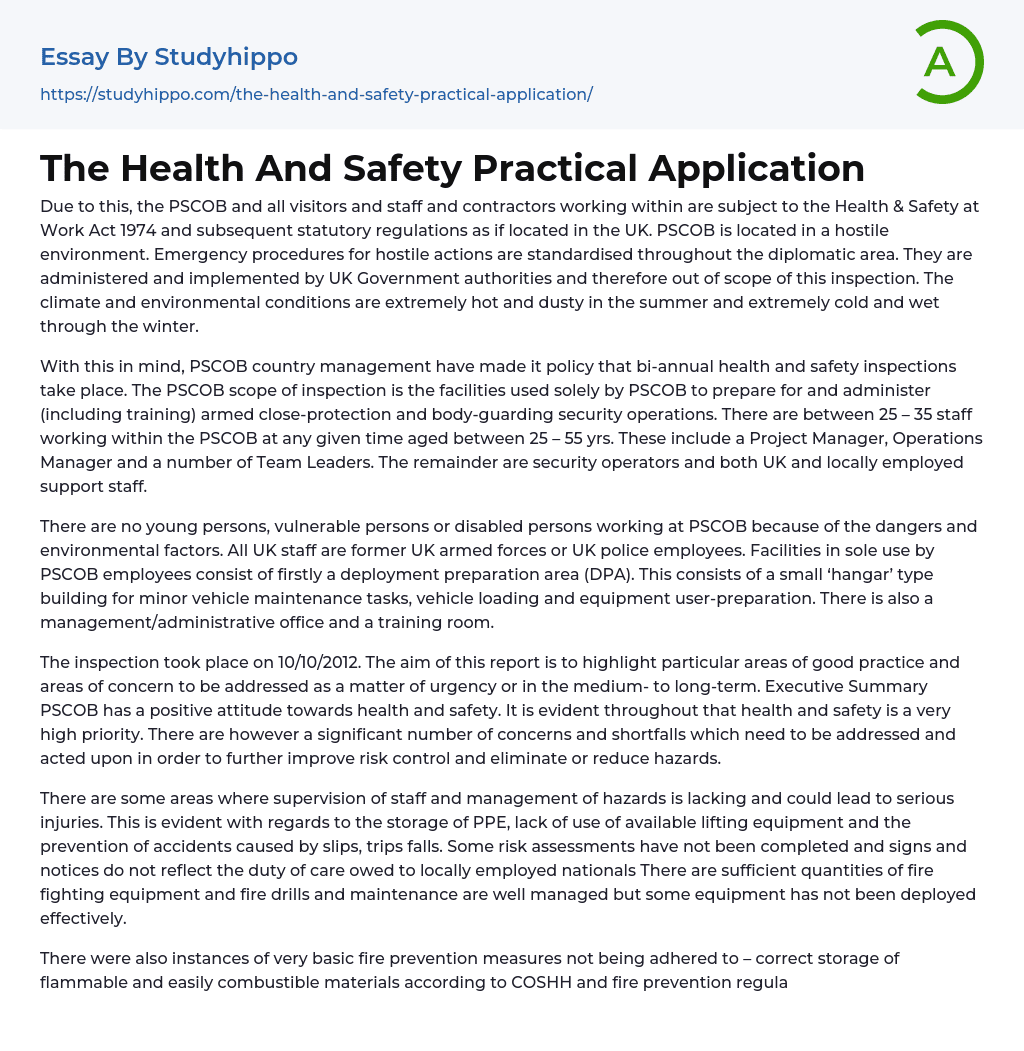
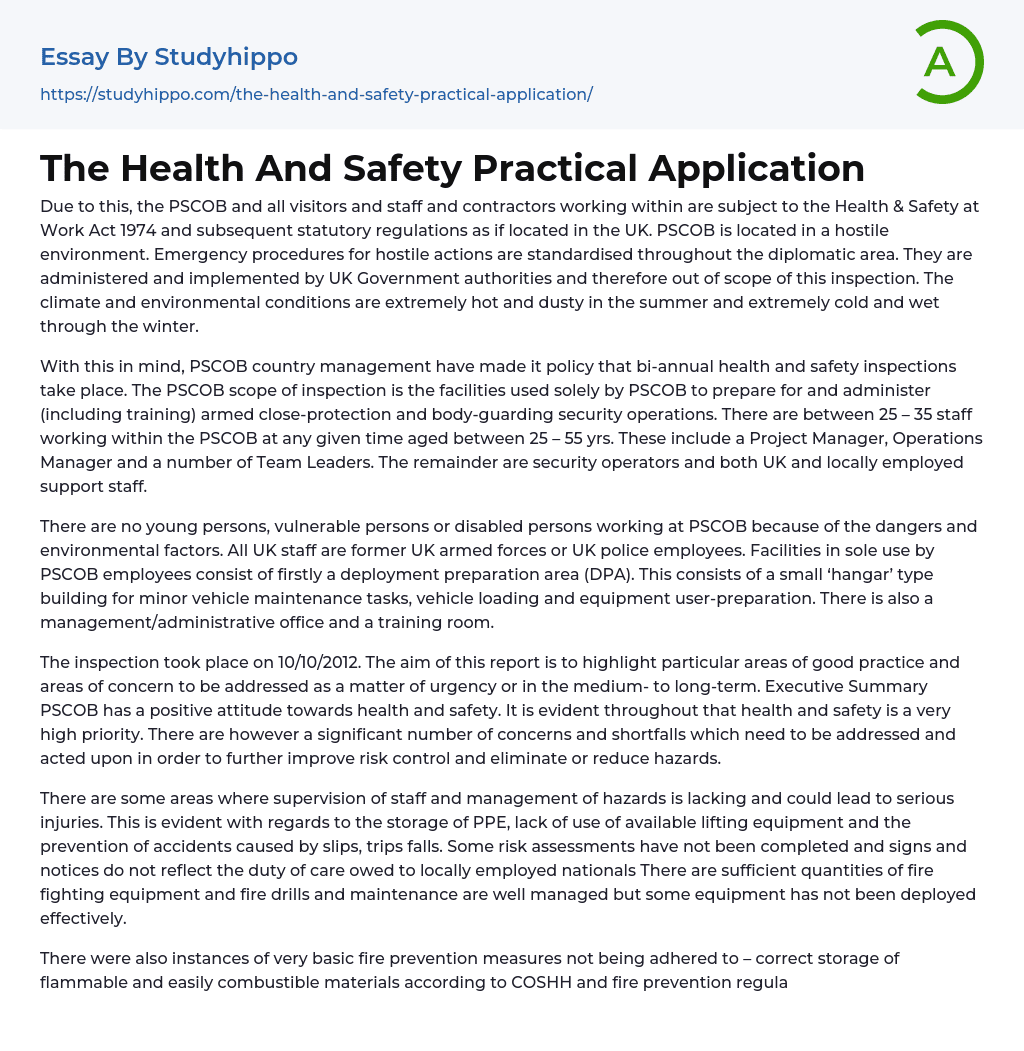
The Health And Safety Practical Application Essay Example
Everyone present in the PSCOB facility, including visitors, employees, and contractors, must adhere to the Health & Safety at Work Act 1974 along with its subsequent regulations as if they were located in the UK. It's crucial to understand that this site is situated in a risky area where procedures against hostility are frequently activated within diplomatic zones. The management of these processes is handled by UK governmental departments and hence does not fall under this inspection's scope. The weather conditions at this establishment can be extreme with severe heat and dust during summer months while winter brings intense coldness and dampness.
In an effort to emphasize health and safety, PSCOB's national administration has implemented a semi-annual inspection policy. These assessments are specifically targeted at premises exclusively used by PSCOB for security tasks including armed close-protection and
...body-guard services, in addition to training. The team at PSCOB consists of 25-35 members aged between 25 and 55 years old, encompassing positions like Project Manager, Operations Manager, Team Leaders, security operatives, and auxiliary staff who have been recruited both locally and from the UK.
PSCOB refrains from hiring young individuals, those with disabilities or vulnerable individuals due to safety and environmental factors. All PSCOB staff in the UK are ex-UK military or police personnel. The only facilities utilized by PSCOB employees include a Deployment Preparation Area (DPA), a compact 'hangar' like structure used for light vehicle maintenance work, loading vehicles, and preparing equipment users. Also available is an office for management/administrative tasks and a training room.
The examination took place on 10/10/2012, aimed at recognizing both praiseworthy procedures and worrisome areas tha
need immediate or long-term rectification. The Executive Summary reveals that PSCOB upholds a positive attitude towards health and safety, as demonstrated by its high priority to such precautions. Nonetheless, there are some significant issues and shortcomings which call for measures to boost risk management and remove or lessen hazards.
Areas lacking supervision of staff and hazard management could result in serious injuries. This is seen in areas such as the storage of PPE and the failure to use available lifting equipment, as well as in preventing accidents from slips, trips, and falls. Some risk assessments are incomplete and signs and notices do not adequately address the duty of care for local employees. While fire fighting equipment quantities are sufficient and fire drills and maintenance are well managed, some equipment is not effectively deployed.
Instances have been reported where basic fire safety regulations were overlooked. It's crucial to store flammable and combustible materials appropriately, as mandated by the COSHH and fire safety rules. Inadequate upkeep of equipment could lead to health problems or even serious injuries. Environmental factors underline the significance of this issue further. There were cases when certain equipment was not properly maintained without any updates, inspections, maintenance records or examination details.
This report highlights issues that can be rectified using limited resources and funds. The necessary work can be carried out on location, which is crucial given our operation in a challenging and remote setting. Many of the highlighted concerns are breaches of existing health and safety standards. Consequently, dedicating time, finances, and energy to address these will yield long-term advantages for PSCOB. It will also contribute to minimizing accidents
and boosting staff safety levels. Listed below are the principal revelations from the inspection (reference numbers correlate with entries on attached observation sheets).
Workplace Health and Safety
Workplace inefficiencies often stem from a lack of adequate oversight and employees' limited comprehension of the consequences of their actions. Thus, it's paramount for managers, team leaders, and coworkers to collaborate in raising this understanding among staff members. The primary responsibility lies with supervisors to eliminate elements that increase the hazards of slips, trips, and falls. Such items could encompass unsuitable rugs, storage for Personal Protective Equipment (PPE), and used pallets (5, 16, 24 & 27). By implementing straightforward and economically viable changes alongside dialogues with team members and supervisors, management can markedly decrease risks throughout all facilities.
Signs that can be read by all staff (6.) and shared facilities (7) are examples of this. It is not clear if the use of available manual handling was consistently enforced (10). The environmental control systems were good and showed good consideration for climate and temperature in welfare provision. However, more attention is needed in terms of the supply and availability of drinking water (1 & 12). The procedures and work systems related to movement control, interaction with vehicles, and safe/marked routes are well-thought-out. Fire precautions and prevention measures are up to date.
The fire points and equipment are well maintained, but there are areas where the provision and redistribution of Fire Fighting Equipment (FFE) would further decrease fire hazards. The consideration of different classes of fire hazards and suitable FFE for these classes (3, 22, 23, 25) has not been thoroughly addressed. More
supervision is needed to reduce fire hazards and eliminate potential sources of ignition in specific areas (16 & 25). The electrical register and inspection record are adequate, but some electrical equipment is not listed. Additional information and instruction are necessary to emphasize the importance of updating the electrical register (9, 20, 27).
The provision and use of equipment, fault reporting, and inspection and maintenance records for some equipment are not being kept up to date or are not in use (2, 13, & 15). This also applies to hand-tool kits, where there is a quantity checking policy but no fault reporting or exchange procedure (15). Additionally, under separate legislation, items of mechanical lifting aids require inspection, examination, and test certification and documentation (14). There is a lack of understanding of the hazards and risks associated with workstations and DSE at management and supervisory levels (8 & 21).
In general, adequate precautionary and preventative measures are in place for the safe handling and accommodation of COSHH. There is readily available COSHH information and instructions, and the staff questioned are aware of good response procedures. However, some COSHH articles were poorly accommodated and not marked as hazardous (17 & 25). One example showed insufficient use of personal protective equipment when handling COSHH (18). It appears that poor supervision and a violation of what was considered to be an adequate COSHH policy were the reasons for these issues.
PPE
Broadly speaking, the use of personal protective equipment (PPE) was largely adequate. However, there was a notable lack of proper direction and advice when staff were seen handling hazardous liquid without any gloves on.
It seemed that gloves were not conveniently available, leading to insufficient application and employees resorting to taking shortcuts. In this specific instance, non-aggressive workplace environment PPE is necessary, particularly ballistic protection. This type of PPE is readily obtainable and comes with detailed instructions regarding its usage and accessibility. Unfortunately, the work environment lacked suitable storage facilities to assist individuals at their workstation.
If this PPE is not stored or stowed properly, it may become damaged or degraded, posing a risk of serious injury or worse. It is important to comply with statutory regulations such as Regulation 5 of PUWER, which states that equipment must be kept in good working order and repair. Additionally, Regulation 6 requires regular inspection and documentation of any faults or maintenance issues, especially considering the adverse climate and environmental conditions it may be exposed to. Failure to conduct inspections at suitable intervals could lead to dangerous situations like overheating.
The observation (2) indicates that the regulations regarding the faulty portable air-conditioning units have been violated.
Regulation 8 of PPE
It is required by law to properly store Personal Protective Equipment (PPE) when not in use to avoid any damage or deterioration. However, this rule seems to contradict the discoveries about PPE for adverse conditions as stated in DPA (5). On another note, Regulation 10 of Health Safety and Wellbeing (HSW) Management mandates that data pertaining to risk control should be easily understandable by all employees, suggesting translation into other languages if necessary. Yet, several notices and signs fall short of meeting this standard (6).
LOLER requires that lifting equipment undergo a thorough examination prior
to its initial use.
There is no documented proof of such an examination being conducted on a pallet truck currently in use (14).
There is also no indication of a risk assessment or information regarding hazards associated with the CCTV workstation. This violates Regulations 2 and 7 of DSE Regs.
According to Article 12 of the Regulatory Reform Fire Safety Order Part 2, the responsible person (in this case, the Country Operations Manager) must arrange for the safe storage of hazardous substances and implement reasonable precautions to ensure employee fire safety (Article 8).
According to COSHH Reg 7, it is necessary to establish measures that regulate exposure and employ safe handling procedures including the use of personal protective equipment (PPE). However, this regulation has been violated due to the absence of gloves or improper use of gloves, as well as the absence of labels on COSHH bottles refered to as item 17 and 18. The response to this report will determine the reputation of PSCOB and the level of commitment from management towards ensuring the safety and well-being of all individuals involved in PSCOB security operations. PSCOB is legally obligated to rectify any breaches of statutory regulations, which are clearly outlined above.
Steps are being implemented to rectify regulatory breaches with the aim of avoiding potential investment proposals, contract and business expansion opportunities from being impeded by unnecessary legal actions. This is achieved primarily through standardizing documentation and certification processes for equipment, requiring only a minimal investment in terms of time and resources. Such preventive strategies are preferable over facing higher legal expenses, personal claim settlements, and penalties - all of
which can be avoided. PSCOB operates in a challenging environment where the welfare of all participants is paramount.
PSCOB's management is tasked with the obligation to guarantee a secure working environment by supplying safe machinery, facilities, and welfare. This needs to be an established norm. Upholding the usage of personal protective equipment (PPE) and appropriate lifting gear is essential for any entity aiming at fostering a healthy and secure workplace. Furthermore, routinely offering clean drinking water should also be part of their duty. At present, the profits from PSCOB's contract are derived from available staff, security tools, and the count of successfully accomplished security tasks on a daily basis.
Inadequate COSHH measures or defective temperature regulation systems can cause both immediate illness and long-term health conditions, leading to financial setbacks due to the unavailability of staff and equipment needed for regular operations. Without a functioning business core, revenue generation is impossible. Moreover, securing close protection contracts and growing the business has become increasingly difficult each year. Abundant evidence suggests that potential customers who see a properly managed and safe workplace with all essential safety precautions in place tend to be more likely to invest in or use PSCOB's services.
Conclusion
Broadly speaking, the personnel at PSCOB demonstrate a positive outlook towards health and safety. Despite this, the report points out various issues that require attention from supervisors and management. In particular, there is an insufficient level of oversight to thwart incidents such as slips, trips, and obstructions caused by traffic within the workplace. Instances of these include unattended pallets, a jointly used staircase lacking risk assessment, and an
unidentified curb step. Furthermore, there's worry about the deficient supervision and strictness regarding manual handling aids. It's crucial to act promptly to ensure comprehensibility of instructions for everyone.
Improvements are required in the oversight and distribution of drinkable water. Risk assessments should take into account common utilities or access/egress points. Certain cases violate Health ; Safety (Workplace) Regulations, including fundamental stipulations of HSW Act 1974 Section 2. The highlighted concerns about fire safety indicate that standard fire safety principles are being addressed, specifically concerning records/documents. However, some areas require more comprehensive information.
The office has examples of contraventions of the Reg Reform Fire Safety Order and Elec Safety Regs, including the distribution of appliances and unnecessary bulk supplies of paper. Inadequate electrical safety measures have also been highlighted in the findings and observations. Improvement is needed in the maintenance, inspection, and efficiency of equipment. Records and documentation were not available for portable air-conditioners, lifting equipment, and exhaust extractors, which goes against the requirements of PUWER and LOLER.
Precautions and responsive/preventative measures for hazardous substances are in place but lack of supervision and general lack of application resulted in instances of poor storage, inadequate labelling, and inadequate use of personal protective equipment (PPE). These actions violate the general requirements of the Control of Substances Hazardous to Health (COSHH) Regulations. The importance of correctly storing potentially life-saving PPE that provides ballistic protection from hostile acts should be emphasized. Supervision and instruction will ensure appropriate use of PPE such as gloves to comply with the statutory PPE Regulations. Most of the raised issues can be easily and inexpensively resolved by making minor adjustments and alterations
to management, supervision, and facilities.
- Computer File essays
- Desktop Computer essays
- Servers essays
- Anatomy and Physiology essays
- Addiction essays
- Biodegradation essays
- Dental Care essays
- Disease essays
- Disorders essays
- Health Care essays
- Intelligence Quotient essays
- Nutrition essays
- Olfaction essays
- Public Health essays
- Women's Health essays
- World health organization essays
- Cancer essays
- Infectious Disease essays
- Lung Cancer essays
- Neurology essays
- Physical Exercise essays
- Medicine essays
- Sex essays
- Inquiry essays
- Disability essays
- Poison essays
- Action Potential essays
- Nervous System essays
- Childbirth essays
- Puberty essays
- Blood essays
- Kidney essays
- Neuron essays
- Body essays
- Glucose essays
- Sense essays
- Heart essays
- Skeleton essays
- Human Physiology essays
- Eye essays
- Immune System essays
- Muscle essays
- Skin essays
- Brain essays
- Central Nervous System essays
- Human Skin Color essays
- Digestive System essays
- Common sense essays
- Respiration essays
- alcoholism essays