean manufacturing system through the example of a successful organization. We will delve into the primary elements of this system, starting with the five key principles that form its foundation. These principles will be further explored in this section.
The first principle is manufacturin
flow, which involves the physical design and layout of the manufacturing process. It encompasses various factors such as evaluating product quality, determining Kanban sizes, creating process maps, designing cell layouts, implementing one-piece flow, standardizing work procedures, calculating Takt time, balancing workloads, and analyzing production processes and volumes.
Next is the organizing element, which focuses on important factors within the organizational structure and organizing function. This includes establishing effective lines of communication, defining roles and responsibilities for both staff and management, and providing necessary training. The lean manufacturing system requires the formation of multidisciplinary teams dedicated to specific products, as well as cross-training employees to ensure versatile skill sets. Training programs that promote awareness and understanding of lean principles among staff are crucial at the beginning of implementing this system. Additionally, the development of lean managers is emphasized during this stage.The lean manufacturing system emphasizes the importance of process control in the development of a manufacturing enterprise. It aims to achieve an optimal production process through effective control systems. Key factors such as productive maintenance, 5S housekeeping, SPC, line stop, visual control, graphical work instructions, single minute exchange of dies, Poka-yoke, and continuous improvement are considered in the control system.
Performance measurement is a vital aspect to consider when developing a lean manufacturing system. It involves controlling staff performance based on set standards and criteria. This includes factors like productivity, resource utilization, inventory turnover, cost efficiency, quality, and timely delivery of goods.
Logistics is another important component of a lean manufacturing system. It focuses on policies, procedures, and methods that ensure an efficient flow of materials. This involves aligning with suppliers and clients, level loading, mix model production, forward
planning, and other operational rules.
The Kanban pull system is commonly used in the logistics stage of a lean manufacturing system.
Planning is a critical element of implementing a Lean Manufacturing Program. It should be carefully done to identify core areas and necessary changes. There are specific areas to consider during analysis and implementation of a lean manufacturing system, which will be explained below.The company's mission statement and corporate plan, which prioritize the customer and align with the current system, are essential factors to consider. Short-term plans must be implemented to facilitate the execution of long-term plans.
Create a Quality Assurance Department that focuses on ensuring the appropriate quality of manufactured and delivered products to clients. There are three main techniques in the quality assurance program. The Statistical Process Control system tracks process variability, using periodic measurements to ensure the process stays within control limits. Any factors outside these limits are investigated and corrected to maintain the desired standard and consistency. The Poka-Yoke technique acts as a foolproof mechanism by identifying defects at the source, preventing defective products from entering the next process. This technique reduces the probability of defects, minimizes waste and inspection time. Implementation involves ten steps: identifying the goals, defects to be removed, analyzing past trends for similar solutions, locating the defect, understanding current operations, identifying the source of defects, determining the purpose of the device, creating an effective mistake-proofing device to mitigate the issue.The text below explores the elaboration and examination of a device for its effectiveness, as well as the implementation and evaluation of the device's results. Typically, business organizations utilize both methods together as they complement each other, ultimately enhancing the quality
aspect. The latter method, known as visual control, is primarily an observational approach. To identify non-value-added activities, a production flow diagram is created. Additionally, value stream mapping helps ensure quality by focusing on the firm's operations, such as identifying issues like poor layout, large batches, and uneven workload. Visual control is typically conducted alongside the 5-S system.
This text describes a control system called the 5-S system, which consists of five stages: sort, straighten, shine, standardize, and sustain. In the sort stage, unnecessary items are identified and removed from the system. The straighten stage involves organizing and labeling items using lines, labels, and signs. The shine stage involves cleaning and inspecting to prevent dirt and contamination. The standardize stage sets guidelines for the 5-S conditions and communicates them effectively. Finally, the sustain stage ensures continuous adherence to the standards through training and communication.Visual standards and measures are commonly used to aid staff comprehension. The installation of the 5S system can decrease machine breakdowns and improve safety and product quality. The 5-S system and visual control method are important for the effective development, implementation, and maintenance of a lean manufacturing program. The Kaizen event focuses on reducing setup time through techniques like the Single Minute Exchange of Dies. This improves quality, efficiency, flexibility, resource utilization, and reduces lead-time and process variability. The Kaizen Event is vital for implementing a lean manufacturing system and enhances the Just in Time System. Short cycle time is crucial for a lean manufacturing program as it improves client lead-time and manufacturing work in progress.
The lean manufacturing system focuses on various causes of high work in progress. These include suppliers of raw materials,
long set up time, production planned in large batches, frequent changes in shop orders, recurring shortages of component parts, sections functioning at different shifts, lack of specialized employees, slow material flow within the organization leading to bottlenecks, and not meeting the tastes of targeted customers. To ensure proper development and implementation of a lean manufacturing program, remedial actions can be taken such as decreasing excessive inventory and improving inventory turnover. This involves examining the cause and root of the work in progress problem. A Just in Time System can be adopted under a lean management system to effectively mitigate this problem for work in progress, raw material, and finished goods.Indeed, Just in Time is an integral part of the lean manufacturing system. This strategy involves frequent deliveries from suppliers in smaller quantities. Just in Time is often connected with Total Quality Management and is founded on the concept of getting it right the first time. The main objective of this technique is to have the correct inventory, delivered at the right time, in the right volume, and at the right location. It should be noted that Just in Time can be applied not only to raw materials but also to finished products, affecting the previous point mentioned. Another important goal of a Just in Time System is achieving greater alignment between customer preferences and demand rate. This is accomplished by adopting a flexible production approach and manufacturing products in line with customer demands and desired quantity. Minimizing lead-time and emphasizing quality are also significant objectives of the just in time system. Ultimately, it is crucial for management to understand the key principles of a Just
in Time System to ensure successful design and implementation of lean manufacturing.
It is crucial to define and communicate standard operations to all staff involved. Additionally, multi-process handling employees are required. Thus, clear communication channels and proper training for staff are important. A Just in Time System necessitates the use of a flow production technique, specifically a one-piece flow where machines are arranged in the order of processes for easy movement of materials and goods. This aspect of Just in Time is linked to lean manufacturing's focus on inventory reduction. To achieve a low cycle time, another strategy is to minimize non-value added waiting time. The visual control method mentioned in sub-section 1.2.1 can help identify such activities. Differentiating between production lot size and transfer lot size is crucial to reduce these non-value added activities, with a particular emphasis on reducing the transfer lot size. Implementing a pull production control system, such as the Kanban system, supports the Just in Time System, an integral element as already mentioned.
The client has a significant role in the manufacturing process in this system. It is considered real-time and aligned with the target market. The pull system is self-correcting and follows the customer's demand for production and delivery instructions. Production only occurs when necessary and requested by the client. The system is also self-regulating, authorizing production based on actual consumption of goods. The Kanban system includes features such as low inventory, reduced cycle time and setup times, improved quality, and increased collaboration among staff. It is important to have a uniform demand, which is often beyond the organization's control. These features align with those observed in the Just-in-Time System.The pull
system of inventory control assists in achieving a cellular manufacturing system, which is crucial in lean manufacturing. The successful implementation of a cellular manufacturing system requires flexibility in production design, cost-effectiveness, and operation in small lot sizes. These features are present in the pull system, demonstrating its contribution to the cellular manufacturing system. The synchronization of production is another important strategy in lean manufacturing. Overbuilding on items should be eliminated and production should be evenly spread throughout the calendar year. The cellular manufacturing system plays a crucial role in ensuring synchronized production. Additionally, a single-piece flow system integrated with pull inventory control is essential in the company's lean manufacturing program at this stage.The fourth strategy in this phase focuses on scheduling a steady and balanced workflow. It emphasizes the importance of frequent small orders and ensuring a proper flow of production by addressing idle time caused by machine breakdowns. Consequently, an improved maintenance policy for all capital equipment is crucial.
Another strategy, called value stream, aims to reduce variability in the organization's operations. This technique requires the implementation of the Just in Time System, which has been explained in detail previously. To minimize or eliminate variability, it is necessary to concentrate on both internal and external factors. These factors include equipment downtime, late deliveries from raw material suppliers, long setups, production lot size, and lot size from suppliers. Nonetheless, it is acknowledged that complete elimination of variability may not be feasible in certain industries.
In such instances, management should find ways to adapt and alleviate the negative effects it entails. However, due to their significance, the important factors mentioned earlier will be reiterated with the addition of
new ones to provide a comprehensive understanding of these critical elements. It is crucial to select a change agent who will lead the transformation journey and be supported by a specialized team. After choosing the production undergoing transformation and setting short-term goals, communication regarding the lean manufacturing vision should begin. This should be followed by the implementation of all necessary systems discussed previously. The roles and responsibilities of operational management and staff should be clearly assigned to ensure defined and met monitoring standards. To minimize resistance to change, management should provide positive feedback on employees' progress in implementing the lean manufacturing system.
- Value Chain essays
- Airbus essays
- Delta Air Lines essays
- Qantas essays
- Factory essays
- Material essays
- Production And Manufacturing essays
- Alarm clock essays
- Accounting essays
- Andrew Carnegie essays
- Automation essays
- Business Cycle essays
- Business Intelligence essays
- Business Model essays
- Business Operations essays
- Business Software essays
- Cooperation essays
- Cooperative essays
- Corporate Social Responsibility essays
- Corporation essays
- Customer Relationship Management essays
- Family Business essays
- Franchising essays
- Harvard Business School essays
- Harvard university essays
- Human Resource Management essays
- Infrastructure essays
- Inventory essays
- Logistics essays
- Management essays
- Manufacturing essays
- Market essays
- Marketing essays
- Multinational Corporation essays
- News Media essays
- Online Shopping essays
- Quality Assurance essays
- Richard Branson essays
- Sales essays
- Selling essays
- Shopping Mall essays
- Small Business essays
- Starting a Business essays
- Stock essays
- Strategy essays
- Structure essays
- Trade Union essays
- Waste essays