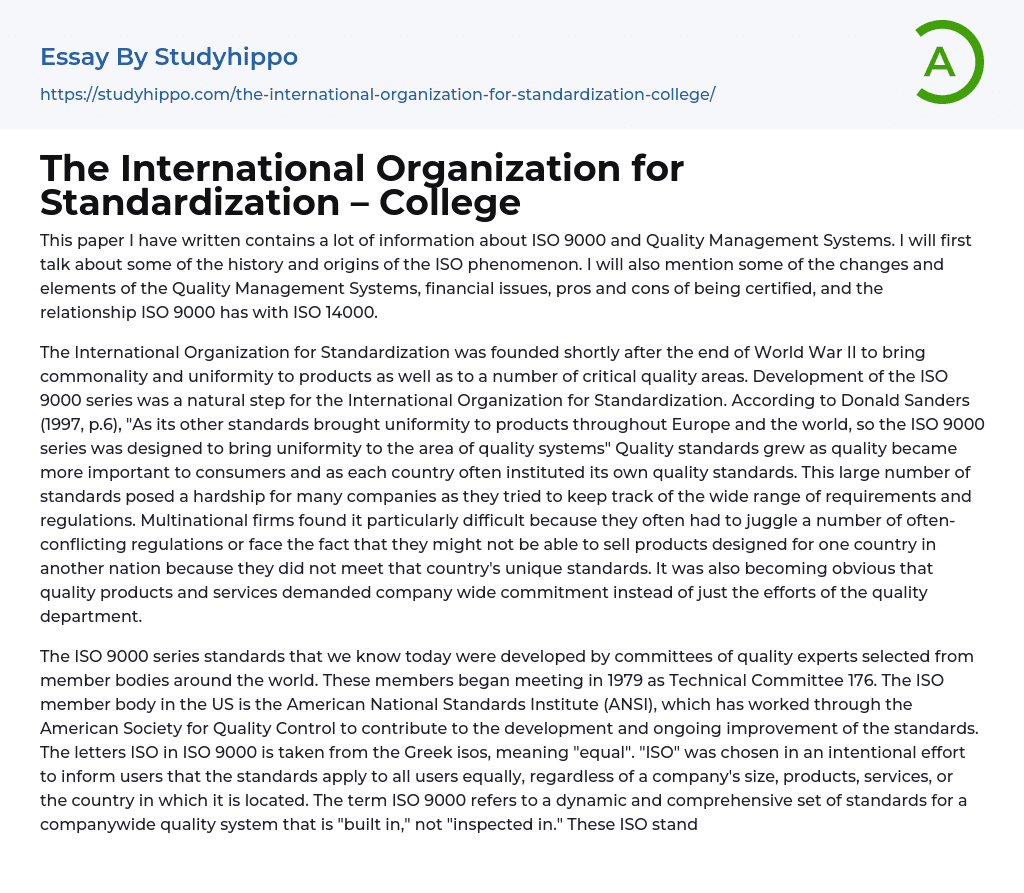
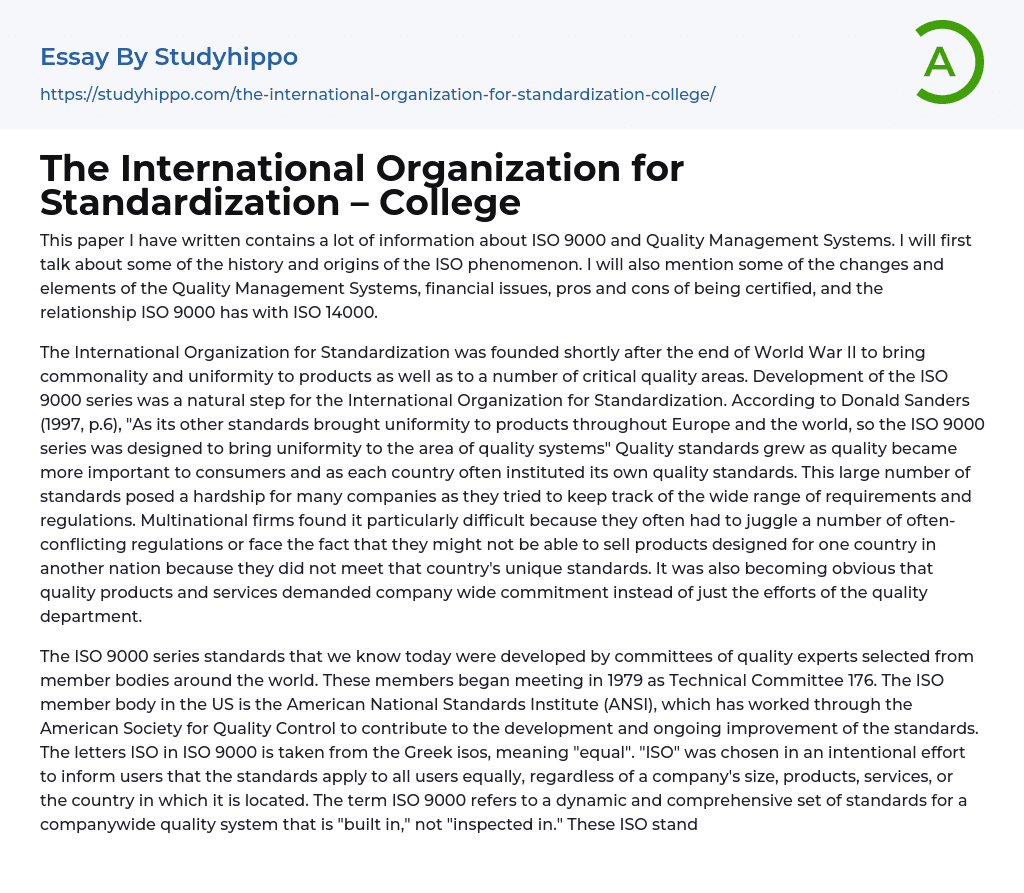
The International Organization for Standardization – College Essay Example
This paper I have written offers extensive information on ISO 9000 and Quality Management Systems, including a discussion on the history and origins of the ISO phenomenon.
The International Organization for Standardization was established after World War II to promote standardization and uniformity in various aspects of quality. This includes the development of the ISO 9000 series, which aims to bring uniformity to quality systems. Donald Sanders (1997, p.6) suggests that the ISO 9000 series was created to achieve the same level of uniformity that other ISO standards have brought to products worldwide. Consequently, quality standards have evolved and become more significant to consumers, leading each country to implement its own quality standards.
The large quantity of standards caused difficulties for many companies as they attempted to keep track of the various requirements and regulations.
...This was especially challenging for multinational firms as they had to manage multiple conflicting regulations, or face the possibility of being unable to sell products designed for one country in another due to not meeting that country's specific standards. Additionally, it became evident that achieving quality products and services required commitment from the entire company, rather than just the quality department. The ISO 9000 series standards, as we now recognize them, were created by committees comprised of quality experts chosen from member bodies worldwide.
These members began meeting in 1979 as Technical Committee 176. The ISO member body in the US is the American National Standards Institute (ANSI), which has worked through the American Society for Quality Control to contribute to the development and ongoing improvement of the standards. The letters ISO in ISO 9000 is taken from the Greek isos, meanin
"equal". "ISO" was chosen in an intentional effort to inform users that the standards apply to all users equally, regardless of a company's size, products, services, or the country in which it is located. The term ISO 9000 refers to a dynamic and comprehensive set of standards for a companywide quality system that is "built in," not "inspected in." These ISO standards are revised and reissued roughly about every six years (Sanders 1997).
The ISO 9000 standards have gone through several revisions. The first set was published in 1987, followed by a revision in 1994, and the most recent update in 2000. These updated standards are collectively known as the "ISO 9000 2000 Standards". Currently, ISO 9000 consists of three quality standards: ISO 9000:2000 (fundamentals and vocabulary), ISO 9001:2000 (requirements), and ISO 9004:2000 (guidelines). When comparing the differences between ISO 9001:1994 and ISO 9001:2000, numerous changes can be observed.
In order to enhance compatibility with the ISO 14001 environmental management standard, ISO has abandoned the previous 20-clause structure of the old standard and reorganized the ISO 9001 standard into 5 sections. This new structure not only ensures a more logical arrangement but also places a greater emphasis on customer orientation. While the previous standard already focused on meeting customer requirements and achieving customer satisfaction, the revised ISO 9001:2000 standard delves into these aspects with enhanced depth and detail.
The new ISO standards require organizations to communicate with customers and monitor their satisfaction. Previously, organizations seeking certification were referred to as "suppliers" because they provided products and services. However, this terminology caused confusion, so the focus is now on the "organization" instead of the "supplier." The term "supplier"
now refers to the organization's supplier, replacing the previous term "subcontractor." Additionally, the new standards allow for certain requirements to be excluded or ignored under special circumstances. These excluded requirements are known as exclusions.
According to ISO, certain requirements in Section 7 Product realization can be ignored or excluded if specific conditions are met. The QMS is comprised of continual improvement, management responsibility, resource management, product/service realization, and measurement, analysis, and improvement. To have a QMS, the organization must establish, document, implement, and maintain it while continuously enhancing its effectiveness. The organization should identify necessary processes, determine their sequence and interaction, establish criteria and methods for operation and control, ensure resources and information availability, monitor and analyze these processes, and take action for planned results and continual improvement.The text below summarizes the requirements for top management's commitment to the development, implementation, and continual improvement of the Quality Management System (QMS), as well as the resources needed for customer satisfaction and process realization.
Top management must provide evidence of its commitment to the QMS through various actions, including communicating the importance of meeting customer, legal, and regulatory expectations, establishing a quality policy and setting quality objectives, conducting management reviews, and ensuring the availability of resources.
The organization must determine and provide the necessary resources to enhance customer satisfaction. These resources can include people, infrastructure, work environment, information, suppliers, natural resources, and financial resources. It's important for these resources to align with the organization's quality objectives.
Additionally, the organization should plan and develop the processes required for product or service realization, ensuring that these processes are in place to meet quality standards.
The planning of product or service realization must align with
the requirements of the other processes in the Quality Management System (QMS). During this planning, the organization needs to determine the following, as appropriate:
- Quality objectives and requirements for the product or service.
- The need to establish processes, documents, and allocate resources specific to the product or service.
- The required verification, validation, monitoring, inspection, and test activities specific to the product or service, as well as the criteria for accepting it. Additionally, records are needed to verify this clause.
Moreover, the organization must plan and implement processes for monitoring, measuring, analyzing, and improving. These processes are necessary:
- To demonstrate conformity of the product or service.
- To ensure conformity of the QMS.
- To continually improve the effectiveness of the QMS.
This process includes determining applicable methods, such as statistical techniques (Besterfield, 2004). The main value of ISO 9000 certification is the ability to consistently deliver a product or service according to a defined standard, which leads to improved bottom line performance. ISO registration also plays a significant role in enhancing market credibility.
Your certification provides access to both domestic and international business opportunities. A quality system that is ISO 9000 certified facilitates clear communication and shared expectations among businesses. Additionally, implementing an ISO certified quality system promotes ongoing enhancement of your products and processes, leading to reduced errors, returns, and customer complaints. Consequently, your investment in ISO 9000 can yield lower transaction costs.
According to (ISO 2004), although
the cost of achieving certification may seem high, it is actually only a small portion of the overall costs of quality, including prevention, appraisal, and failure costs. The cost of certification should be viewed as a prevention cost and an investment towards establishing and maintaining an effective quality management system (Business Link, 2003).
Despite the potential disadvantages, such as high cost and time-consuming documentation and maintenance, some companies may see the return on investment for an ISO 9000 Quality System as occurring within around 2 years, whereas equipment investment typically takes 3 - 10 years to provide a return on investment. Additionally, the ISO 9000 certification process can be lengthy, ranging from months to years depending on the initial compliance state and commitment of those involved. Furthermore, it requires employee buy-in, which may not be favorable for all employees.
Both ISO 9000 and ISO 14000 focus on management approaches, but with different areas of concern. ISO 9000 focuses on quality management and meeting customer quality requirements, controlling processes, and promoting continuous improvement. On the other hand, ISO 14000 addresses environmental management. Despite their differences, both standards share similar fundamental systems like document control, management system auditing, operational controls, recordkeeping controls, management policies, audits, training, and corrective and preventive actions. In order to achieve success, both ISO 9000 and ISO 14000 require support and commitment from senior management, as well as a system for establishing and reviewing objectives and targets. These objectives can be related to either quality or the environment. Additionally, ongoing management review of the system and its objectives is required for both standards (Lamprecht, 1996).
ISO commissioned a year-long study to examine the compatibility between ISO
9000 and ISO 14000 due to their close relationship. To address this matter, Technical advisory group 12 (TAG 12) was established. TAG 12 recommended several actions to improve standards compatibility:
- Ensure that relevant terms and definitions are identical and consistently used in both families of standards.
- Enhance compatibility and alignment between the management system standards of the two families.
- Integrate auditing standards by creating a common core document, supplemented by separate modules on quality and the environment.
In conclusion, ISO 9000's quality management standards are becoming increasingly important as the most significant quality standard. Numerous companies in more than a hundred countries are utilizing it because it effectively manages quality, saves money, meets customer expectations, and is also being used by competitors. "If you want to have a quality attitude you must have a quality system" (ISO, introduction section, page 6, 2004)." ISO 9000 acknowledges this understanding and recognizes its significance.
References
- Besterfield, D (2004) Quality Control. Upper Saddle River, NJ. Pearson Ed. Inc.
- International Org. for Standardization. (2004, October 6). ISO 9000.
Retrieved March 8, 2005, http://www.iso.org
Lamprecht, J (1996) ISO 9000.
Implementaion for business. Milwalkee, WI: ASQL Quality Press
Praxiom Reasearch Group (2005, March 7). ISO Standards. Retrieved March 7, 2005, http://praxio.com
Sanders, D (1997)
Passing your ISO 9000 audit. Boca Baton, FL: St. Lucie Press.
The Business Link (2003, March 11).
What is ISO 9000? Retrieved from http://www.cbsc.org on March 7, 2005.
- Chief Executive Officer essays
- Convenience Store essays
- Firm essays
- Training And Development essays
- Unilever essays
- Variable Cost essays
- Virgin Group essays
- Bargaining essays
- Entity essays
- Pest analysis essays
- Professor essays
- Should College be Free essays
- Should college athletes be paid essays
- College Education essays
- College Tuition essays
- Graduation essays
- College Goals essays
- Personal Statement essays
- Online Classes Vs Traditional Classes essays
- Online Education essays
- Student Loan essays
- Study Abroad Scholarship essays
- Reasons To Go To College essays
- Paying College Athletes essays
- Technology In The Classroom essays
- John Locke essays
- 9/11 essays
- A Good Teacher essays
- A Healthy Diet essays
- A Modest Proposal essays
- A&P essays
- Academic Achievement essays
- Achievement essays
- Achieving goals essays
- Admission essays
- Advantages And Disadvantages Of Internet essays
- Alcoholic drinks essays
- Ammonia essays
- Analytical essays
- Ancient Olympic Games essays
- APA essays
- Arabian Peninsula essays
- Argument essays
- Argumentative essays
- Art essays
- Atlantic Ocean essays
- Auto-ethnography essays
- Autobiography essays
- Ballad essays
- Batman essays