Operations Management Exam #1 – Flashcards
Unlock all answers in this set
Unlock answers
question
Organizations Have 3 Basic Functions
answer
Marketing Operations Finance
question
What is Operations?
answer
The part of a business organization that is responsible for producing goods or services Influences all of the rest of the organization The actual doing part of the business process
question
What is Operations Management?
answer
The management of systems or processes that create goods and/or provide services
question
Operations Management affects:
answer
Companies' ability to compete
question
Why study OM?
answer
Every aspect of business affects or is affected by operations There is a significant amount of interaction and collaboration amongst the functional areas
question
The Operations Function
answer
The creation of goods and services through the transformation of inputs into outputs
question
Feedback
answer
measurements taken at various points in the transformation process
question
Control
answer
The comparison of feedback against previously established standards to determine if corrective action is needed.
question
Value Added
answer
value/price of output - cost of input
question
Processes (Managing to Meet Demand)
answer
Operations ; Supply Chains vs Sales and marketing Supply ? Demand is wastefully costly Supply ; Demand causes Opportunity Loss/Customer Dissatisfaction Supply = Demand is Ideal
question
Processes (Variation)
answer
Variations can be disruptive to operations and processes. They may result in additional costs, delays and shortages, poor quality, and inefficient work systems.
question
Manufacturing
answer
goods-oriented (tangible things) physical items that include raw materials, parts, subassemblies, and final products. Automobile Computer Oven Shampoo
question
Service
answer
act-oriented activities that provide some combination of time, location, form or psychological value. Air travel Education Haircut Legal counsel
question
Goods-service Continuum
answer
Products are typically neither purely service- or purely goods-based.
question
Products Package
answer
combinations of goods and services
question
Scope of Operations Management
answer
The operations function includes many interrelated activities such as: Forecasting (we won't cover, but important) Capacity planning Facilities and layout Scheduling Managing inventories Assuring quality Motivating employees Deciding where to locate facilities And more . . .
question
Role of the Operations Manager
answer
The Operations Function consists of all activities directly related to producing goods or providing services. A primary role of the operations manager is to guide the system by decision making. -System Design Decisions -System Operation Decisions
question
System Design Decisions
answer
-Capacity -Facility location -Facility layout -Product and service planning These are typically strategic decisions -usually require long-term commitment of resources -determine parameters of system operation
question
System Operation Decisions
answer
These are generally tactical decisions -Management of personnel -Inventory management and control -Scheduling -Project management -Quality assurance
question
Decision Making
answer
Most operations decisions involve many alternatives that may have different impacts on costs or profits Typical operations decisions include: What: What resources are needed, and in what amounts? When: When will each resource be needed? When should the work be scheduled? When should materials and other supplies be ordered? Where: Where will the work be done? How: How will he product or service be designed? How will the work be done? How will resources be allocated? Who: Who will do the work?
question
Model
answer
an abstraction of reality; a simplified representation of something
question
Types of Models
answer
Physical Models -Look like their real-life counterparts Schematic Models -Graphs, Charts, Blueprints, Drawings, etc. Mathematical Models
question
Common Features of Models
answer
simplifications of real-life phenomena Focus on the most important aspects of the real-life system & omit unimportant details
question
Benefits of Models
answer
Models are generally easier to use and less expensive than dealing with the real system Serve as a consistent tool for evaluation and provide a standardized format for analyzing a problem Require users to organize and sometimes quantify information Increase understanding of the problem Enable managers to analyze "What if?" questions
question
Limitations of Models
answer
Important variables may be missed Quantitative information may be emphasized over qualitative Models may be incorrectly applied and results misinterpreted Nonqualified users may use the model incorrectly
question
Quantitative Methods
answer
A decision making approach that seeks to obtain a mathematically optimal solution -Linear programming -Queuing techniques -Inventory models -Project models -Forecasting techniques -Statistical models
question
Historical Evolution of OM
answer
Industrial Revolution Scientific Management Decision Models and Management Science Influence of Japanese Manufacturers
question
Pre-Industrial Revolution
answer
Craft production - highly skilled workers use simple, flexible tools to produce small quantities of customized goods
question
Industrial Revolution
answer
The Industrial Revolution (late 18th century) -Began in England in the 1770s -Division of labor - Adam Smith, 1776 -Application of the steam engine, 1780s -Cotton Gin and Interchangeable parts - Eli Whitney, 1792 Substituting machine power for human power. Management theory and practice did not advance appreciably during this period
question
Scientific Management (Early 20th century)
answer
"Science of Management" based on observation, measurement, analysis and improvement of work methods, and economic incentives Management is responsible for: -planning, carefully selecting and training workers -finding the best way to perform each job Emphasis was on maximizing output -Ford Model-T, 1908-1927 -Modern-Times, 1936
question
Decision Models & Management Science (Mid 20th century)
answer
OR applications in warfare - Operations Research (OR) Groups Mathematical model for inventory management (F.W. Harris, 1915) Statistical procedures for sampling and quality control (Dodge, Romig & Shewart , 1930s) Statistical sampling theory (Tippett, 1935) Linear programming (George Dantzig , 1947)
question
Influence of Japanese Manufacturers
answer
Late 20th century Refined and developed management practices that increased productivity -Credited for the "quality revolution" -continual improvement -employee empowerment -Lean Operations / Just-in-Time production
question
Key Issues for Operations Managers Today
answer
Economic conditions Innovating Quality problems Management technology The Internet, e-commerce, e-business Supply chain management Risk management Revenue management Competing in a global economy Globalization, Outsourcing Environmental concerns Ethical behavior
question
Customization
answer
requires more resources and effort than more standardized products and services
question
Theory X
answer
Workers do not like work and must be induced to do it
question
Theory Y
answer
Workers enjoy work and are committed to doing it
question
Components of the Supply Chain
answer
Forecasting, purchasing, inventory management, information management, quality assurance, scheduling, production, distribution, delivery, and customer service Doesn't include marketing or finance because those are the two other functions of an organization next to operations
question
Ethics
answer
a standard behavior that guides how we should act in various situations
question
Business Sustainability
answer
refers to economic, environmental, and social sustainability
question
Division of Labor
answer
allows employers to employ less-skilled workers than would have been needed in craft production
question
Which of the following are reasons organizations fail?
answer
Not investing enough in necessary capital or human resources Underestimating the importance of internal communication and cooperation between functional areas Putting too much emphasis on short term financial performance Not focusing enough on process design and improvement Failure to correctly focus on customer wants and needs
question
Three separate, but related concepts that are vitally important to business organizations:
answer
Competitiveness Productivity Strategy
question
Competitiveness
answer
How effectively an organization meets the wants and needs of customers relative to others that offer similar goods or services Organizations compete over: -Price (Cost) -Quality -Response-time -Variety (Flexibility)
question
Quality Based Strategies
answer
may be apart of another strategy
question
3 Basic Business Strategies
answer
Low cost, responsiveness, differentiation
question
Planning and Decision Making
answer
Start at the top with a mission (vision)
question
Order Qualifiers
answer
Characteristics that customers perceive as minimum standards of acceptability for a product or service to be considered as a potential for purchase
question
Order Winners
answer
Characteristics of an organization's goods or services that cause it to be perceived as better than the competition
question
Price, delivery reliability, delivery speed and quality can be qualifiers or order winners
answer
and may change over time.
question
Mission
answer
The reason for an organization's existence that serves as the basis for organizational goals Mission statement -States the purpose of the organization -Answer the question: "What business are we in?"
question
Supply Chain Strategy
answer
should align with overall business strategy
question
Example Strategies an Organization Might Choose From
answer
Low Price Specialization -narrow product lines or limited services Variety -e.g., customization Newness -innovation to create new products or services Service -various aspects of service (e.g., helpful, reliable, etc.) Sustainability -environmentally friendly and energy efficient operations Quality Responsiveness (time-based strategies) -reduction of time needed to complete products or perform services
question
Goals
answer
Provide detail and the scope of the mission Goals can be viewed as organizational destinations The basis for organizational strategies
question
Strategy
answer
A plan for achieving organizational goals Serves as a roadmap for reaching the organizational destinations
question
Strategy Formulation
answer
1. Core Competencies 2. Environmental Scanning (SWOT) 3. Order Qualifiers & Order Winners
question
Core Competencies
answer
The special attributes or abilities that give an organization a competitive edge To be effective core competencies and strategies need to be aligned
question
Environmental Scanning - SWOT
answer
Environmental Scanning is necessary to identify: Internal Factors (Strengths and Weaknesses) External Factors (Opportunities and Threats)
question
Key Internal Factors
answer
Human Resources Skills of workforce, expertise, experience, loyalty to the organization Facilities and equipment Capacities, locations, age, maintenance costs Financial resources Cash flow, access to additional funding, debt, cost of capital Customers Loyalty, wants and needs Products and services Existing, potential for new ones Technology Existing, ability to integrate new and its impact on current and future operations Suppliers Relationships, dependency, quality, flexibility, service Other Labor relations, company image, distribution channels etc.
question
Key External Factors
answer
Economic conditions Health and directions of the economy, inflation, deflation, interest rates, taxes, tariffs. Political conditions Attitude towards business, political stability, wars Legal environment Antitrust laws, regulations, trade restrictions, minimum wages laws, liability laws, labor laws, patents Technology Innovations rate, future process technology, design technology Competition Number and strength of competitors, basis of competitions (price, quality etc.) Markets Size, location, brand loyalty, ease of entry, growth potential, long term stability, demographics.
question
Organizational Strategies
answer
Overall strategies that relate to the entire organization and support the achievement of organizational goals and mission
question
Functional level strategies
answer
Strategies that relate to each of the functional areas and that support achievement of the organizational strategy
question
Operations Strategy
answer
The approach, consistent with organization strategy, that is used to guide the operations function. But... Organization Strategy should take into account the realities of operations strengths and weaknesses
question
Tactics
answer
The methods, actions, or implementations taken to accomplish strategies, which ultimately achieve goals The "how to" part of the process
question
Productivity
answer
A measure of the effective use of resources usually expressed as the ratio of output to input Productivity measures are useful for: -Tracking an operating unit's performance over time -Planning workforce requirements -Scheduling equipment -Financial analysis
question
Why does Productivity Matter?
answer
Higher productivity relative to the competition leads to competitive advantage in the marketplace. High productivity is linked to higher standards of living -; Have more, work less. Manufacturing multiplier (1.6-16): manufacturing has beneficial side effect -; service jobs. Manufacturing incorporates R -; competitive edge.
question
Measures of Productivity
answer
Partial measures: output/(single input) Multi-factor measures: output/(multiple inputs) Total measure: output/(total inputs)
question
Productivity Calculation Example Units produced: 5,000 Standard price: $30/unit Labor input: 500 hours Cost of labor: $25/hour Cost of materials: $5,000 Cost of overhead: 2x labor cost
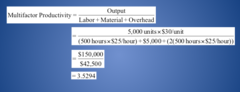
answer
larger than 1, but is it good enough? The higher the better
question
Productivity Growth Example
answer
Labor productivity on the ABC assembly line was 25 units per hour in 2009. In 2010, labor productivity was 23 units per hour. What was the productivity growth from 2009 to 2010?
question
Service Sector Productivity
answer
difficult to measure and manage involves intellectual activities has a high degree of variability
question
Factors Affecting Productivity
answer
Methods Quality Capital Technology -INCREASE: Calculators, Computers, Faxes, copiers, Internet search engines, Voice mail, cell phones, email -REDUCE: inflexibility, high costs, mismatched operations, non-work activities Management
question
Improving Productivity
answer
1. Develop productivity measures for all operations 2. Determine critical (bottleneck) operations 3. Develop methods for productivity improvements 4. Establish (reasonable) goals 5. Make it clear that management supports and encourages productivity improvement 6. Measure and publicize improvements 7. Don't confuse productivity with efficiency
question
Efficiency = getting the most out of a fixed set of resources
answer
Productivity = effective use of overall resources (e.g., upgrading equipment)
question
OM Incorporates
answer
suppliers employees distributers retailers
question
What is the first step in creating a new operation
answer
design of product and process to produce it
question
What might cause a business to change?
answer
changes in the market
question
Start of Chapter 4 Notes: Product and Service Design
answer
The essence of an organization is the goods and services it offers Every aspect of the organization is structured around them Product and Service design (or redesign) should be closely tied to an organization's strategy
question
Reasons for Design or Re-Design
answer
Market Opportunities or Threats drive product and service design (or redesign): Economic -Low demand, need to reduce costs, quality problems Social and Demographic -Aging populations, population shifts Political, Liability, or Legal -Regulations, safety issues Competitive -New or changed products and services Cost or Availability -Raw materials, components, labor, energy Technological -Product components, processes
question
Idea Generation Supply-Chain Based
answer
Ideas can come from anywhere in the supply-chain: -Customers -Suppliers -Distributors -Employees
question
Idea Generation Competitor-Based
answer
Studying how a competitor operates and its products and services
question
Reverse engineering
answer
Dismantling and inspecting a competitor's product to discover product improvements
question
Idea Generation Research Based
answer
Research and Development (R&D) -Organized efforts to increase (scientific) knowledge or product innovation Basic research -Objective: advancing the state of knowledge about a subject without any near-term expectation of commercial applications Applied research -Objective: achieving commercial applications Development -Converts the results of applied research into useful commercial applications.
question
Quality Function Deployment
answer
An approach that integrates the "voice of the customer" into product and service development The purpose is to ensure that customer requirements are factored into every aspect of the process
question
Phases in Products Design & Development
answer
1. Feasibility analysis -Demand, development and production cost, potential profit, technical analysis, capacity req., skills needed, fit with mission. 2. Product specifications -What's needed to meet customer wants 3. Process specifications -Weigh alternative processes in terms of cost, resources, profit, quality 4. Prototype development -Few units are made to find problems with the product or process 5. Design review -Changes are made or project is abandoned 6. Market test -Determine customer acceptance. If unsuccessful return to Design-review. 7. Product introduction -promotion 8. Follow-up evaluation -Based on feedback changes may be made.
question
Standardization
answer
Extent to which there is an absence of variety in a product, service, or process Products are made in large quantities of identical items Every unit [customer] processed goes through the same process [receives essentially the same service]
question
Standardization Advantages
answer
Fewer parts to deal with in inventory and in manufacturing Reduced training costs and time More routine purchasing, handling, and inspection procedures Orders fillable from inventory Opportunities for long production runs and automation
question
Standardization Disadvantages
answer
High cost of design changes increases resistance to improvements: designs may be frozen with too many imperfections remaining Decreased variety results in less consumer appeal
question
Mass Customization
answer
A strategy of producing basically standardized goods or services, but incorporating some degree of customization in the final product or service Techniques: -Delayed differentiation -Modular design
question
Delayed Differentiation
answer
The process of producing, but not quite completing, a product until customer preferences are known e.g., Produce a piece of furniture, but do not stain it; the customer will choose the stain or personalized M
question
Modular Design
answer
A form of standardization in which components are grouped into modules that are easily replaced or interchanged e.g., PC Advantages -simplification of manufacturing and assembly -relatively low training costs -easier diagnosis and remedy of failures -easier repair and replacement Disadvantages -Limited number of possible product configurations -Limited ability to repair a faulty module; the entire module must often be scrapped
question
Different phases of a products life cycle require different strategies
answer
in all cases, accurate forecasts of demand and cash flow are critical
question
Designing (products) for Production
answer
1. Concurrent engineering 2. Computer-Assisted Design (CAD) 3. Production requirements 4. Component commonality
question
Concurrent Engineering
answer
Bringing design and manufacturing engineers together early in the design phase -manufacturing personnel, marketing and purchasing personnel in loosely integrated cross-functional teams -Views of suppliers and customers may also be sought The purpose: -achieve product designs that reflect customer wants as well as manufacturing capabilities
question
Computer Aided Design (CAD)
answer
Increases designers' productivity. Directly provides information to manufacturing (dimensions, material - BOM). Perform analysis: engineering ,cost. Shortens time-to-market SolidWorks, AutoCad
question
Production Requirements
answer
Designers must take into account production capabilities -Equipment -Skills -Types of materials -Schedules -Technologies -Special abilities When Opportunities and Capabilities do not match management must consider expanding or changing capabilities. Related concepts: a. Design For Manufacturing (DFM) b. Manufacturability c. Design For Assembly (DFA)
question
DFM and DFA
answer
Design for Manufacturing (DFM) -designing products that are compatible with an organization's abilities Manufacturability -Ease of fabrication and/or assembly -Has important implications for cost, productivity and quality Design for Assembly (DFA) -reducing the number of parts in a product and on assembly methods and sequence.
question
Component Commonality
answer
When products have a high degree of similarity in features and components, a part can be used in multiple products Benefits: -Savings in design time -Standard training for assembly and installation -Opportunities to buy in bulk from suppliers -Commonality of parts for repair -Fewer inventory items must be handled
question
Service Design
answer
Begins with a choice of service strategy, which determines the nature and focus of the service, and the target market Key issues in service design -Degree of variation in service requirements -Degree of customer contact and involvement
question
Differences between Service ; Product Design
answer
1. Services are created and delivered at the same time. Less opportunity to correct errors. Training, process design more important. 2. Services cannot be inventoried -; capacity issues. 3. Services are highly visible to consumers. Importance of process design. 4. Service systems range from those with little or no customer contact (similar to product design) to those that have a very high degree of customer contact 5. Location is often important to service design, with convenience as a major factor. 6. Demand variability - time ; requirements - alternately creates waiting lines or idle service resources. Cost and efficiency perspective vs. customer perspective. -Standardizing at the risk of eliminating features that customers value - reduce customer choices (e.g., cable channels bundle) -Increase flexibility by employing temporary workers
question
Challenges to Service Design
answer
Variability Timing. Services cannot be stored. Balancing supply and demand: possible (e.g., doctor's appointments) impossible (e.g., emergency room). Disney's FastPass Difficult to predict customer requirements especially when there is direct contact with the customer.
question
Service Blueprint
answer
a method to design and analyze a service. Steps: 1. Establish boundaries and decide the level of detail needed. 2. Identify and determine the sequence of customer and service actions and interactions. Picture the service from the customer's perspective. 3. Develop time estimates for each phase of the process, as well as time variability. 4. Identify potential failure points and develop a plan to prevent or minimize them, as well as a response plan.
question
Reliability
answer
The ability of a product, part, or system to perform its intended function under a prescribed set of conditions Reliability is expressed as a probability: -The probability that the product or system will function when activated -The probability that the product or system will function for a given length of time
question
The central feature of Taguchi's approach is parameter design.
answer
It focuses on a much smaller subset of possible production environments of standard design of experiments. This can lead to a near optimal solution.
question
Reliability- When Activated
answer
Finding the probability under the assumption that the system consists of a number of independent components Requires the use of probabilities for independent events Independent event Events whose occurrence or non-occurrence do not influence one another
question
Reliability Rule 1
answer
If two or more events are independent and success is defined as the probability that all of the events occur, then the probability of success is equal to the product of the probabilities of the events (#1 works AND #2 works) Overall reliability is less than the least reliable component. Though individual system components may have high reliabilities, the system's reliability may be considerably lower because all components that are in series must function
question
Redundency
answer
One way to enhance reliability is to utilize redundancy, the use of backup components to increase reliability
question
Rule 2
answer
If two events are independent and success is defined as the probability that at least one of the events will occur, the probability of success is equal to the probability that (either) one occurs (it works) plus (OR) 1.00 minus that probability (it fails...) multiplied by the probability the other occurs
question
Rule 3
answer
If two or more events are involved and success is defined as the probability that at least one of them occurs, the probability of success is 1 - P(all fail). 1 - (#1 fails AND #2 fails AND #3 fails) Can also be calculated by using Rule 2 multiple times.
question
Reliability Over Time
answer
Reliabilities are determined relative to a specified length of time.
question
Improving Reliability
answer
Component design Redundancy/backups System design Production/assembly techniques Testing Preventive maintenance procedures User education