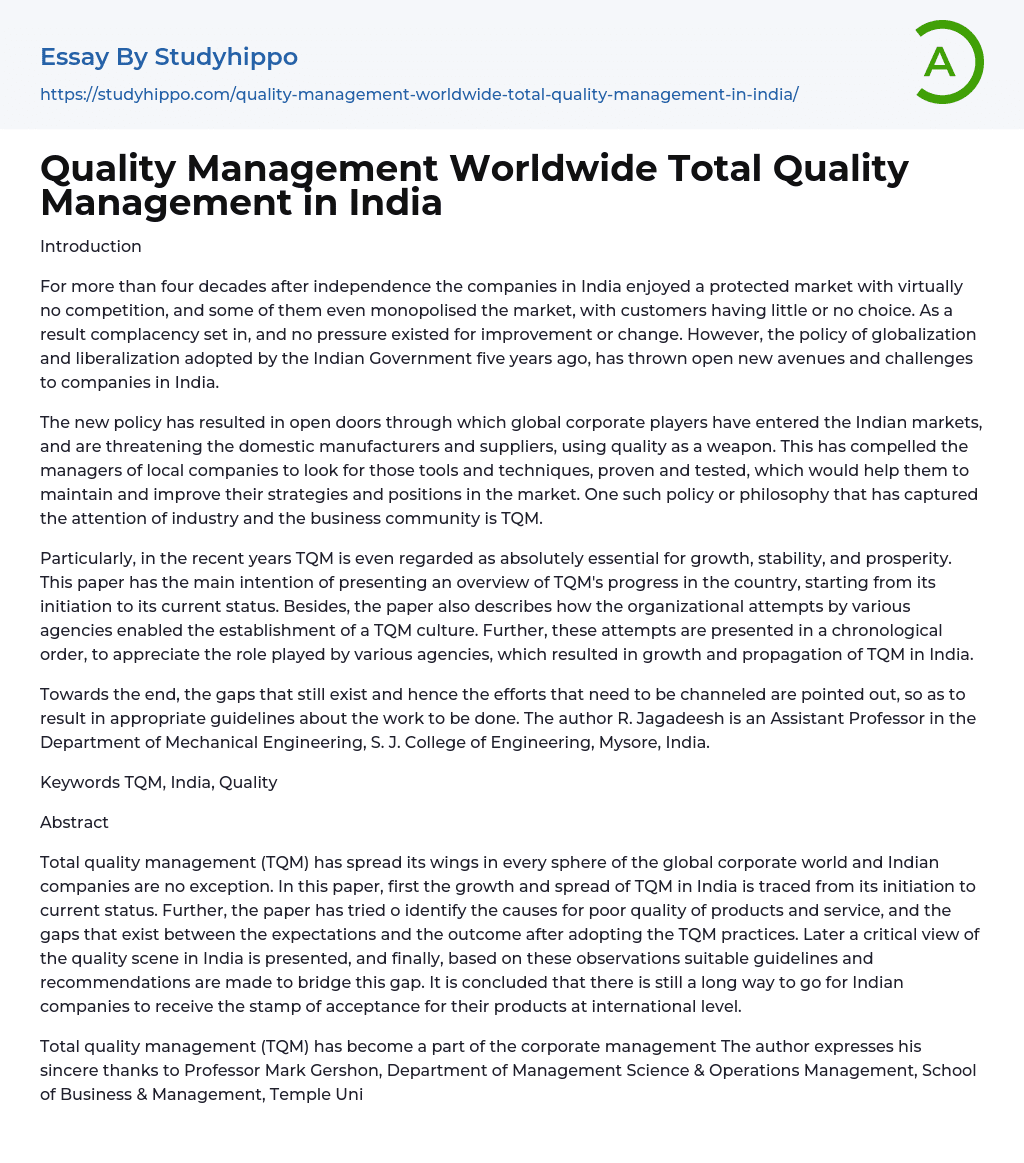
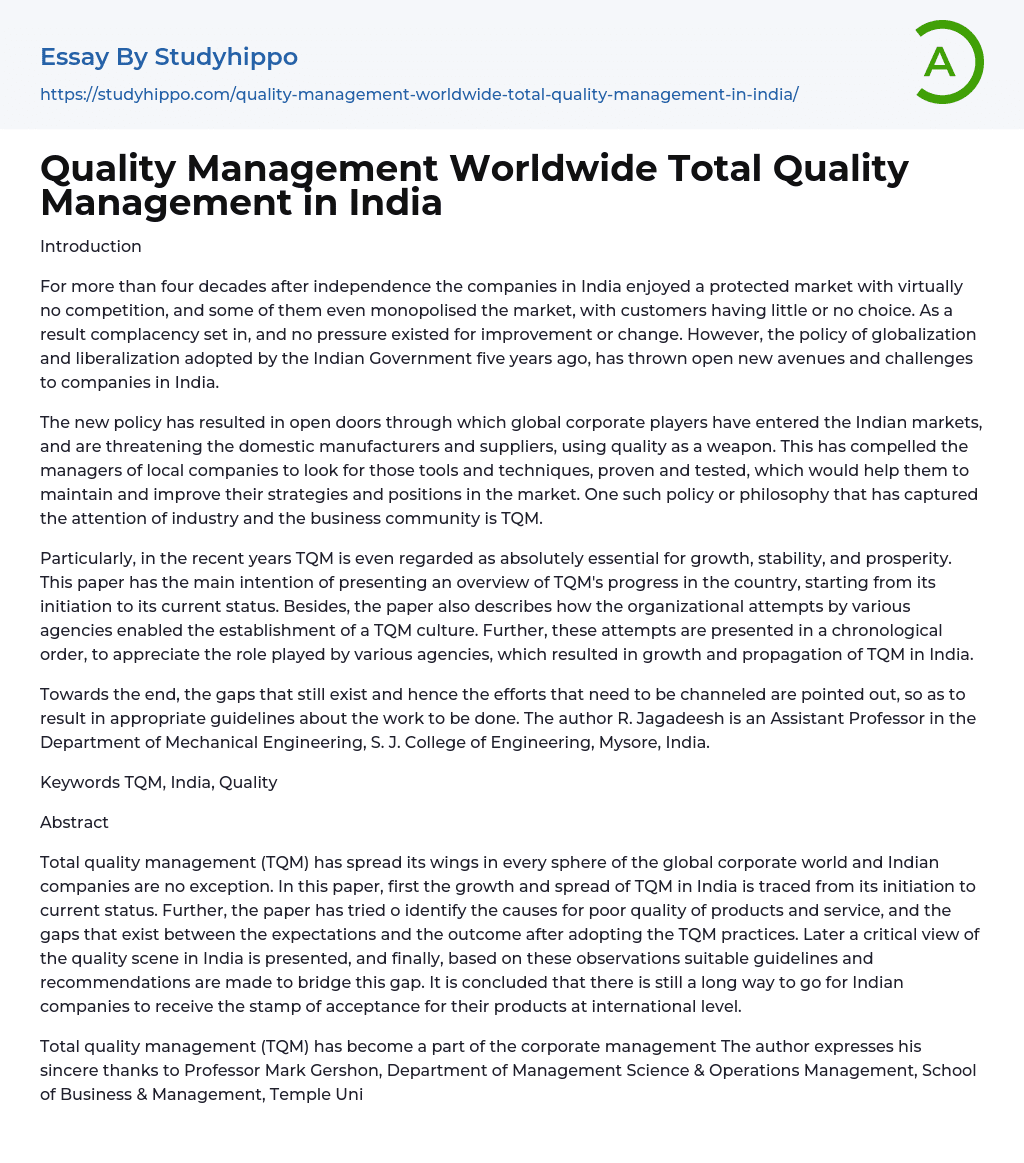
Quality Management Worldwide Total Quality Management in India Essay Example
Introduction
During the period after India gained independence, companies in the country enjoyed a stable market environment with minimal competition. Some companies even had monopolies, which meant customers had limited or no other options.
Due to complacency, there was no motivation for improvement or change. Nevertheless, the Indian Government's policy of globalization and liberalization has presented new prospects and difficulties for companies in India. This policy has enabled international corporations to enter the Indian markets, posing a risk to domestic manufacturers and suppliers by using quality as a competitive edge. Consequently, local company managers have been encouraged to search for established tools and techniques that can assist them in maintaining and improving their market strategies and positions. TQM is one specific policy or philosophy that has gained attention from the industry and business community.
T
...he significance of TQM (Total Quality Management) has significantly risen in recent years due to its vital role in attaining growth, stability, and prosperity. This article offers an overview of the development of TQM in the country, from its beginning to its current state. It also examines how different organizations have contributed to nurturing a culture of TQM. By presenting these endeavors in chronological order, we recognize the contributions made by various agencies in India's progress and promotion of TQM.
Towards the end, the author R. Jagadeesh, an Assistant Professor in the Department of Mechanical Engineering, S.J, points out the remaining gaps and the efforts that need to be channeled to establish appropriate guidelines for the work that needs to be done.
College of Engineering, Mysore, India. Keywords TQM, India, Quality
Abstract
This paper explores the implementation of Total Quality Management (TQM) in
companies worldwide and specifically in India. It examines the adoption and growth of TQM in India, investigates the causes behind insufficient quality of products and services, identifies discrepancies between expectations and outcomes in implementing TQM practices, critically evaluates the quality situation in India, and provides recommendations to tackle these challenges.
The text emphasizes the importance of Indian companies enhancing their worldwide reputation for product quality. It underscores that total quality management (TQM) is considered essential in both international and domestic corporate management. The author expresses gratitude to Professor Mark Gershon from Temple University for reviewing the paper and offering valuable suggestions that enhanced its quality. While TQM was previously disregarded as mere jargon and a temporary trend, it is now recognized as indispensable for achieving success and facilitating growth.
The increasing number of publications indicates the growing interest in TQM. Ahire et al. (1995) conducted a literature review on TQM, analyzing 226 articles published in 44 management journals between 1970 and 1993. Various studies have documented success stories, such as those by Longenecker and Scazzera (1993) and Sterman et al. (1997). These success stories have inspired Indian companies to implement TQM programs. The ISO 9000 certification, which is currently a priority for many companies, has provided a strong foundation for launching TQM effectively.
Various compelling reasons exist for adopting Total Quality Management (TQM), including pressure resulting from decreased profits, the inability to penetrate new markets, intensifying competition, and the demands of quality-conscious customers for improved products and services.
Status of Quality
In India, there is a long tradition of achieving high standards in various fields. The country's rich cultural heritage is evident in architectural wonders like the "Taj Mahal" and
the "Konark temple," which highlight an emphasis on quality. Additionally, throughout history, products such as jewelry, textiles, artistic items, and ornamental articles have consistently demonstrated exceptional quality and have been extensively traded with other nations. Even during colonial rule, engineering industries in India were renowned for their commitment to quality.
According to Piramal (1997), conglomerates like Tata, Birla, Godrej, and Sarabhai have played a major role in initiating and managing various industries in India. These families are well-known for their trustworthiness and production of high-quality products. However, Agrawal (1993) argues that there has been limited progress in improving the quality of goods and services produced in India since gaining independence. The protected business environment has led to the loss of positive attributes within the Indian industry and the emergence of weaknesses. These weaknesses include a lack of trust and credibility within the working system, a lack of dedication to achieving goals, disregard for rules and norms, low-quality supplies and components, failure to appreciate the value of time, prioritization of short-term benefits over long-term objectives, politicization of labor unions, absence of accountability and management commitment. Additionally, there is an inadequate national quality policy along with insufficient economic resources and indigenous technology. Insufficient infrastructure coupled with a preference for quantity over quality further contributes to these weaknesses. A scarcity of teamwork within organizations leads to cartel formation resulting in a seller's market. Furthermore, the decrease in significance placed on quality can be attributed to the absence of consumerism and governmental regulations across all areas.Therefore, due to prioritizing quick financial gains rather than maintaining high standards, companies restricted Indian products solely for the domestic market and failed to compete
globally.
Additionally, the aforementioned factors proved to be significant obstacles hindering progress. Despite having abundant resources and a skilled scientific and technical workforce, India was unable to manufacture world-class products that met international market standards.
The Advancement of TQM in India
The implementation of TQM initiatives began in the early 1980s by the Confederation of Indian Industries (CII), as they aimed to raise awareness about quality standards within Indian industries. The efforts made by CII are well-documented in publications such as Deccan Herald Advertising Feature (1993) and The Standards Engineer (1996). Quality circles were introduced in India in 1982, pioneered by Bharat Electronics Limited in Bangalore and Bharat Heavy Electricals Limited in Trichy. In 1986, the CII (previously known as CEI - Confederation of Engineering Industries) invited Professor Ishikawa to India to provide insights on quality to industry professionals. Subsequently, in 1987, a dedicated TQM division was established by CII.
The establishment of this division is credited to 21 companies who joined together to support the cause of Total Quality Management (TQM). These companies pooled their resources and made a commitment to embark on the TQM journey. The chief executives of these companies formed the National Committee on Quality and declared quality month as an annual event. Additionally, the Confederation of Indian Industry (CII) introduced the first newsletter on quality. In 1987 and 1988, the CII invited the Juran Institute to India to conduct three training workshops. Furthermore, in 1989, a team from India attended the Deming Seminar in London. The CII also organized study teams to visit Japan and the USA to observe quality practices.
During the 1990s, the CII mainly concentrated on training. In February 1991, they partnered
with an Indian company to obtain India's initial ISO 9000 certification. Additionally, in May 1992, the CII played a vital role in commencing the National Quality Campaign led by the Prime Minister of India. This period was critical for the nation as it embarked on globalization and liberalization, resulting in substantial alterations within business and industry. Consequently, there arose a renewed focus on quality, productivity, and competitiveness.
The CII has been organizing The Quality Summit every year since 1993, offering a forum for business leaders and high-level managers to connect, gain knowledge, contribute through sharing experiences, and hear from industry experts. In New Delhi, the National Productivity Council (NPC) has set up a TQM and Benchmarking Division that provides TQM implementation services such as modular training programs and consultancy services. In 1996, the Indian Government declared the formation of the Quality Council of India (QCI), with half of the initial capital contributed by the Industry Ministry.
The national agency for quality certification will be established with a seed capital of 50 million. The corporate sector will also contribute to the funding. This agency is in accordance with the World Trade Organization (WTO) agreements, which require member countries to trade only in certified products within two years. The corporate sector has been requesting the establishment of a recognized quality council to reduce dependency on expensive foreign agencies for certification and save foreign exchange. The QCI will be responsible for monitoring and administering the National Quality Campaign and ensuring the efficient functioning of the National Information and Enquiry Services.
The introduction of economic reforms in 1992 has greatly improved the economic scene after the liberalization process. This led to a
new era of progress and prosperity, as reported in Yojana (1997). The agriculture and allied sectors saw a real GDP growth rate of 6.8%, while the industry and services sectors experienced growth rates of 7.0% and 7.3% respectively. The Eighth Five Year Plan (EFYP) (1992-97) concluded with an average growth rate of 6%.
The average growth rate of 5 percent per annum is comparable to the target rate of 5.6 percent for the EFYP and the actual achievement of 6 percent in the Seventh Five Year Plan. This is the highest average growth rate achieved since 1951. The sectoral average growth rates for the period 1992-97 are: Agriculture and allied sectors at 4 percent, and Industry at 7 percent.
The growth rates in agriculture and services were 8% and 9. 2% respectively. The export growth rate in 1996-97 was 4. 1%. Foreign direct investment reached US $2,696 million in the same period. These figures highlight the positive impact of globalization and liberalization on the economy, indicating promising prospects for the future.
While various advancements can be observed on a larger scale, Indian companies have made individual efforts to enhance their product quality and overall performance using TQM practices. One case study by Gupta and Sagar (1993) illustrates the implementation of total quality control in an engineering company through extensive use of personal computers. The study highlights the company's successful resolution of several quality-related issues, including high rejection rates, slow inspection rates, measurement errors, interpretation inconsistencies, cumbersome data storage and retrieval, inflexible inspection schedules, lack of adaptability to changing environments, and inadequate adjustment of quality plans for different batch sizes. The company effectively enhanced its problem-solving capacity through quality
circles and implemented quality databases at each stage. The utilization of comprehensive information systems provided better guidance to personnel, leading to improved decision-making processes.
India's business sector has been successful due to the systematic application of Total Quality Management (TQM). Business Today (1995) provides exclusive coverage on the quality status of Indian companies, highlighting market leaders and corporate giants. The report includes detailed information on esteemed Indian companies such as Mukand, BPL, Arvind, IFB, ABB, HDFC, Amex, Hindustan Lever, Ranbaxy, Indal, Gujarat Ambuja, Vysya Bank, Oberoi Hotels and Thermax. These companies have prioritized quality in their planning operations and marketing strategies to establish a unique position in the market. Pati and Reis (1996) further confirm that India is emerging as a leading economy in the new world economic order due to increased awareness of quality.
India's export earnings in the fiscal year 1994-95 witnessed a notable surge, reaching US$26 billion. This represents an 18.27% increase compared to the previous year's earnings of US$22.17 billion. The rise reflects the positive perception of Indian products and services among global customers. Moreover, there has been a shift from import substitution to prioritizing the growth of an export-oriented economy.
Other significant observations include:
- Indian businesses are pursuing paths of superior quality and high productivity.
- There is a conscious increase in quality-focused consumerism and growing competition.
- Industries are expanding their domestic market share and exploring global markets.
-
The number of ISO 9000 certified companies in India has significantly increased.
The Pati and Reis
(1996) survey provides further insights into quality practices in India.
The survey used a five-point Likert interval to measure perception, where points 1 (very high), 2 (high), 3 (medium), 4 (low), and 5 (very low) describe the current degree of quality practices.
The critical success factors contributing to quality and their average scores based on the survey are as follows:
- Role of top management and quality policy: 3.3
- Role of quality department/personnel: 3.14
- Training: 3.69
Product/service design, supplier quality management, process management and operating procedures, quality data reporting, and employee relations were all rated. The ratings for product/service design was 2.91, supplier quality management was 2.86, process management and operating procedures was 2.74, quality data reporting was 2.72, and employee relations received a rating of 2.
According to a survey, the manufacturing sector in India acknowledges the significance of quality and has taken steps to enhance product quality. However, the service sector, which is mainly government-owned and operated, lags behind the manufacturing sector in terms of quality. Indian companies are increasingly understanding the importance of "customer focus" for Total Quality Management (TQM). Jain (1996) states that companies now prioritize collecting customer feedback to personalize products and meet their needs. They employ various methods like benchmarking, customer meetings, and market research to gather feedback on their product range and after-sales service. Two specific cases exemplify these efforts.
Escorts Limited, an automobile manufacturing company, changed the delivery route based on customer
and dealer feedback in order to ensure safe and quick delivery. Additionally, J. K. Synthetics focused on standardizing quality parameters and implementing after-sales service, following feedback from customer meetings. The sales of J. K. Synthetics increased significantly from 220 tonnes in the first quarter of 1995 to 632 tonnes in the last quarter of the same year, representing a three-fold growth compared to the previous value. According to a report published in Business Today (1998), Yoshikazu Tsuda, a counselor at JUSE (Union of Japanese Scientists and Engineers), is guiding some Indian companies in their pursuit of total quality.
Some Indian companies, such as Sona Steering, Jai Bharat Maruti, GKN Invel, Asahi Float Glass, Brakes India, Lucas TVS, India Pistons, and India Piston Rings, practice the sixsigma technique which is considered a classic TQM technique. The Economic Times (1998) mentions that Wipro, a well-known name in the information technology field, is among these companies. Sridharan (1998a) reports a notable achievement by an Indian company called Sundaram Fasteners, located near Chennai, India. This company received the Best of Best Vendors Award for two consecutive years in 1996 and 1997 for supplying metal radiator caps to General Motors, USA. The award was given due to the company's consistent zero defects rate, 100 percent reliability in delivery schedules, and lowest price.
According to an interview with the managing director of Asea Brown Boveri Ltd, one of India's successful multi-national companies, the company is the only supplier from India to General Motors out of its 3,000 global suppliers (Premchander, 1996). Sundaram Clayton, an Indian company, has achieved a historic feat by winning the esteemed Deming Prize for Overseas Companies for effectively
implementing TQM. This success is attributed to their deployment of TQM tools, techniques, and systems, which transformed their employees into quality practitioners (Sridharan, 1998b). The company has also improved their time to market by 38% and gained corporate credibility by 22%.
A critical assessment of the Indian quality scene requires a comparative global examination of the developments concerning the quality of products and services. This approach allows for an evaluation of the progress made in enhancing quality. The World Competitiveness Report conducted a survey in 1994, which ranked products and services from 41 countries. The results, summarized in Skaria (1995), reveal that the quality of Indian products and services is unsatisfactory. India's rank, in relation to various quality parameters, is as follows (denoted by the rank out of 41 followed by the respective parameter):
39 ± price to quality; . 38 ± practice of TQM; . 40 ± customer orientation; . 28 ± product liability; .
39 ± time to innovate; The report indicated that globally, Indian products and services are not satisfactory and have a negative reputation. This is concerning for corporate managers, especially those seeking new markets and partnerships with foreign collaborators. A commonly mentioned excuse for poor quality in India is the absence of consumer pressure. Many managers believe that unless customers are aware of their right to demand high quality and actively encourage companies to invest in quality, they will continue to receive subpar products.
While the adoption of TQM (Total Quality Management) practices in India has been slow, other Asian countries have firmly embraced it. According to a cover feature on "Quality in Asia" published in World Executive Digest (1996), as Asia faces the
challenge of globalization, more companies are seeking ISO 9000 certification and implementing TQM. Hong Kong, Taiwan, Malaysia, Singapore, and China are actively adopting total quality practices to succeed in global markets. The Economic Intelligence Unit (1996) conducted a survey on quality practices among companies in Hong Kong and found that many of the TQM issues identified in other regions were also prevalent there. Despite this, the growth of TQM throughout Asia has led to the development of new approaches in the region.
The text suggests that India needs to closely monitor developments in the Asiatic region because several countries have successfully implemented TQM principles, improving their output quality and attracting more foreign investment. This could potentially limit India's share in the global market. Despite the hype surrounding ISO 9000 certification, quality is still not a major strength of Indian products. Indian companies' managers have much to learn and implement in order to build an image based on quality. Philip Crosby, as reported in The Times of India (1997), stated that complacency is a major problem within the Indian management system. The managers of Indian industries should take this statement seriously.
According to James Harrington, an expert in quality, India has companies grouped into four categories: poor performers, good performers, better performers, and outstanding performers. Harrington notes that poor performers would go bankrupt in other parts of the world, while good performers would likely follow suit. However, better performers have a chance of surviving and outstanding performers are expected to thrive in the twenty-first century. This suggests that India still has room for low-quality products and underperforming companies, which should be addressed promptly. Sukumar points out that Total
Quality Management (TQM) continues to confuse corporate India, as evidenced by the various interpretations held by individuals within the industry. The Sixth Quality Summit organized by the CII in New Delhi revealed that TQM can mean different things depending on an individual's perspective, political stance, and paradigms.
During the summit, multiple definitions of TQM were presented by the speakers, indicating a lack of consensus within the corporate sector. This lack of agreement could hinder the implementation of TQM. In a separate survey conducted by Arun et al. (1998) on ISO certified companies, interesting observations were made regarding TQM implementation. Out of the 17 surveyed companies, managers from seven expressed belief in TQM but admitted to not knowing how to implement it. The survey also revealed that the significance of long-term supplier relationships, a crucial factor for successful TQM implementation, had not yet been acknowledged for achieving total quality.
Other obstacles that hinder the implementation of TQM include reliance on traditional incentives, numerical targets, performance ratings, slogans for productivity improvement, and inadequate training for each individual's job. Based on the survey, it is concluded that if these factors are not addressed, a company may maintain ISO certification but not be recognized as a TQM company.
Comments and Conclusion
The various surveys conducted independently by researchers and business publications have shown that there is an increasing awareness of the importance of product and service quality in India. With intense competition focusing on quality, Indian industries and businesspeople are actively seeking to enhance product quality through TQM. Numerous organizations, both private and government, are actively promoting TQM through various training and educational programs.
TQM has become an essential element for achieving success and
is now ingrained in the "mission and vision" of the Indian corporate sector. Nevertheless, it is evident that the key factors for quality to thrive in India include a robust consumer movement, a dedicated commitment from the corporate sector to prioritize quality, and the rigorous implementation of standards by regulatory bodies and authorities.
Indian companies should avoid grading their products with labels such as "export quality," "first grade," "seconds," and "import rejects" in order to maintain consistent quality across all products. They should serve as a role model by consistently adhering to high quality performance and output before expecting others to do the same. While Total Quality Management (TQM) has helped Indian companies improve their product and service quality, the global market demands even higher levels of quality for recognition and acceptance. Therefore, Indian companies need to continue their efforts and strive for quality with more focus. This paper aims to inspire and drive Indian companies in that direction.
References
- Agrawal, S. K. (1993), "ISO 9000 implementation in Indian industry", Proceedings of the Eighth ISME Conference in Mechanical Engineering, New Delhi, India, March, pp. 638-44.
- Ahire, S. L., Landeros, L. and Golhar, D. Y.
(1995), "Total quality management: a literature review and an agenda for future research", Journal of Production and Operations Management, Vol. 4 No. 3, pp. 277-306.
R. , Aruna Kumar and Lokesh Sharma (1998), "Identification of barriers to achieve TQM after obtaining ISO 9000 certification and development of a causal model for TQM", unpublished dissertation, Department of Industrial and Production Engineering, SJ College of Engineering, Mysore, India.
January, p. 152.
98. Deccan Herald Advertising Feature (1993), "Total quality management ± the Indian scene", Monday, 1 November, 1993, p. 8.
Gupta, V. K. and Sagar, R. (1993), "Total quality control using PCs in an engineering company", International Journal of Production Research, Vol. 31 No.
1, pp. 161-73. Jain, S. (1996), TQM ± the leading edge", India Today, 31 March pp. 90-1. Longnecker, C. O. and Scazerra, J.
A. (1993), "Total quality management from theory to practice: a case study", International Journal of Quality & Reliability Management, Vol. 0 No. 5, pp. 24-31.
A. (1996), "Proliferation of TQM in India ± a survey", Proceedings of the Global Conference on Small & Medium Industry and Business, Bangalore, India, January 1996, pp. 209-14.
8 No. 2, pp. 109-21. Skaria, G. (1995), "The total quality imperative", Business Today, 7-21 January, pp. 19-27. Sridharan, R. 1998a), "Total quality limited", Business Today, 2 November, pp.
69-79.
P. and Kofman (1997) examine the unanticipated side effects of successful quality programs and explore the paradox of organizational improvement in their article titled "Unanticipated side effects of successful quality programs: exploring a paradox of organizational improvement" published in Management Science, Volume 43, Issue 4, pages 503-21.
Sukumar, R.
(1998),
"Total quality confusion", Business Today, 7 December, p. 27.
(1996), "How Asia practices TQM", World Executive Digest, November, p. 4.
(1998), "From six-sigma to strategy", 23 March, p. 3. The Standards Engineer (1996), "News and views", Vol. 31 Nos.
1 and 2, April-September, pp. 20-6.
- Genetic Engineering essays
- Bus essays
- Internal Combustion Engine essays
- Hybrid essays
- Electric Car essays
- Invention essays
- Mechanics essays
- Innovation essays
- Telephone essays
- Software Engineering essays
- Automobile essays
- Cycling essays
- Civil engineering essays
- Mechanical Engineering essays
- Bentley essays
- Cloud Computing essays
- Computer Science essays
- Consumer Electronics essays
- Data Analysis essays
- Electronics essays
- engineering essays
- Enterprise Technology essays
- Hardware essays
- Impact of Technology essays
- Information Age essays
- Information Technology essays
- Modern Technology essays
- Operating Systems essays
- people search essays
- Robot essays
- Bangladesh essays
- China essays
- Hong Kong essays
- India essays
- Japan essays
- Kuala Lumpur essays
- Malaysia essays
- Manila essays
- Pakistan essays
- Philippines essays
- Singapore essays
- Vietnam essays
- Vietnamese essays
- Qualities essays
- Board Of Directors essays
- Brand Management essays
- Business Ethics essays
- Business Management essays
- Change Management essays
- Comparative Analysis essays