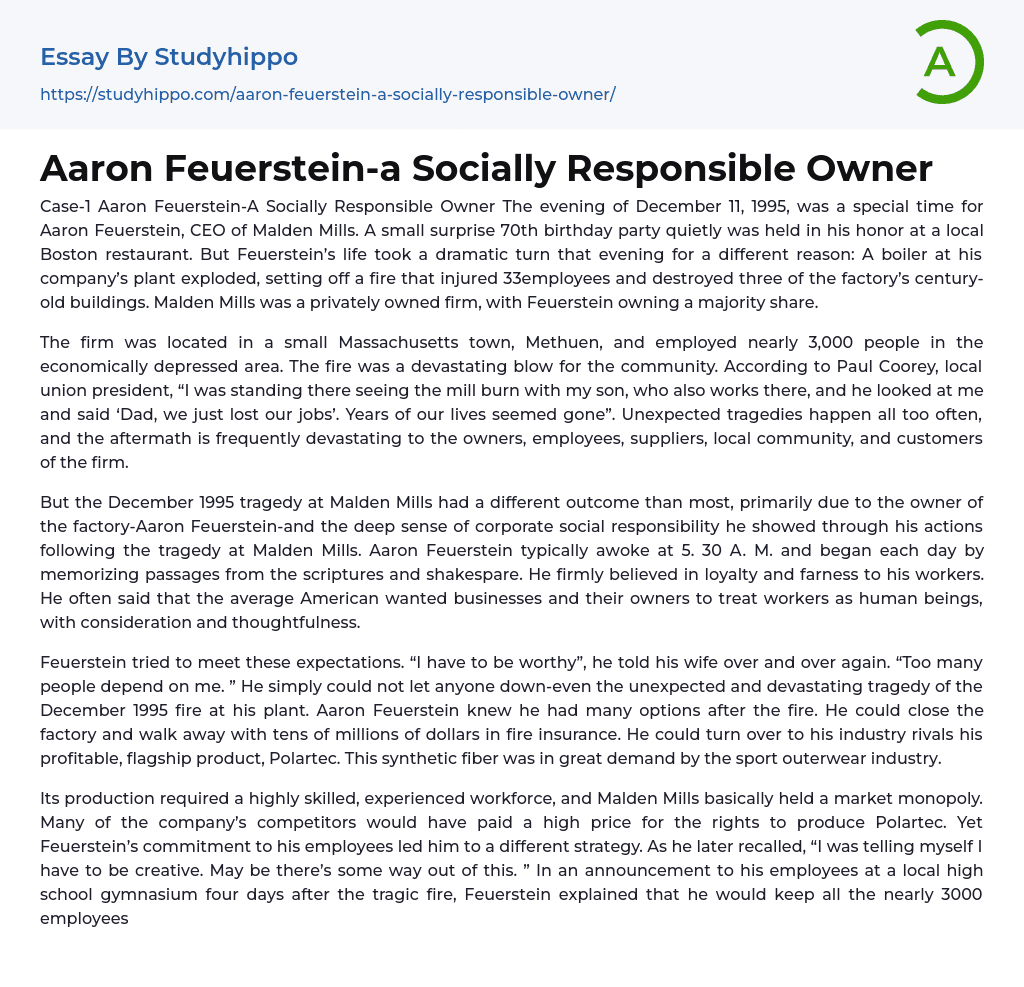
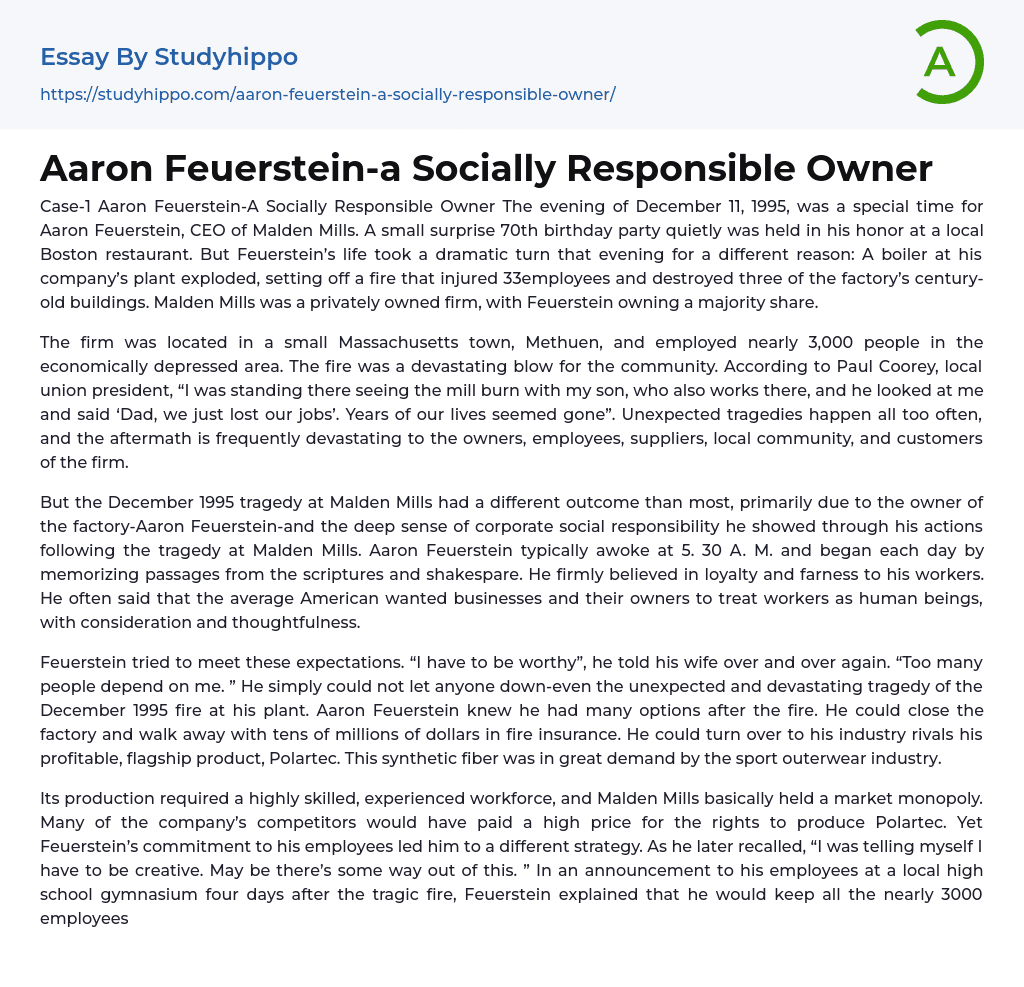
Aaron Feuerstein-a Socially Responsible Owner Essay Example
The evening of December 11, 1995, was a special time for Aaron Feuerstein, CEO of Malden Mills. A small surprise 70th birthday party quietly was held in his honor at a local Boston restaurant. But Feuerstein’s life took a dramatic turn that evening for a different reason: A boiler at his company’s plant exploded, setting off a fire that injured 33employees and destroyed three of the factory’s century-old buildings. Malden Mills was a privately owned firm, with Feuerstein owning a majority share.
The firm was located in a small Massachusetts town, Methuen, and employed nearly 3,000 people in the economically depressed area. The fire was a devastating blow for the community. According to Paul Coorey, local union president, “I was standing there seeing the mill burn with my son, who also works there, and he looked at me and said ‘Dad,
...we just lost our jobs’. Years of our lives seemed gone”. Unexpected tragedies happen all too often, and the aftermath is frequently devastating to the owners, employees, suppliers, local community, and customers of the firm.
But the December 1995 tragedy at Malden Mills had a different outcome than most, primarily due to the owner of the factory-Aaron Feuerstein-and the deep sense of corporate social responsibility he showed through his actions following the tragedy at Malden Mills. Aaron Feuerstein typically awoke at 5. 30 A. M. and began each day by memorizing passages from the scriptures and shakespare. He firmly believed in loyalty and farness to his workers. He often said that the average American wanted businesses and their owners to treat workers as human beings, with consideration and thoughtfulness.
Feuerstein tried to mee
these expectations. “I have to be worthy”, he told his wife over and over again. “Too many people depend on me. ” He simply could not let anyone down-even the unexpected and devastating tragedy of the December 1995 fire at his plant. Aaron Feuerstein knew he had many options after the fire. He could close the factory and walk away with tens of millions of dollars in fire insurance. He could turn over to his industry rivals his profitable, flagship product, Polartec. This synthetic fiber was in great demand by the sport outerwear industry.
Its production required a highly skilled, experienced workforce, and Malden Mills basically held a market monopoly. Many of the company’s competitors would have paid a high price for the rights to produce Polartec. Yet Feuerstein’s commitment to his employees led him to a different strategy. As he later recalled, “I was telling myself I have to be creative. May be there’s some way out of this. ” In an announcement to his employees at a local high school gymnasium four days after the tragic fire, Feuerstein explained that he would keep all the nearly 3000 employees on the payroll for a month while he started to rebuild the family business.
One month later, as the rebuilding process continued at a slow pace, Feuerstein extended it for yet a third month. “What I did was merely the decent thing to do,” he insisted. “The worker is not just a cuttable expense, a pair of hands. I consider the employees the most valuable asset Malden Mills has. ” With the first announcement of guaranteed salaries just days before Christmas, the reactions from employees
were understandably positive. “When he did it the first time, I was surprised,” said Bill Cottor, a 49-year-old Malden Mills employee. “The second time was a shock.
The third…well, it was unrealistic to think he would do it again. ” Nancy Cottor finished her husband’s thought: “It was the third time that brought tears to everyone’s eyes. ” By March 1996, most of the company’s employees were back to work. Those who were not were offered assistance in making other arrangements or finding other employment in the area. Malden Mills’ customers and other local organizations responded to Feuerstein’s actions with an extraordinary outpouring of support. An apparel company, Dakotah, sent Feuerstein a $30,000 check after the fire.
The Bank of Boston donated $50,000, the company’s union sent $100,000, and the Chamber of Commerce in nearby Lawrence, Massachusetts, contributed $150,000. Many of Malden Mills’ customers promised to stick with the company and wait for them to rebuild and regain their production capacity rather than switch to a competitor. Just eight months after the fire, three of the four production lines at Malden Mills were fully operational and all but 500 of the nearly 2,400 employees were back to work in the factory.
But unexpected downturns in the apparel industry challenged the wisdom of Feuerstein’s actions. By 1998, employees at Malden Mills experienced steady layoffs and the firm acquired $120 million in debt. Under the leadership of new chief operating officer Gerald Bowe, following the values of the company’s founder, Malden Mills experienced a turnaround in 1999. Hourly employee recalls numbered 1,500, bringing the total number of employees back to the level at the time of fire.
align="justify">Government and overseas contracts countered the decline in sales in the competitive domestic market, and Malden Mills appeared to be recovering from its financial setbacks as the firm entered the twenty-first century. Aaron Feuerstein’s commitment to both the company’s economic and social mission and goals appeared to have emerged from ashes intact.
Questions:
- Which principle of social responsibility was the basis of Aaron Feuerstin’s actions in the case? Give evidence from the case.
- Which arguments for CSR support Feuerstein’s actions, and which arguments against CSR raise questions regarding his actions?
- Was Feuerstein being responsible to his multiple stakeholders in this case?
Little Enough or Too Much Bryan was recently hired by a large chemical company to oversee the construction of production facilities to produce a new product. X Chemical developed a new industrial lubricant that it felt it could produce at a price close to those of its competitors. The plant to manufacture the lubricant was built on land adjacent to the East River. X chemical had already applied for and received the necessary permit to dump waste materials from the process into the river.
Several other chemical plants in the nearby vicinity are also releasing waste materials into the river. Bryan is concerned because the government agency that oversees the permit process granted X chemical a permit to release more waste into the river than previously anticipated. An additional stage in the production process that would have reduced the waste and recycled some materials became unnecessary due to the regulatory agency’s decision. Because the additional process would have added capital and production costs, it was not built as part of the existing plant. Yet,
X chemical has always stated publicly that t would do all that it could to protect the environment from harmful materials.
The company has had mediocre performance for several quarters, and everyone is anxious to see the new product do well. Tests have shown it to be a top-quality industrial lubricant that can now be produced at a cost significantly below those of their competitors. Orders have been flowing in, and the plant is selling everything it can produce. Morale in the company has increased significantly because of the success of the new product. Due to the success of the new product, all employees are looking forward to sizable bonuses from the company’s profit sharing plan.
Bryan is upset that the company failed to build the additional stage on the plant and fears that the excess waste released today will cause problems for the company tomorrow. Bryan approaches Bill Gates, the plant supervisor, with his concerns. Bill replies, “It’s up to the government agency to protect the river from excess waste, and the company only had to meet the agency’s standards. The amount of waste being released poses no threat to the environment, according to the agency. The engineers and chemists who originally designed the production process must have been too conservative in their estimates.
Even if the agency made a mistake, the additional recycling and waste reduction process can be added later when it becomes necessary. At this point, building the additional process would require costly interruptions in the production process and might cause customers to switch to our competitors. Hence, environmental group might become suspicious if the production was stopped to add the
additional process-They might see it as an admission of wrongdoing. No one in the company wants to attract any unwarranted attention from the environmental groups. They give us enough trouble as it is.
The best thing we can do is make money while the company can and deals with issues as they come up. Don’t go trying to cause trouble without any proof. The company doesn’t like troublemakers, so watch your step. You’re new here, and you wouldn’t want to have to find a new job. ” Bryan is frustrated and upset. He can see all the benefits of the new product, but inside he is sure the company is making a short-sighted decision that will hurt them in the long run. The vice president of operations will tour the plant next week, and Bryan is considering approaching the officer with his concerns.
- Auction essays
- Balanced Scorecard essays
- Business Plans essays
- Expense essays
- Income essays
- Net Income essays
- Security Guard essays
- Singapore Airlines essays
- Battle essays
- Intranet essays
- Maintenance essays
- Simulation essays
- Inn essays
- Chief Executive Officer essays
- Convenience Store essays
- Firm essays
- Training And Development essays
- Unilever essays
- Variable Cost essays
- Virgin Group essays
- Bargaining essays
- Entity essays
- Pest analysis essays
- Nightclub essays
- Leadership and Management essays
- Change Management essays
- Project Management essays
- Knowledge Management essays
- Operations Management essays
- Quality Management essays
- Risk Management essays
- Scientific Management essays
- supply chain management essays
- Performance Management essays
- Time Management essays
- Brand Management essays
- Total Quality Management essays
- Risk essays
- Manager essays
- Leadership essays
- Business Ethics essays
- Board Of Directors essays
- Product Management essays
- Comparative Analysis essays
- Decision Making essays
- Dispute Resolution essays
- Stress Management essays
- Business Management essays
- Brand Equity essays
- Branding essays
Unfortunately copying the content is not possible
Tell us your email address and we’ll send this sample there.
By continuing, you agree to our Terms and Conditions.