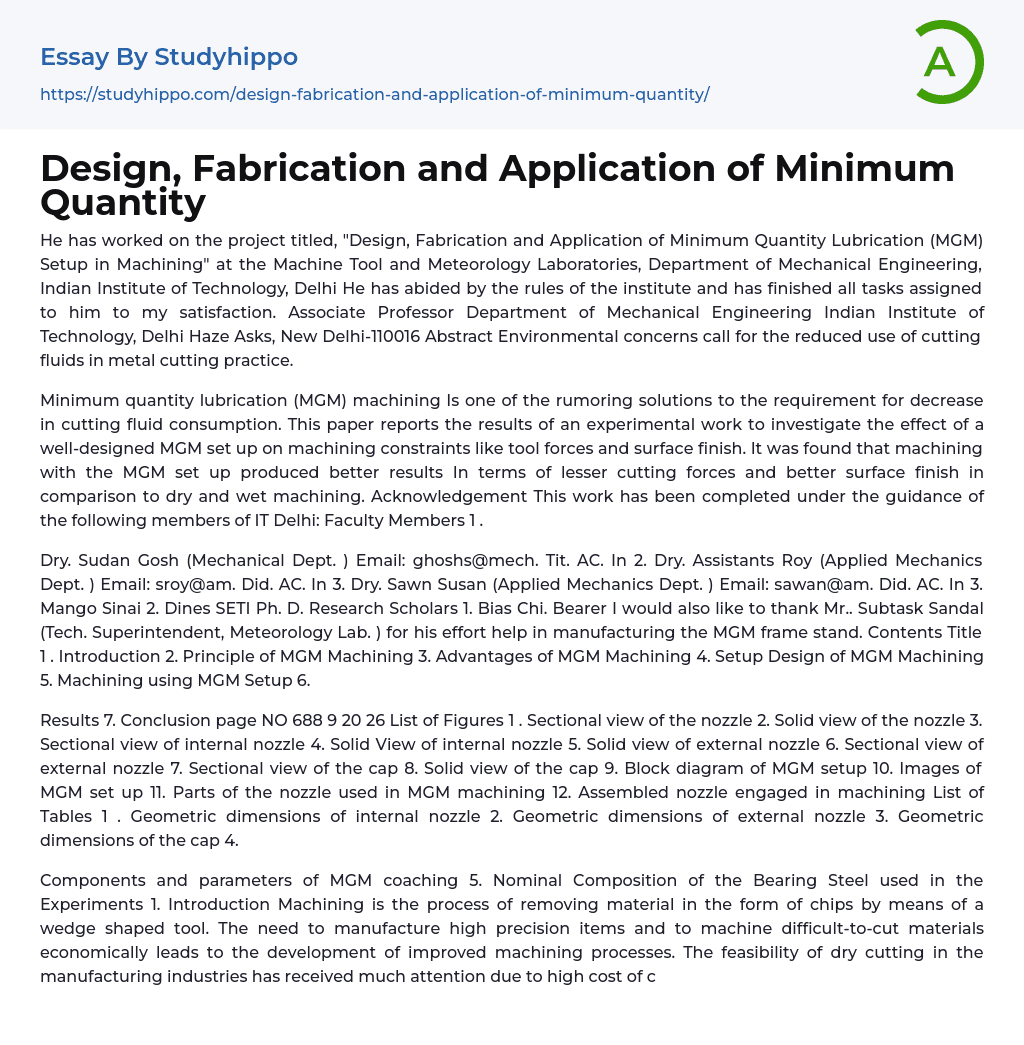
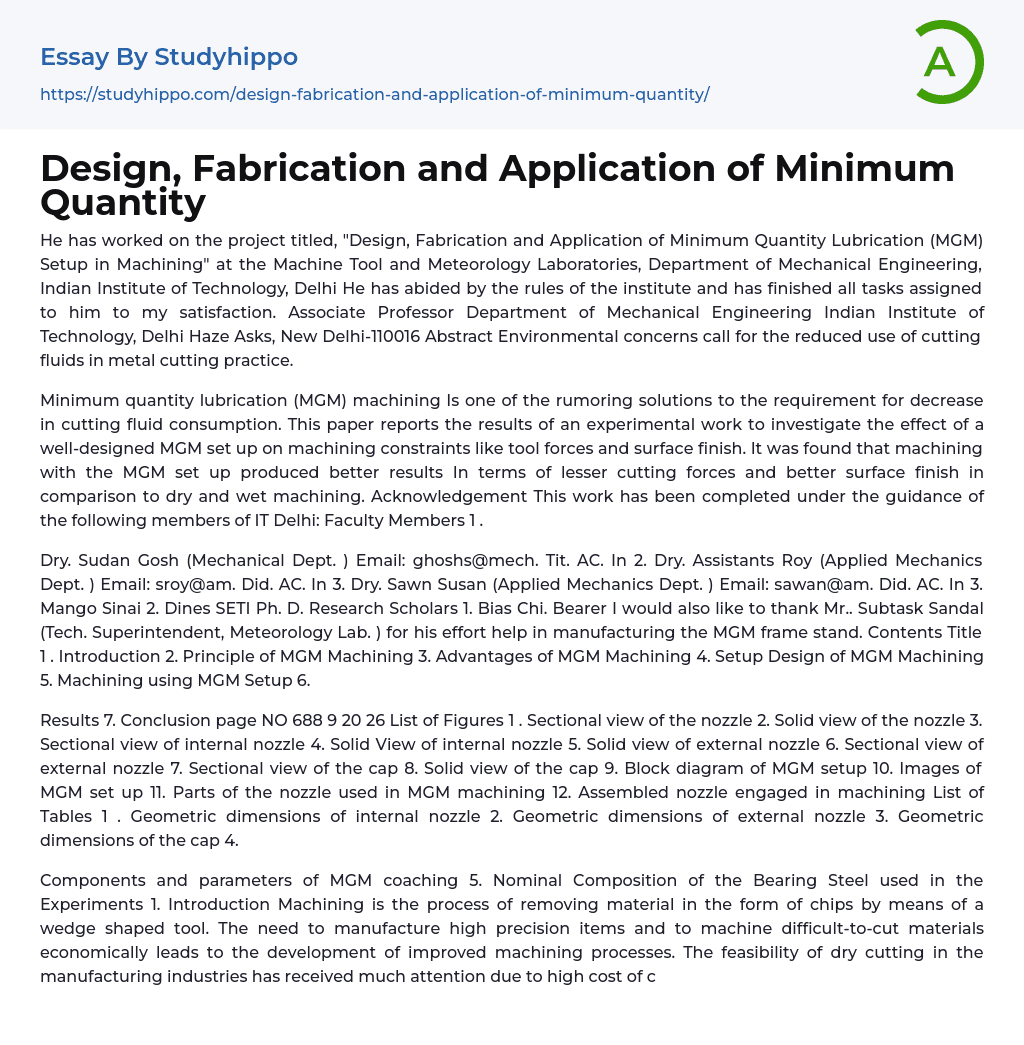
Design, Fabrication and Application of Minimum Quantity Essay Example
The project titled "Design, Fabrication and Application of Minimum Quantity Lubrication (MGM) Setup in Machining" was successfully completed at the Machine Tool and Meteorology Laboratories, Department of Mechanical Engineering, Indian Institute of Technology, Delhi. The individual followed the institute's rules and fulfilled all assigned tasks satisfactorily. An Associate Professor from the Department of Mechanical Engineering at Indian Institute of Technology, Delhi recommends this individual's work. Haze Asks, New Delhi-110016 Abstract: The need to reduce the use of cutting fluids in metal cutting practice has led to the development of minimum quantity lubrication (MGM) machining. This paper presents the findings of an experimental study that examined the impact of a well-designed MGM setup on machining factors such as tool forces and surface finish. The results showed that using the MGM se
...tup resulted in improved outcomes compared to dry and wet machining, with reduced cutting forces and enhanced surface finish observed. Acknowledgement: This project was completed under the guidance of various faculty members at IT Delhi, including Sudan Gosh and Assistants Roy and Sawan Susan from the Mechanical and Applied Mechanics Departments. Assistance during this project was also provided by Mango Sinai and Dines SETI. D. Research Scholars would like to thank Bias Chi.Bearer and Mr. Subtask Sandal for their help in manufacturing the MGM frame stand.
The title contains the following sections: Introduction, Principle of MGM Machining, Advantages of MGM Machining, Setup Design of MGM Machining, Machining using MGM Setup, Results, and Conclusion. The page numbers for these sections are 688, 9, 20, and 26. There is also a list of figures including sectional views and solid views of the nozzle and cap as well as
a block diagram and images of the MGM setup. Additionally, there is a list of tables containing geometric dimensions, components and parameters of MGM coaching, and the nominal composition of the Bearing Steel used in the experiments.
The purpose of machining is to remove material using a wedge-shaped tool to manufacture high precision items economically. Dry cutting has gained attention in manufacturing industries due to the high cost and health risks associated with cutting fluids. Cutting fluid waste must be treated before disposal and prolonged exposure can lead to skin cancer and breathing difficulties. Dry cutting reduces costs while eliminating negative effects related to cutting fluid usage for cooling and lubrication purposes. However, cutting fluids are still necessary when machining difficult-to-machine materials such as super alloys [3].The application of cutting fluids provides significant benefits, such as increased productivity, improved surface quality of machined workpieces, and the ability to perform processes at higher speeds, feed rates, and cutting depths. This is achieved by enhancing lubricity and cooling at the chip-tool and chip-workplace interface. When effectively utilized, cutting fluids can enhance surface finish, dimensional accuracy, and decrease power consumption [4].
Moreover, using cutting fluid serves multiple purposes in cutting processes. It aids in removing heat and chips generated during cutting process, thereby prolonging tool lifespan [5]. However, concerns about the cost of cutting fluid and health risks associated with exposure to its mist have led both industry and academia to reevaluate their role. Additionally, increased focus on environmental sustainability in manufacturing has resulted in stricter regulations regarding the use of cutting fluids in machining operations particularly in countries like the United States [6].
To address these concerns while still benefiting
from the advantages of using cutting fluids, several noble approaches have been adopted. One such approach involves carefully selecting suitable cutting fluids based on various machining conditions and parameters which is a crucial yet complex process [7].Over time, there has been a shift in the use of oils for machining. Initially, straight oils were used, but they were then replaced by soluble oils. Eventually, vegetable and synthetic oils became more popular. This transition was driven by their superior cooling and lubricating properties, as well as their safer handling and disposal methods, which are environmentally friendly [7-9].
Proper application of cutting fluids is crucial to ensure efficient machining. Often, a significant amount of the applied fluid goes to waste without contributing to the process. Therefore, factors like nozzle design, placement, supply system, and other machining conditions need to be considered in order to effectively manage these areas. Additionally, careful management of cutting fluids after use is important to minimize their impact on health and the environment while reducing disposal costs.
A promising step towards reducing cutting fluid usage is the increased implementation of near-dry and dry machining over the past few decades. These advanced processes aim to require less or no cutting fluid at all. While dry machining offers advantages such as producing cleaner parts, generating no waste, reducing costs, and eliminating residual oil for chip recycling; it also comes with drawbacks that need to be considered carefully due to its associated costs.The main challenge in transitioning to dry machining is the significant initial investment needed to establish a dry machining operation. Machinery and tools designed for cutting fluids cannot easily be adapted for dry cutting, requiring the
purchase of new and more powerful machines. Special tooling is often necessary to withstand the high temperatures generated during dry cutting. Dry machining has a significant impact on the quality of machined parts by altering their metallurgical properties and residual machining stresses. It can also cause part distortion and make them hot, making handling and inspection challenging. To address these issues, near-dry machining (NDM) was developed as a solution.
In NDM, a small quantity of cutting fluid is supplied in atomized droplet size with high velocity. This method uses much less oil compared to conventional flood application. NDM offers the combined benefits of dry and flood machining in an environmentally friendly manner. The amount of oil used is minimal, resulting in mostly dry parts involved in metal removal. However, compressed air delivers a small yet sufficient amount of oil precisely to the machining zone for cooling, lubrication, and chip removal using a high-velocity air jet.[1] demonstrated that MGM resulted in lower cutting forces and improved surface finish compared to dry machining. In addition, they observed a decrease in temperature of approximately 5% in MGM turning, 10-15% in MGM end milling, and 20-25% in MGM drilling compared to dry cutting. [12] discovered that using vegetable oil as a lubricant in MGM reduced cutting forces by about 5-15%, with a more significant reduction seen in axial force than power force. This decrease, along with enhanced tool life and surface finish, was attributed to the lower temperature achieved in the cutting zone. Similar findings were reported for machining 1040 steel [13]. Furthermore, when machining 1045 steel, Lie and Liana [14] found lower cutting forces in MGM compared to dry
cutting due to the temperature difference. Dharma et al., who compared MGM with wet machining, investigated the impact of MGM on tuning 4340 steel [15]. They utilized an external nozzle and aerosol supply to deliver the lubricant to the tool and observed a reduction of about 5-10% at the tool-chip interface's temperature compared to wet machining (depending on cutting speed and feed). Consequently, an improvement of up to 15-20% was seen in tool life and surface finish. For gun-drilling and cross-hole drilling of crankshafts, Philippic and Stephenson [16] noted similar tool life between wet machining and MGM. Brag et al.'s study did not provide any specific information within this context[17] In drilling aluminum-silicon alloys, it was found that using MGM with a diamond-coated tool led to improved performance in terms of forces, tool wear, and amount of water-soluble oil. This improvement was observed regardless of whether the drills were coated or uncoated.
[18] David et al. concluded that by selecting the appropriate MGM system, similar results to flood lubricant conditions can be achieved when turning brasses.
Despite numerous research papers attempting to explain the distinct outcomes of MGM machining, conclusive evidence has not been provided directly due to the difficulty of analyzing the topic [19]. V.P. Astrakhan proposed a plausible explanation in his literature [19]: the cutting fluid's embitterment action reduces strain on the work material through the utilization of the Rebind effect, which is closely related to the metal cutting process. He suggests that atomized oil has a greater ability to enhance embitterment in removing layers, thereby reducing plastic deformation in transforming these layers into chips.
The design of MGM machining aerosols plays a crucial role in
determining droplet concentration and size. Two supply methods exist: external supply through separate nozzles and internal supply through built-in channels within tools. Each method has specific applications. In CNN turning, external supply is utilized where aerosol is sprayed onto the tool from outside via a closely fitted nozzle.This technique is used in sawing, end and face milling, and turning operations. In addition to a well-designed nozzle, other equipment needed for MGM set up in CNN turning includes a compressor for pressurized air. A pressure gauge is installed near the nozzle to measure the incoming air pressure. The oil is continuously sent to the nozzle in small amounts using a pump and oil reservoir. A stopper is used to check and measure the flow rate of the oil. A frame stand supports all these components conveniently.
To achieve proper mixing of oil with air, it is necessary for the oil to be atomized into fine droplets by the compressed air. Additionally, the transition of oil through the nozzle should be smooth, continuous, and with enough velocity to effectively penetrate the machining interfaces.
To meet these requirements, an internally mixed air assisted atomizer has been designed (Figure 1 and 2). This design includes an internal nozzle that introduces a high velocity jet of air at its exit. The internal nozzle is fitted into an external nozzle with a fine orifice for oil inlet near its exit point. The connection between internal and external nozzles is secured using a cap tightened by screws.
The design parameters that are not crucial in this particular field have been adjusted to align with locally available designs that are easier to fabricate. The design of
the internal nozzle takes inspiration from various sources on fluid mechanics.According to certain papers, the ability of an air jet to penetrate a hard-to-reach plastic area where the chip and tool meet during metal machining is enhanced by a higher air jet velocity. Taking this into consideration, the nozzle is designed with the aim of achieving an air jet velocity that is very high, comparable to or greater than the speed of sound. A simple converging nozzle can increase the air jet velocity up to Mach 1 (the speed of sound) given the prevailing temperature conditions. However, even when there is an increased mass flow rate of air, the outlet speed does not go beyond this "choked" condition. On the other hand, a converging-diverging nozzle - which includes an initial converging section followed by a diverging section and a throat at its minimum cross-section - has the capability to significantly increase the air jet velocity at exit well above Mach. Depending on factors such as inlet pressure and temperature conditions, mass flow rate of air, and cross-sectional areas at throat and exit points; once reaching Mach 1 at throat level, the air jet's velocity continues to rise further. This increase in velocity causes a shock wave occurrence at any specific cross-section within the diverging section due to sudden changes in pressure and temperature conditions. If all parameters are meticulously controlled, this shock wave will only happen right at the nozzle's exit point.The turbulence in the region allows the cutting fluid to enter through the orifice in the exterior nozzle, while the high-speed air jet effectively atomizes the oil particles. The cross-sectional areas of adiabatic conditions
at the throat and exit can be determined using the following equations. This approximation is valid due to significantly high fluid flow speed. The inlet air stream is stagnant with zero velocity. Inlet or stagnation properties are represented by subscript zero, throat properties by subscript t, and exit properties by subscript e. The symbols used have their usual meanings.
The steady flow energy equation can be expressed as h t + (v/2) = C p T O = C p T t + (v t 2/2). Assuming air behaves as a perfect gas, we can write C p T O = C p T t + (v t 2/2). By using C p = , we obtain (T O /T t) = 1+ ((y-1)/2)*M t 2, where M t represents the Mach number at the throat - v t /(YURTt )0.5.
For air under adiabatic conditions at the throat, we have two relationships: (P? / P?) = (T? / T?) and (P? / P?) = (T? / T?). For air with a ? value of 1.4, achieving Mach 1 at the throat requires 1.2(P? / 1.893(P? / 1.577.
The mass flow rate can be calculated using m? = A? * v?, where A? represents the cross-sectional area at the throat Alternatively, m =(? / ART?)^?.^? * (P?/A?)^?.^???.
Using the SAFE and adiabatic relations between the throat and exit, we can also derive (T? / T?)^? * M? = m? * v?, where A? is the cross-sectional area at the throat.We aim for a Mach number of 1.5 at the exit of the internal nozzle, so the throat will have an air speed equal to Mach 1. The inlet conditions
are P? = 6 bar, T? = ICC, and d? = 1 mm for ease of fabrication. From these conditions, we find m = 1 G/s and v? = 432.5 m/s. The diameter at the nozzle exit is approximately d? = 1 mm.
Due to factors of irreversibility, there will be some energy loss from the air flowing through the nozzle, resulting in a decrease in velocity at the exit compared to the desired value. To account for this and ease of fabrication, we have increased the diameter at the nozzle exit to d? = 2 mm. All other dimensions can be seen in Figure 3 and Table 1.
The internal nozzle is considered noninsured based on material strength, ease of fabrication, and conformity to local standards. Figure 3 provides a sectional view of the internal nozzle while Figure 4 shows a solid view. Table 1 includes geometric dimensions such as ID (internal diameter) at inlet, throat, and exit; lengths of converging and diverging parts; and thickness of the nozzle.
For the external nozzle design concept, we have derived it from standard models available in the market but with modifications to meet our specific requirements. The external nozzle has multiple important tasks to fulfill.
The proper enclosure of the internal nozzle is crucial to prevent interference from external sources. It should also have a well-designed orifice near its exit for oil intake. Additionally, it needs to incorporate a mixing section for oil and supersonic air, followed by a streamlined converging flow towards the exit. The design of the external nozzle can be seen in Fig.5 and Fig.6 (Figures 1 and 2 are included for discussion purposes). Figure 5 provides
a solid view of the external nozzle, while Figure 6 presents a sectional view. Table 2 includes the geometric dimensions of the external nozzle, such as the internal diameter at both inlet and exit, length of converging and straight sections, thickness of the nozzle, internal diameter of oil inlet orifice, and distance between the exit of the internal nozzle and start of converging section.
To determine the velocity of aerosol at the exit of the external nozzle, certain criteria need to be considered. The mass flow rate (m o ) for oil is determined to be 1 g/min based on its similarity in density with water-soluble oil. Previously calculated mass flow rate (m) for air is found to be 1.1 g/s. Therefore, total mass flow rate (m t ) amounts to 1.116 g/s.At atmospheric conditions prevailing at the exit – pressure (P) being 1 bar and temperature (T) ICC = KICK – density (p) is calculated as 1 Keg/mm.The assumed diameter at nozzle's exit is mmThe continuity equation (m t = PAP) is used to determine the Fame/s, which corresponds to a high velocity similar to Mach 1.4.1. The cap has been designed in a manner that allows for easy connection and disconnection of the external and internal nozzles. The internal nozzle fits tightly within the cap and is secured to the external nozzle using threaded nuts. Figure 7 and 8 illustrate the design of the cap. Table 3 provides geometric dimensions of the cap, including sizes of the external and internal nozzles, number and size of bolts, and material selection for the nozzle.
When selecting a material for the nozzle, it is important to consider factors
such as corrosion resistance, erosion resistance, durability, performance, cost-effectiveness, strength-to-weight ratio, and ability to withstand low temperature fluids without distorting in shape. Brass was chosen as it possesses desirable properties including strength, ductility, corrosion resistance, incapability, availability in various forms and sizes.
To measure nozzle strength, we will consider the minimum yield strength value for brass which is approximately 124 Amp for safety reasons. When calculating hoop stress - an essential specification for determining its strength against failure - it can be assumed that there is negligible deviation from cylindrical shape for the nozzle.The formula used to calculate the circumferential stress (hoop stress) in the nozzle is o h = PDP/at, where p represents the air pressure, D is the internal diameter of the nozzle, and t is the thickness of the nozzle. The maximum expected pressure that the nozzle will face is p= bar = 8*105 Pa. As air expands within the internal nozzle, the pressure will decrease in the annular space of the external nozzle. To ensure the strength of the interior nozzle material, it is sufficient to check the section with D= mm for its maximum external diameter. The thickness remains constant at t= mm. Therefore, based on these calculations, we determine that o h = 1.6 Amp as maximum hoop stress inside the nozzle. This value falls below brass's yield stress, indicating that there is no risk of tensile stress failure from a design perspective.
The manufacturing process for this specific nozzle assembly was carried out by an industry located in New Delhi which possesses advanced and modern machines capable of achieving accurate dimensions up to a micron scale. The complete MGM system
consists of various components including a fluid supply system consisting of an oil storage burette and small pump for continuous oil supply from said burette along with an IV set for maintaining oil level under pressure from inlet to nozzle via gravitational head. A control valve measures and controls desired small quantities of oil supplied to said nozzle.The air supply system consists of a compressor with a maximum capacity of 8 bar. A pressure gauge is installed near the air inlet to measure the delivery pressure, which is then connected to the nozzle through hose pipes.
- Factory essays
- Material essays
- Production And Manufacturing essays
- Alarm clock essays
- Energy essays
- Density essays
- Thermodynamics essays
- Motion essays
- Atom essays
- Sound essays
- Electricity essays
- Nuclear Power essays
- Temperature essays
- Physiology essays
- Light essays
- Force essays
- Heat essays
- Speed essays
- Big Bang Theory essays
- Energy Development essays
- The elements essays
- Voltage essays
- Solar Energy essays
- Nuclear Energy essays
- Alternative Energy essays
- Melting essays
- Nuclear Family essays
- Accounting essays
- Andrew Carnegie essays
- Automation essays
- Business Cycle essays
- Business Intelligence essays
- Business Model essays
- Business Operations essays
- Business Software essays
- Cooperation essays
- Cooperative essays
- Corporate Social Responsibility essays
- Corporation essays
- Customer Relationship Management essays
- Family Business essays
- Franchising essays
- Harvard Business School essays
- Harvard university essays
- Human Resource Management essays
- Infrastructure essays
- Inventory essays
- Logistics essays
- Management essays
- Manufacturing essays