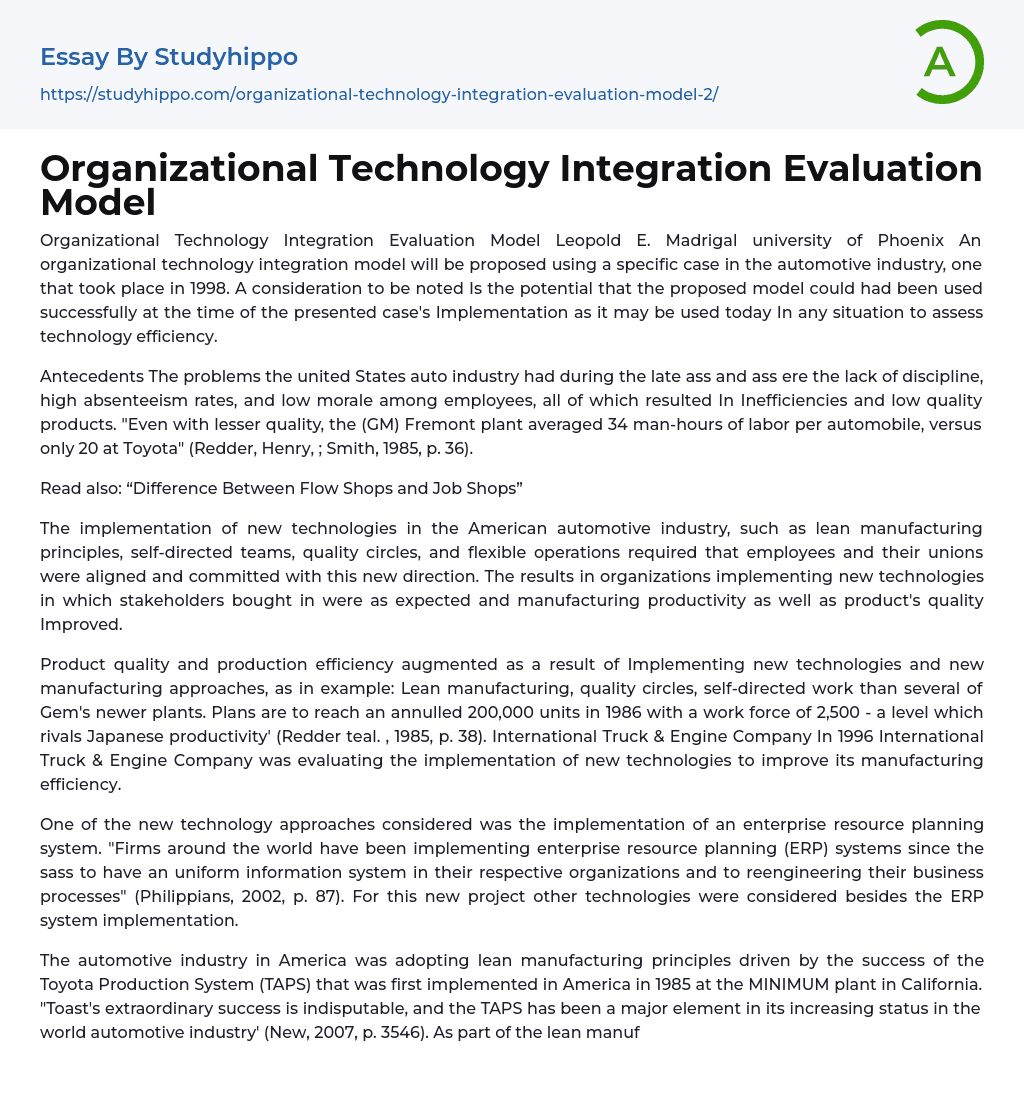
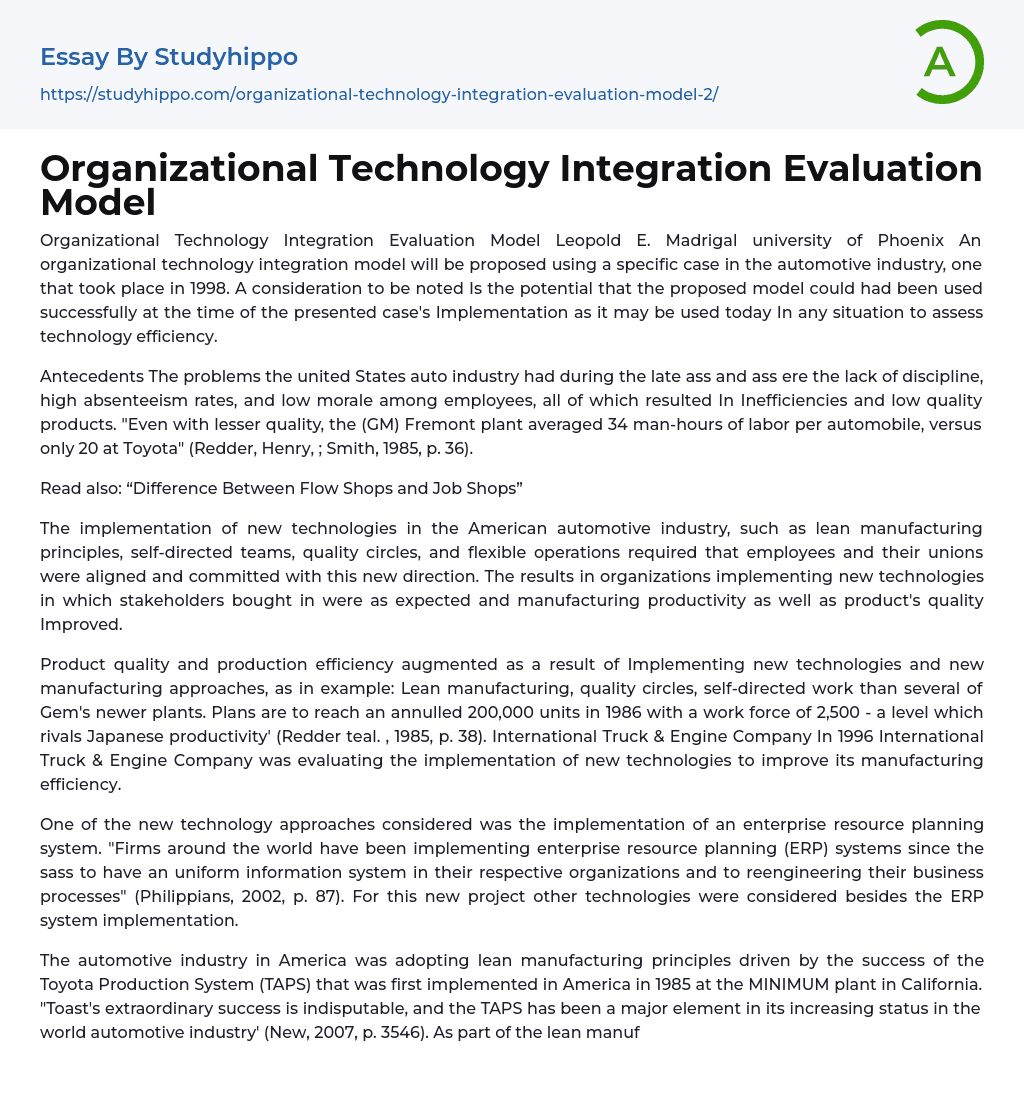
Organizational Technology Integration Evaluation Model Essay Example
The University of Phoenix introduces the Organizational Technology Integration Evaluation Model, created by Leopold E. Madrigal. This model is derived from a case study in the automotive industry in 1998. It is important to mention that this model was effective during that time and remains applicable for evaluating technology efficiency in any context today.
In the late 20th century, the auto industry in the United States faced various challenges. These included a lack of discipline, high absenteeism rates, and low employee morale. As a result, inefficiencies arose and low-quality products were produced. According to Redder, Henry, and Smith (1985), the GM Fremont plant took an average of 34 man-hours to build one automobile compared to Toyota's average of only 20 man-hours.
Also, read "Difference Between Flow Shops and Job Shops".
The successful implementation of new technologies in the
...American automotive industry, such as lean manufacturing principles, self-directed teams, quality circles, and flexible operations, depended on the alignment and commitment of employees and their unions. Organizations that had stakeholders who supported these new technologies saw improvements in manufacturing productivity and product quality.
The implementation of new technologies and manufacturing approaches, such as Lean manufacturing, quality circles, and self-directed work, resulted in increased product quality and production efficiency. This improvement was observed in several of Gem's newer plants. The company plans to reach a production level of 200,000 units in 1986 with a workforce of 2,500, which is comparable to Japanese productivity (Redder teal., 1985, p. 38). In 1996, International Truck & Engine Company was considering the adoption of new technologies to enhance its manufacturing efficiency.
One potential technological approach for the new projec
was the implementation of an enterprise resource planning (ERP) system. According to Philippians (2002), organizations worldwide have been implementing ERP systems since the sass to establish a consistent information system and streamline their business processes (p. 87). In addition to the ERP system, other technologies were also considered for this project.
The automotive industry in America began adopting lean manufacturing principles inspired by the success of the Toyota Production System (TAPS), which was first implemented in America at the MINIMUM plant in California in 1985. The remarkable success of TAPS has significantly contributed to the global automotive industry's recognition of Toyota (New, 2007, p. 3546). As part of the lean manufacturing initiatives, the goal was to create a new organizational structure that empowered employees and fostered teamwork through self-directed work groups. Our research revealed that highly empowered teams are more effective than less empowered ones (Kirkland & Russell, 1999, p. 69). This initiative represented a departure from the conservative management approach previously adopted by the organization in terms of shop-floor operations. Another decision was made to construct a new facility that adhered to lean manufacturing principles, such as ensuring modular assemblies flow directly to their intended production point in a specific sequence.
According to Oldenburg, Roman, ; Terra (2007), in an attempt to reduce production costs, numerous U.S. companies choose to manufacture their products in countries with cheaper labor. Thus, a new facility is planned to be established in Mexico. However, aside from the already existing challenge of assembling an experienced team for this venture, the complexity is further heightened by the need to incorporate new technologies.
The introduction of new technologies included implementing new
technical designs for manufacturing and new conceptual designs for manufacturing processes. These changes were made in conjunction with adopting lean manufacturing initiatives, which involved implementing new management practices like self-directed work groups. Additionally, a new ERP system was also implemented. As part of the lean manufacturing approach, based on the Toyota Production System (TAPS), various changes were made in the assembly system. This included transforming the anal assembly into a mixed model final assembly system to balance demand on suppliers, restructuring the linear subassembly lines into U-shaped subassembly cells, and redesigning the job shop into manufacturing cells.
Final assembly has a take' time, and the cells are designed to have a cycle time slightly less than the take' time and to operate on a 'make one, check one, and move one on'(MO-CO-MOO strategy. The task involved planning the implementation strategy, constructing a new facility in a foreign country with lean manufacturing principles, hiring a dervish team for the new facility, implementing a new ERP system for the organization, and being able to start production of trucks built at other facilities to relieve capacity restrictions and reduce manufacturing costs.
In summary, the implementation team had three primary focuses: 1) the manufacturing system, 2) human integration into the new manufacturing design (also known as a socio-technical system), and 3) utilizing the ERP system as an enabling technology. Throughout the process of designing and implementing the manufacturing system, it was crucial for the team to acknowledge its significance as a vital component within any manufacturing company.
The manufacturing system, as described by Black (2007, p.3643), is a complex arrangement of physical elements. It involves the design and implementation
of self-directed work groups and a multi-task development program linked to a payment structure. The individuals working within this system are considered "internal customers", so the system must be designed to meet their needs. Additionally, it must also produce products that satisfy the needs of "external customers" (Black, 2007, p.43).
An ERP system is viewed as a means to enhance performance. These systems consist of functional modules like materials management, production planning, sales and distribution, human resources, and financial accounting. These modules are based on best practices that represent the most cost-effective and efficient methods for carrying out business processes (Sackbut & Subliminal, 2006, p.7).
By establishing a new facility with new management and personnel, the organization gains advantages in addressing change management issues. Change management is primarily seen as an issue within human resource management.According to Bananas (2009,p236), this is because implementing new procedures or technologies and overcoming resistance to change are primarily people-related tasks.
The organization invests in technology with the expectation that it will meet future business needs and those of customers and stakeholders. Technological innovation creates value and improves the efficiency of producing existing products and services (Shame, 2009, p. 7).
The organization set several expectations for the implementation of new technologies. These included increasing the medium duty truck assembly capacity by 120 units per day and increasing the heavy duty assembly capacity by 60 units per day. They also aimed to reduce the man-hours per truck by 10% and reduce the cost of direct labor by 70%. Additionally, they wanted to implement an ERP system that would integrate information from all performance and assemblies. The organization planned to limit online stocking areas
by designing narrow aisles along the assembly lines and implement quality circles and multi-ability development programs for their employees. Lastly, they aimed to improve the quality of the product by minimizing end-of-line defects-per-truck. As for the 'soft' systems technologies related to people, every individual would have to go through a specific training program to be certified for three assembly stations.
The belief is that a certified person should be able to work without making mistakes at line speed (taking time). The lean system is designed to produce high-quality products. Toyota believed in company-wide total quality control and taught it to everyone from the company president to every production worker. They were able to transform from a company that made low-quality products to one that could provide customers with highly reliable products (Black, 2007, p.3644). The implementation of the ERP system represented another technological improvement, and although no clear measures of success were established, there were some beliefs about the outcome. Typical benefits of ERP systems mentioned in the literature include inventory and lead time reductions, improved on-time deliveries, reduced operating costs, enhanced customer relationships (Hit et al., 2002), and improved decision making" (Sackbut Subliminal, 2006, p.49). By March 1998, the new facility had started operations, albeit on a limited basis. Only one of the two assembly lines was ready for truck assembly, while the other assembly line, cab fabrication, and paint areas were still being prepared for production. The materials flow design and the use of Kanata and assembly mod were already in place. The new personnel seemed comfortable with the processes, procedures, tools, and systems they were using. The ERP system was already in
a production environment.
The organization had concerns about the situation at the new assembly plant. They had invested millions of dollars to improve production efficiency, product quality, and manufacturing costs. However, there were issues with trucks reaching the end of the assembly line without all their parts and a lack of available materials at both the plant and point of use. This led to stopping and redesigning the production ramp-up plan to address assembling incomplete trucks that needed rework in the proper storage area. Identifying the root causes was challenging due to unknown variables for manufacturing experts from other plants.
The organization was faced with a challenge in a new manufacturing facility. The facility operated according to the principles of lean manufacturing and had new processes, new systems, and inexperienced staff. Moreover, it was located in a foreign country with a different way of doing business. The problem at hand was that the assembly facility could not produce five trucks a day without missing some components, which affected the missing request planning (MR.). As a result, the trucks had numerous defects at the end of the assembly line, making it undesirable to increase production to the planned 30 units per day by April 1998.
The evaluation of improvements in man-hours per truck or manufacturing cost reductions was challenging due to the lack of "clean" trucks. Additionally, the assembly line's top line speed with the new installed capacity could not be fully tested because of numerous missing components. To assess the effectiveness of technology implementation at the new assembly facility, it is necessary to test each of the different technologies implemented starting from planning and designing
stages through pre-production and implementation. After completing these tests, an integration test between the different technologies must be conducted before testing the overall system.
During the process, different performance levels are examined to determine whether the new technologies are suitable for meeting the expected outcomes outlined in the original concept of the new facility. Any discrepancies identified during unit, integration, or system tests are analyzed to assess the need for design changes, additional capabilities, or adjustments to expectations. To evaluate the effectiveness of technology implementation, the situation is assessed using principles from general systems theory (SST). This involves comparing the desired state of the system with its current state. "General systems theory is a model that portrays certain general aspects of reality.
According to Bertelsmann (1972, p. 424), viewing things from a fresh perspective and considering previously overlooked aspects serves as both a way of seeing and a methodological maxim. This paper aims to introduce a tool for assessing the effectiveness of technology implementation, which was not utilized in the described situation. Nonetheless, the GIST tool will be integrated to validate design and performance. The new facility implemented multiple technologies with each intended to function properly. Subsequently, these technologies underwent comprehensive testing together to ensure flawless performance and successful integration as an overall system.
Bananas (2009) proposed a methodology consisting of three stages of testing: 1) Unit testing, 2) Integration testing, and 3) system testing. According to Thompson (2003), the assessment table can be used to test different technology components by evaluating the completeness of cause/effect knowledge beliefs and comparing them with desired standards. Tennyson & Isis (2011) also support this approach and emphasize the
importance of identifying performance problems and finding solutions. By using Thompson's assessment techniques, one can define the desired state and output of the system (standards of desirability) and compare it with the current state to identify root causes. To achieve this, an ideal technology implementation should implement a V model life cycle test. The V model ensures that each deliverable is verified for defects and guarantees complete and correct specifications.
The V model life cycle consists of several stages that must be completed in sequence according to Bananas (2009, p. 274). These stages include: 1) defining reasons for testing, 2) acknowledging structure testing, 3) testing and verification at the design stage, 4) testing within a system implementation, and 5) testing with a system maintenance environment. Bananas (2009) also presents a diagram of Thompson's (2003) technology assessment table which outlines beliefs about cause/effect knowledge standards of desirability, completeness, uncertainty, crystallized efficiency test, ambiguous extrinsic measures, and organizational rationality.
The proposed methodology follows a specific flow, which is presented in the following table. It involves different stages such as defining performance at the ideal and testing states, understanding and verifying testing, and implementation and maintenance within a system environment. Each technology component is evaluated throughout the V model life cycle, starting as a unit and then interacting with other technologies to form a complete system. To assess their performance, the test results are objectively compared to the ideal state, and specific goals may be set. The Thompson assessment table can be used to evaluate each stage based on the standards of desirability and efficiency.
According to the University of Phoenix (2012), when standards are clearly defined but
beliefs are lacking, the assessment of effectiveness is determined by achieving a desired state. In situations where standards are uncertain, but beliefs are complete, external measures such as relying on someone else's opinion are used. Conversely, when standards are unclear and beliefs are incomplete, a predetermined organizational measure is utilized. It is crucial to note that the success of any assessment methodology relies on accurately defining the expected outcomes of a technology implementation. These outcomes should be clarified during the design stage to determine if the technology can deliver them.
As the implementation progresses from design to integration of technologies, it undergoes testing in various pre-production environments. These validation tests must be done based on either objective measurements or expectations that have solid foundations and are attainable. Overall, the proposed technology implementation effectiveness assessment tool can be applied in any technology implementation situation. One crucial factor for the success of the assessment is having a clear and objective understanding of what is expected from the implementation. Defining performance parameters during the design phase will provide guidance for the assessment, assuming those parameters fall within the technology's capabilities. The technology implementation discussed in this paper was completed by September 1999.